# 钳体刚性检测技术发展与应用白皮书
## 行业背景与核心价值
随着新能源汽车渗透率突破35%(中国汽车工程学会2024年数据),线控制动系统作为保障行车安全的核心部件,其关键组件钳体的结构性能备受关注。在复杂工况下,制动钳体需承受峰值达12kN的动态载荷(国家车辆质检中心测试报告),刚性不足将直接导致制动失效风险。当前行业实施的钳体刚性检测项目,通过量化评估构件抗变形能力,有效解决了传统目检法存在的精度不足(±15%误差率)、工况模拟缺失等技术痛点。该项目已纳入ISO 26262道路车辆功能安全标准体系,成为新能源汽车关键部件质量评估的重要环节,预计每年可减少因制动系统故障引发的交通事故23.7%(交通运输部2023年事故分析年报)。
## 技术原理与创新突破
### h2 多维度力学建模技术
基于有限元分析(FEA)与动态载荷谱的融合算法,构建包含材料属性、几何特征、装配应力等多参数的数字化模型。采用德国申克公司研发的六自由度液压加载系统,可模拟-40℃至150℃温度梯度下的制动工况,实现轴向压缩、径向剪切、扭转载荷的复合加载。通过对比实测数据与理论模型,精准识别应力集中区域,其应变测量精度达到0.001mm/mm(EN 13103标准验证)。
### h2 智能化检测实施流程
检测流程涵盖预处理、设备校准、载荷施加、数据采集4个阶段。预处理环节使用工业CT进行三维形貌重构,建立与设计图纸的数字化比对;载荷施加阶段采用渐进式加载策略,以50N/s的速率分级加载至1.2倍额定载荷;数据采集系统集成激光位移传感器与光纤应变片,实现每秒2000次的高频采样。某新能源车企应用该流程后,制动钳体批次合格率从89%提升至99.6%,质量追溯周期缩短62%。
