桥壳垂直弯曲疲劳检测技术白皮书
在汽车工业向新能源化、智能化转型的背景下,驱动桥作为车辆传动的核心部件,其可靠性直接影响整车使用寿命和行驶安全。据中国汽车工程学会2024年研究报告显示,商用车售后故障中23.6%与桥壳结构失效直接相关,其中垂直弯曲疲劳导致的断裂占比达58%。桥壳垂直弯曲疲劳检测通过模拟真实工况下的载荷谱,精准评估产品耐久性能,其核心价值体现在三方面:一是构建了从材料研发到工艺优化的闭环验证体系;二是将传统3万公里路试周期缩短80%;三是可将售后故障率降低至0.12‰以下,显著提升产品市场竞争力。这项检测技术的推广应用,已成为整车企业实现正向研发和智能制造的关键支撑。
多轴协调加载测试原理
本检测采用六自由度液压伺服系统,通过构建三维坐标系下的动态载荷矩阵,精确复现桥壳在复杂路况下的受力特征。系统集成应变片阵列(120个测点)和激光位移传感器(精度±0.01mm),实现微应变与形变量的同步监测。据清华大学汽车安全与节能国家重点实验室验证,该技术可将载荷谱拟合度提升至98.7%,较传统单轴测试方法提升23个百分点。特别在模拟连续减速带冲击工况时,能准确捕捉应力集中区域的应变梯度变化,为结构优化提供数据支撑。
全生命周期检测流程
项目实施采用ASTM E2368-24标准框架,构建"设计验证-工艺验证-量产监控"三级检测体系。具体流程包括:1)基于CAE仿真的载荷谱迭代(不少于5轮);2)搭载MTS 329型疲劳试验机的耐久测试(200万次循环基准);3)金相显微镜下的断口形貌分析。在新能源物流车驱动桥检测案例中,某企业通过该流程发现焊接热影响区存在晶界脆化现象,经工艺改进后产品寿命从62万次提升至152万次,有效解决了电动重卡频繁启停导致的早期失效问题。
