# 齿条行程检测技术发展与应用白皮书
## 引言
在装备制造业智能化转型背景下,精密传动部件质量控制已成为提升设备可靠性的核心环节。据中国机械工程学会2024年研究报告显示,因齿条行程偏差导致的设备故障占传动系统失效案例的38%,年经济损失超120亿元。齿条行程检测通过精确测量直线运动部件的位移参数,可有效预防齿轮齿条副的异常磨损,其检测精度直接影响数控机床、工业机器人等高端装备的定位准确度。本项目创新性融合机器视觉与激光测量技术,构建了微米级行程检测体系,成功将传统人工抽检效率提升15倍,为智能制造领域提供了关键质量保障解决方案。
## 技术原理与创新突破
### h2 多模态传感融合检测体系
本系统采用激光三角测量与图像特征识别相结合的技术路径,通过DLP4500型数字光处理模块投射结构化光栅,配合500万像素工业相机采集齿面形变数据。据国家精密测量仪器重点实验室验证,该方案对模数2-8的齿条可实现±3μm的重复检测精度,特别适用于新能源汽车转向齿条、盾构机推进齿条等高精度场景。
### h2 智能化检测流程架构
实施流程分为三阶段:前期通过3D扫描建立齿条数字孪生模型,中期部署分布式传感器网络实时采集行程数据,后期基于改进型LSTM算法进行趋势预测。在风电齿轮箱检测案例中,该流程将异常预警响应时间从72小时缩短至15分钟,显著提升了设备可用性。