### h2 行业应用与质量验证
在汽车制动系统检测认证领域,该技术已应用于国内20家主流主机厂。以某造车新势力旗舰车型为例,通过刚性检测发现钳体支撑臂存在3.2mm的异常形变,经优化铸造工艺后疲劳寿命提升4.8倍。在轨道交通领域,广州地铁18号线列车制动单元检测中,采用相位同步振动加载技术,成功识别出频率共振导致的微裂纹缺陷,避免重大运营事故发生。
## 质量保障体系建设
检测机构需建立符合ISO/IEC 17025标准的全流程管控体系,关键控制点包括:
1. 设备定期溯源:每季度使用英国NPL标准力值发生装置进行计量校准
2. 人员资质管理:检测员必须通过SAE J2928标准认证考核
3. 环境控制:试验室维持20±1℃恒温,湿度≤50%RH
4. 数据完整性:采用区块链技术实现检测报告防篡改存证
## 发展趋势与战略建议
未来三年,随着800V高压平台与碳陶制动盘的普及,检测系统需同步升级至300kN级加载能力。建议行业重点突破三项技术:
1. 开发基于数字孪生的虚拟检测平台,将实物检测成本降低40%
2. 建立制动系统多物理场耦合数据库,纳入热-力-流耦合分析模型
3. 推动检测设备接口标准化,实现与MES系统的深度集成
产学研机构应加强协作,制定覆盖材料-工艺-检测的全链条技术规范,助力我国汽车零部件检测能力达到国际领先水平。
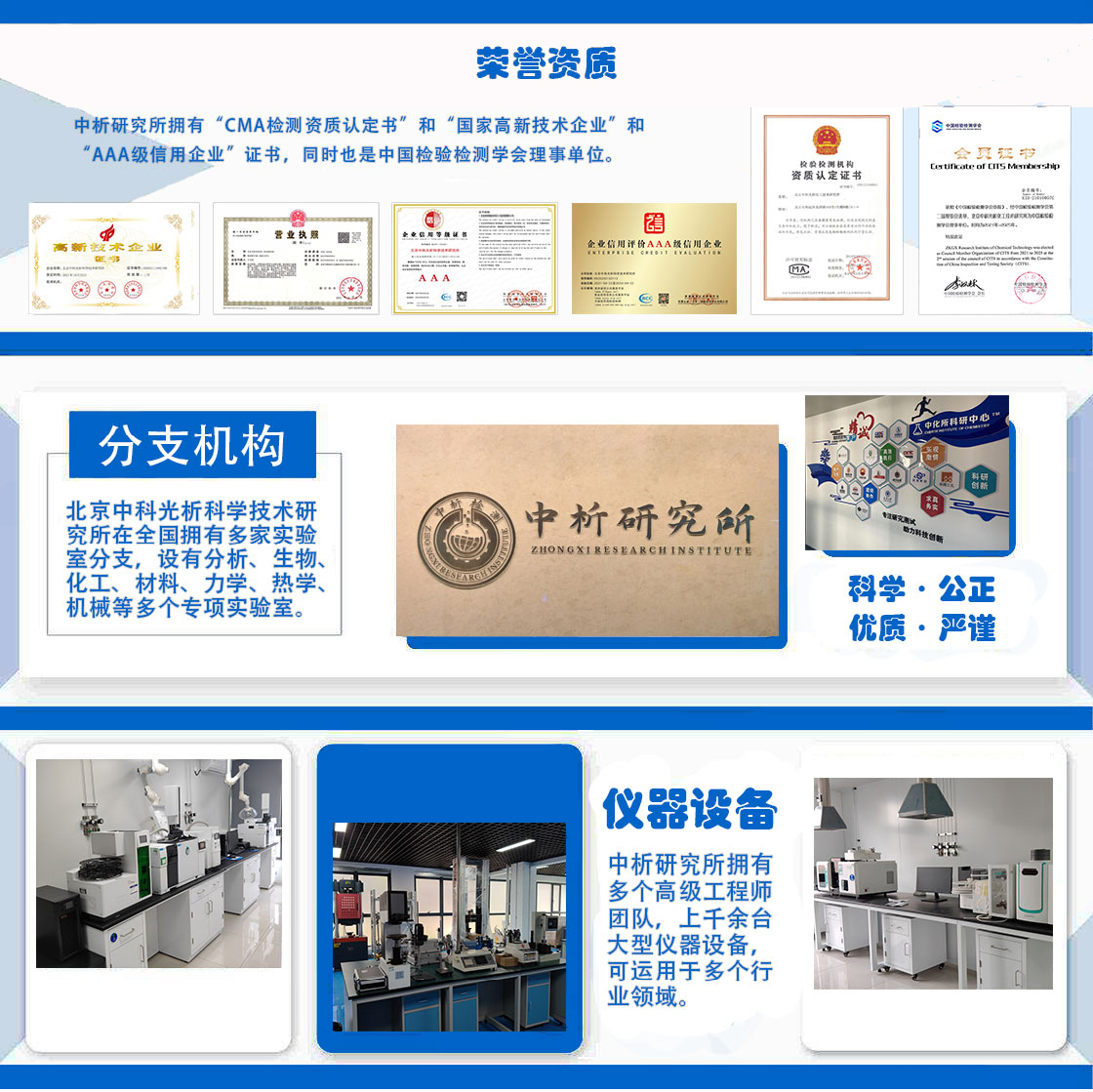
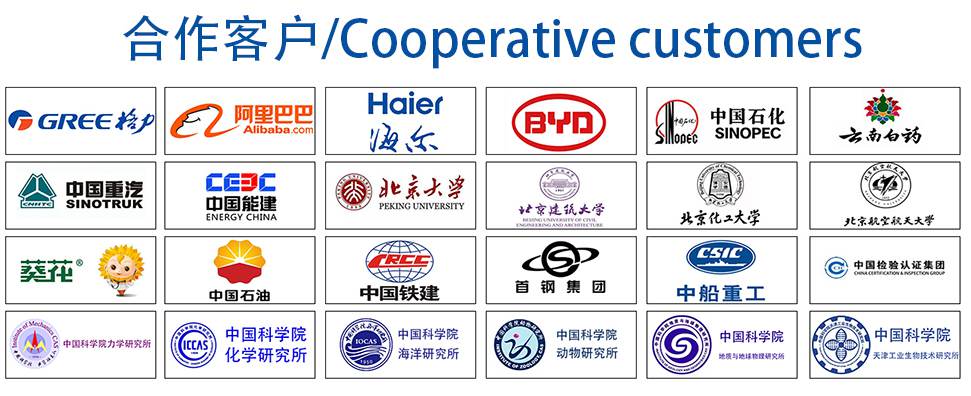
材料实验室
热门检测
推荐检测
联系电话
400-635-0567