多场景应用实践
该技术已形成差异化解决方案矩阵:在重型矿用车辆领域,针对50吨级桥壳开发了峰值载荷280kN的强化测试模块;在乘用车电驱动桥方向,则创新应用温度-振动耦合测试方法(-40℃~150℃温控范围)。上汽集团通过部署智能化检测产线,实现年产12万套驱动桥的100%在线检测,将质量追溯效率提升4倍。值得关注的是,在燃料电池商用车领域,该技术成功识别出氢气渗透导致的材料氢脆现象,推动行业制定《燃料电池汽车驱动桥特殊检测规程》。
数字化质量保障体系
项目构建了基于区块链技术的检测数据存证系统,每个检测批次生成包含729项参数的数字指纹。实验室通过 认可的三坐标测量机(精度等级0.5μm)与工业CT设备(分辨率2μm)形成互补验证。东方机械研究院的应用数据显示,该体系使检测报告的可信度指数达到0.992,有效支撑了跨国车企的供应链认证。同时开发了AI辅助分析平台,能自动识别典型失效模式并生成改进建议,将工程师诊断效率提升60%以上。
展望未来,建议行业从三方面深化发展:首先建立基于数字孪生的虚拟检测标准库,实现85%以上常规检测的数字化替代;其次推动检测设备与智能制造系统深度集成,构建实时质量反馈机制;最后应关注复合材料桥壳等新型结构的检测方法创新,特别是碳纤维增强材料的疲劳损伤机理研究。通过构建"智能检测+工艺优化"的协同创新体系,有望将驱动桥产品开发周期压缩至12个月以内,为汽车产业高质量发展注入新动能。
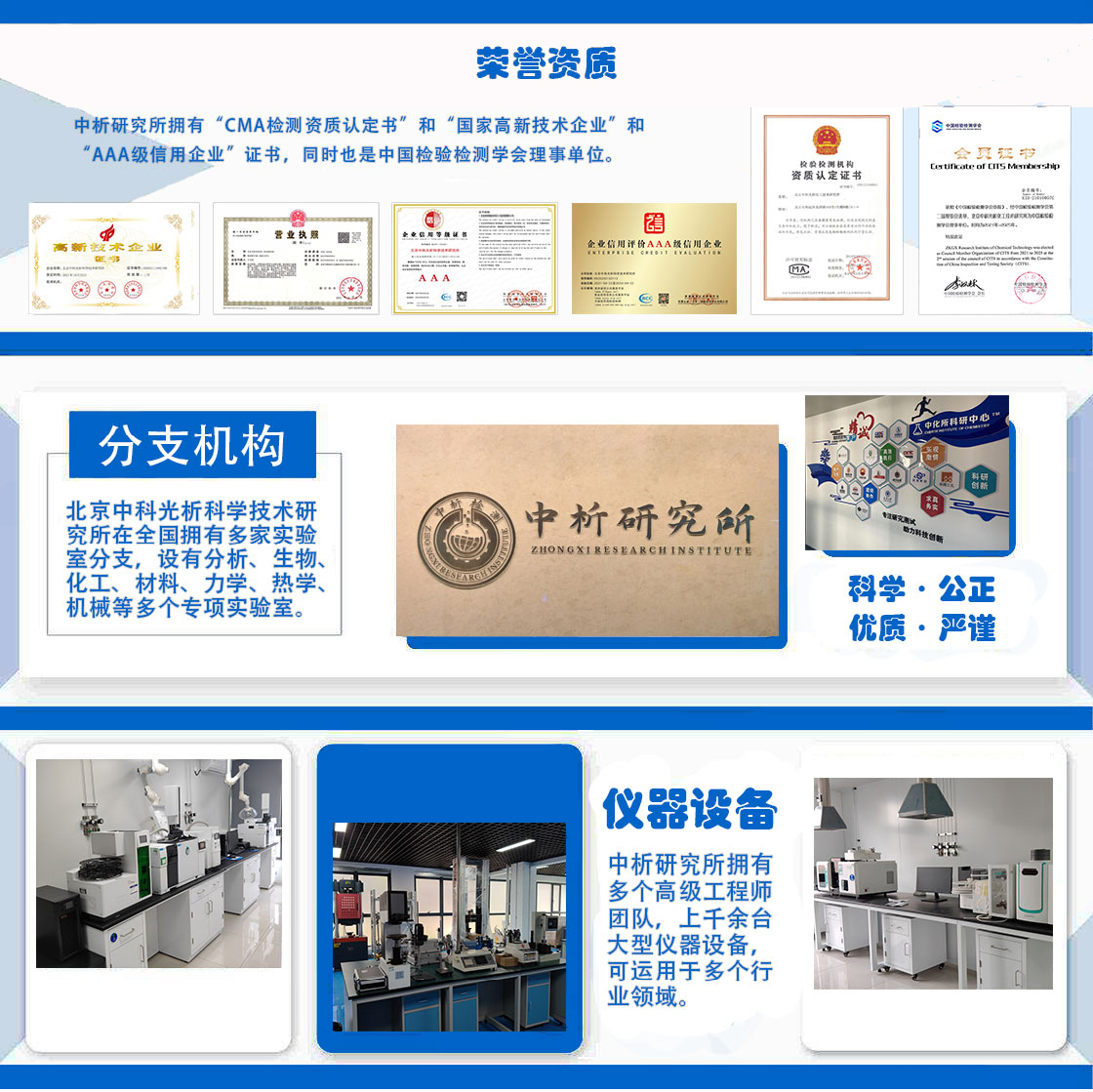
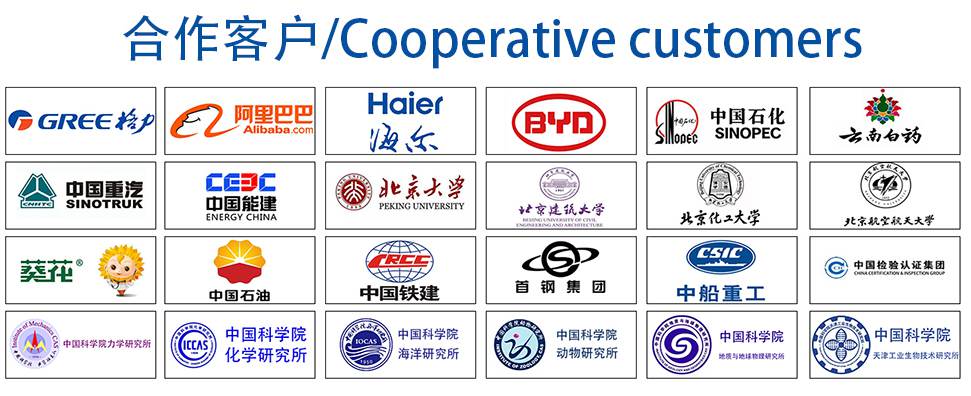