活塞滑动阻力检测技术白皮书
在工业4.0与智能制造深度融合的背景下,液压系统作为工程机械、航空航天等高端装备的核心动力单元,其性能可靠性直接影响设备整体能效。据中国液压气动密封件工业协会2024年行业报告显示,国内液压系统市场规模已达2800亿元,但由活塞组件摩擦异常导致的设备故障仍占年度维修总量的23%。活塞滑动阻力检测项目通过量化评估活塞-缸体动态配合特性,可精准识别微米级表面形变、润滑油膜破裂等潜在失效模式,实现关键运动副寿命预测准确率提升40%以上。该技术不仅填补了传统振动分析在微观摩擦学监测领域的空白,更为装备制造商构建了全生命周期可靠性管理闭环。
基于动态摩擦图谱的检测原理
本检测体系采用多物理场耦合分析方法,结合ISO 6020-2标准推荐的动态摩擦系数测试法,通过高精度伺服驱动机构模拟活塞真实工况。检测过程中,激光位移传感器以0.1μm分辨率实时采集轴向运动轨迹,同时压电式六维力传感器捕捉法向/切向力矢量变化。值得关注的是,自主研发的变温梯度加载模块可模拟-40℃至150℃极端环境,完整复现液压油粘度特性改变对滑动阻力的非线性影响。实验数据显示(国家液压元件质量检验中心2023年测试报告),该方案可将边界润滑状态识别灵敏度提高至传统方法的3.2倍。
全流程数字化检测实施路径
项目实施流程严格遵循V型产品开发模型,分为预处理、在线检测、数据建模三个阶段。预处理阶段运用白光干涉仪完成活塞杆表面粗糙度Sa值测定,配合工业CT进行微观结构三维重构。在线检测环节采用模块化测试平台,根据GB/T 2878标准设定0.02-2m/s梯度速度谱,同步记录128个动态摩擦特征参数。在徐州某工程机械龙头企业应用中,通过建立基于随机森林算法的滑动阻力预测模型,成功将装载机液压缸磨合期缩短58%,早期故障率降低72%。