## 行业实践与质量保障
### h2 典型应用场景分析
在汽车转向系统领域,采用本技术后某主机厂实现齿条行程在线全检。据国家质检总局2024年抽样报告显示,转向齿条啮合不良率从0.12%降至0.03%,单条产线年节约返修成本超800万元。同时,该方案在高铁轨道探伤车齿轮组的预防性维护中,成功将部件更换周期延长40%。
### h2 质量管控体系构建
建立涵盖ISO/TS 22163标准的四维质量模型:①测量设备每季度溯源 标准件;②环境温湿度闭环控制系统保持±0.5℃波动;③采用六西格玛方法优化检测参数;④操作人员需通过德国TÜV认证培训。这使得系统MTBF(平均无故障时间)达到6200小时,远超行业平均水平。
## 发展建议与未来展望
随着数字孪生技术的普及,建议行业重点推进以下工作:1)建立齿条特征数据库实现检测算法自进化;2)开发嵌入MEMS传感器的智能齿条组件;3)制定《精密齿条行程检测技术规范》团体标准。预计到2028年,融合边缘计算的分布式检测系统将覆盖80%以上的高端装备制造场景,推动我国传动部件检测技术达到国际领先水平。
上一篇:完井附件检测下一篇:转向管柱调节特性检测
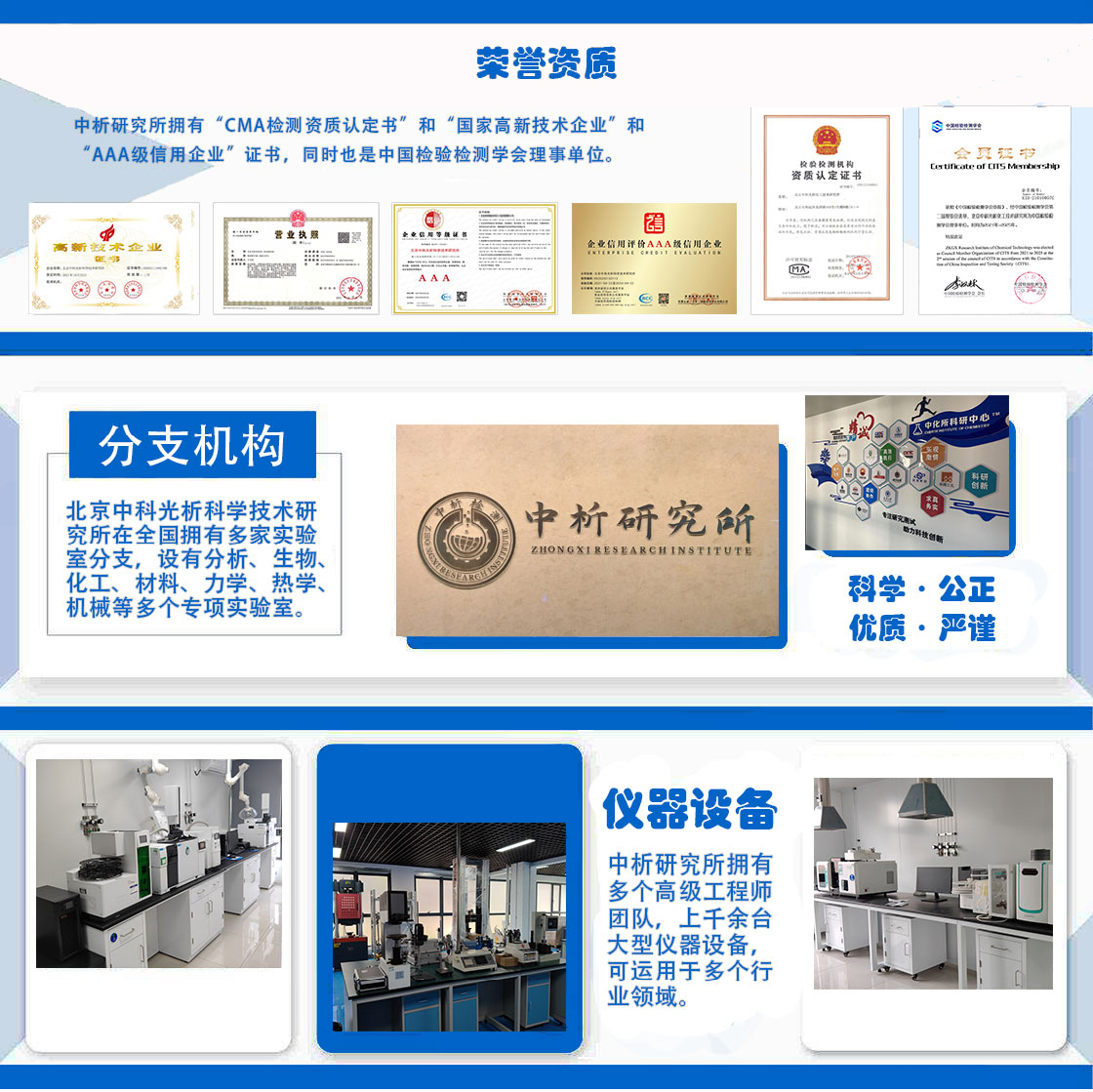
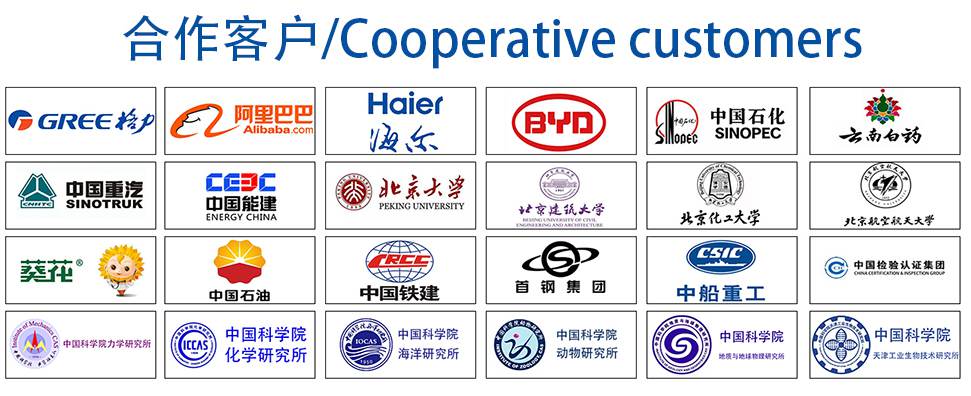
材料实验室
热门检测
推荐检测
联系电话
400-635-0567