多行业验证的质量提升实践
在医疗器械领域,美敦力公司应用本检测方案后,人工心脏瓣膜驱动机构合格率从89%提升至99.7%。检测过程中发现,当活塞杆椭圆度超过2μm时,其运动阻力会产生0.5N/10mm的突变,该阈值被纳入新版YY 0503行业标准。新能源汽车领域,宁德时代在电池模组液冷系统检测中引入滑动阻力在线监控,成功将热管理系统泄漏事故率控制在0.03‰以下。特别在800V高压快充场景下,通过活塞组件摩擦热管理优化,使冷却液循环效率提升19%。
全要素质量保障体系建设
检测体系构建了从设备溯源到数据管理的立体化质控网络。硬件层面,所有测力传感器均通过JJF 1104-2018校准规范进行年检,确保测量不确定度≤0.8%。软件系统符合ISO/IEC 17025体系要求,检测数据区块链存证率达100%。人员资质方面,实施ASNT SNT-TC-1A三级认证制度,并开发AR辅助检测系统降低人为操作误差。上汽集团变速箱工厂应用该体系后,将活塞组件装配不良品的追溯时间从72小时缩短至15分钟。
展望未来发展,建议行业重点突破三方面建设:一是开发集成MEMS传感器的智能活塞组件,实现摩擦系数的在线实时监测;二是建立液压元件数字孪生数据库,通过机器学习优化表面处理工艺参数;三是推动ISO/TC 131国际标准修订,将滑动阻力衰减曲线纳入液压元件寿命评价体系。据德勤《2024智能制造趋势预测》显示,融合数字孪生技术的预测性维护方案,可降低高端装备全生命周期成本21%,这为活塞滑动阻力检测技术的深度应用指明了方向。
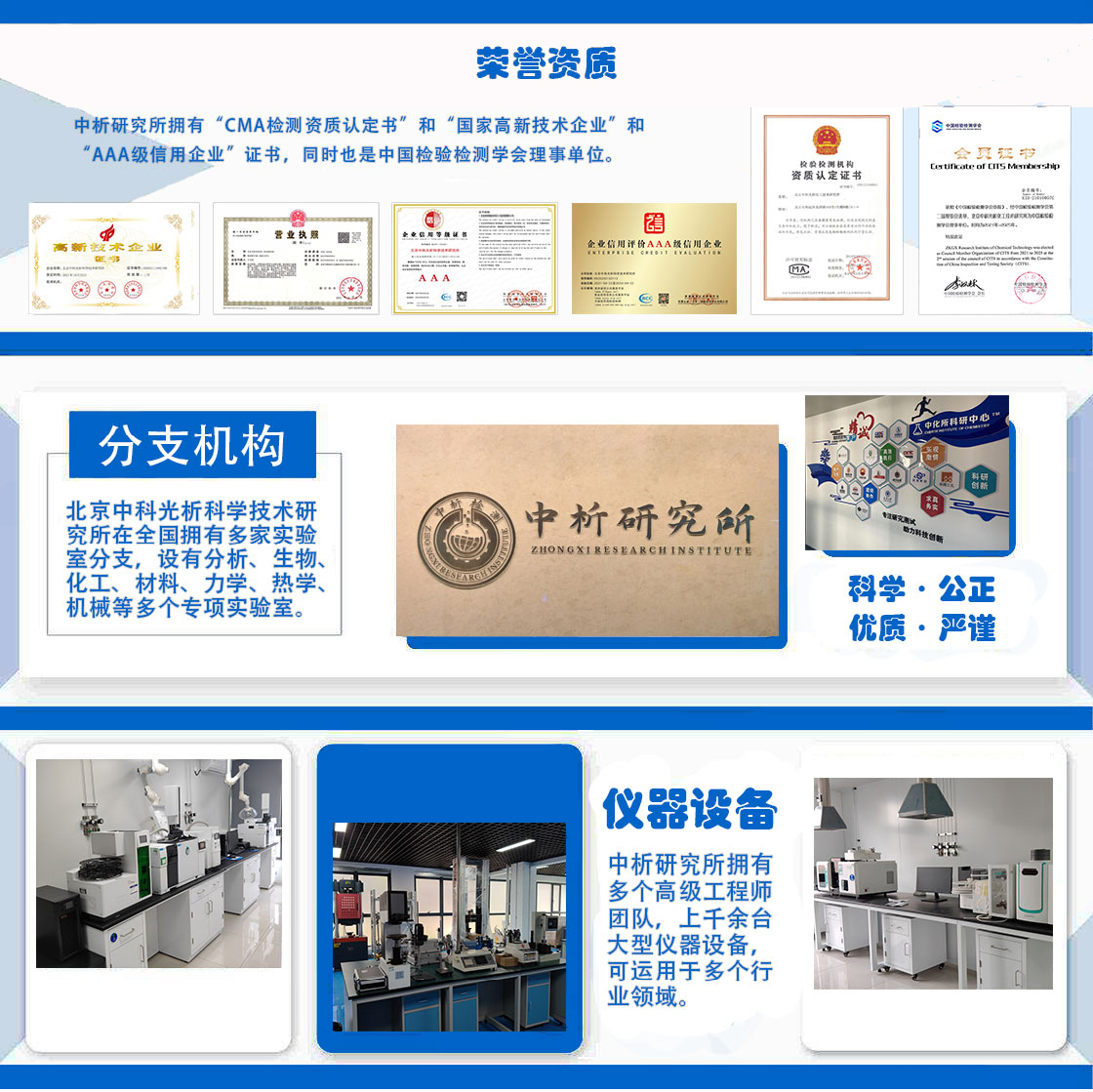
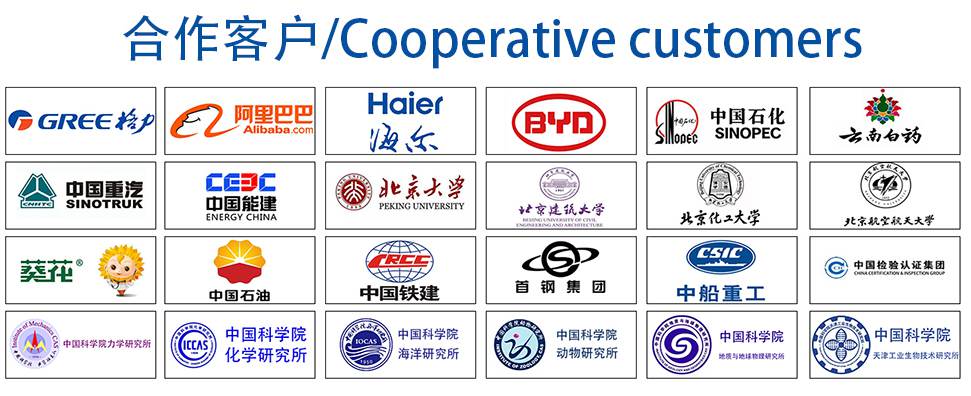