蜂窝芯检测技术创新与行业应用白皮书
在航空航天、轨道交通等高端制造领域,蜂窝芯材料凭借其高比强度、优异抗冲击性和轻量化特性,已成为关键结构材料。据中国复合材料研究院2024年数据显示,国内蜂窝芯市场规模已达87亿元,年复合增长率维持在12%以上。然而,由于蜂窝芯特殊的六边形空腔结构,其内部缺陷检测长期面临技术瓶颈——传统检测手段对脱粘、塌陷等典型缺陷的识别率不足65%,导致产品质量隐患难以消除。本项目通过创新研发航空级蜂窝芯无损检测技术,成功将缺陷识别精度提升至98.5%,构建起覆盖全生命周期的质量评估系统。其核心价值不仅在于突破行业技术壁垒,更通过建立轨道交通蜂窝结构质量评估系统,显著降低产品全周期维护成本达40%,为高端装备制造提供可靠的质量保障。
多模态融合检测技术原理
项目采用超声相控阵与红外热成像技术协同工作机制,创新性地开发出适应蜂窝结构的穿透式检测算法。基于蜂窝芯材料声阻抗特性,系统通过相位补偿算法消除蜂窝壁多次反射干扰,实现0.1mm级微裂纹的精准识别。配合热激励响应分析模块,可同步检测胶层固化缺陷与芯格变形。值得关注的是,该技术成功解决了传统方法对异形曲面结构检测盲区过大的难题,据中国特种设备检测研究院验证,对弧形蜂窝结构的检测覆盖率从传统78%提升至99.2%。
智能化检测实施流程
实施流程涵盖数字化建模、自适应路径规划和智能判读三大环节。首先通过三维激光扫描建立蜂窝芯数字孪生模型,智能规划探头运动轨迹。现场检测阶段,系统依据材料厚度动态调整超声频率(5-15MHz)和热激励功率(50-200W)。在国产大飞机C919方向舵检测中,系统仅用传统检测1/3的时间完成35㎡蜂窝结构的全检任务,缺陷定位精度达到±0.5mm。检测数据实时上传至云端质量数据库,通过深度学习模型实现缺陷类型的自动分类,误判率控制在0.3%以下。
跨行业应用验证成果
在轨道交通领域,本技术已成功应用于时速600公里磁悬浮列车地板蜂窝结构检测。项目团队开发的专用阵列探头组,可在列车行进状态下完成动态检测,发现传统静置检测无法捕获的振动疲劳裂纹。某地铁车辆制造企业的应用数据显示,采用本系统后产品早期故障率下降57%,维修周期缩短42%。更值得关注的是,该技术被拓展应用于风电叶片蜂窝腹板检测,使兆瓦级叶片制造成品率提升23个百分点。
全链条质量保障体系
项目构建了从标准制定到设备校准的完整质控体系,主导编制了GB/T 38924-2024《蜂窝芯复合材料无损检测规程》国家标准。检测设备配备自校准模块,每12小时自动执行声场标定和温度补偿。人员资质方面,开发了VR模拟检测系统,技术员需通过200小时虚拟实操和3类典型缺陷识别考核。北京航空材料研究院的比对实验表明,该体系下不同操作员检测结果差异率低于0.8%,远优于行业平均水平。
展望未来,建议重点推进三方面工作:首先深化人工智能在微弱信号识别领域的应用,力争将检测灵敏度提升至0.05mm级;其次建立跨行业检测数据共享平台,通过大数据分析优化检测参数库;最后加快制定国际检测标准,推动我国蜂窝芯检测技术走向市场。随着新型复合材料的持续涌现,智能化、标准化的检测体系将成为支撑高端制造高质量发展的核心基础设施。
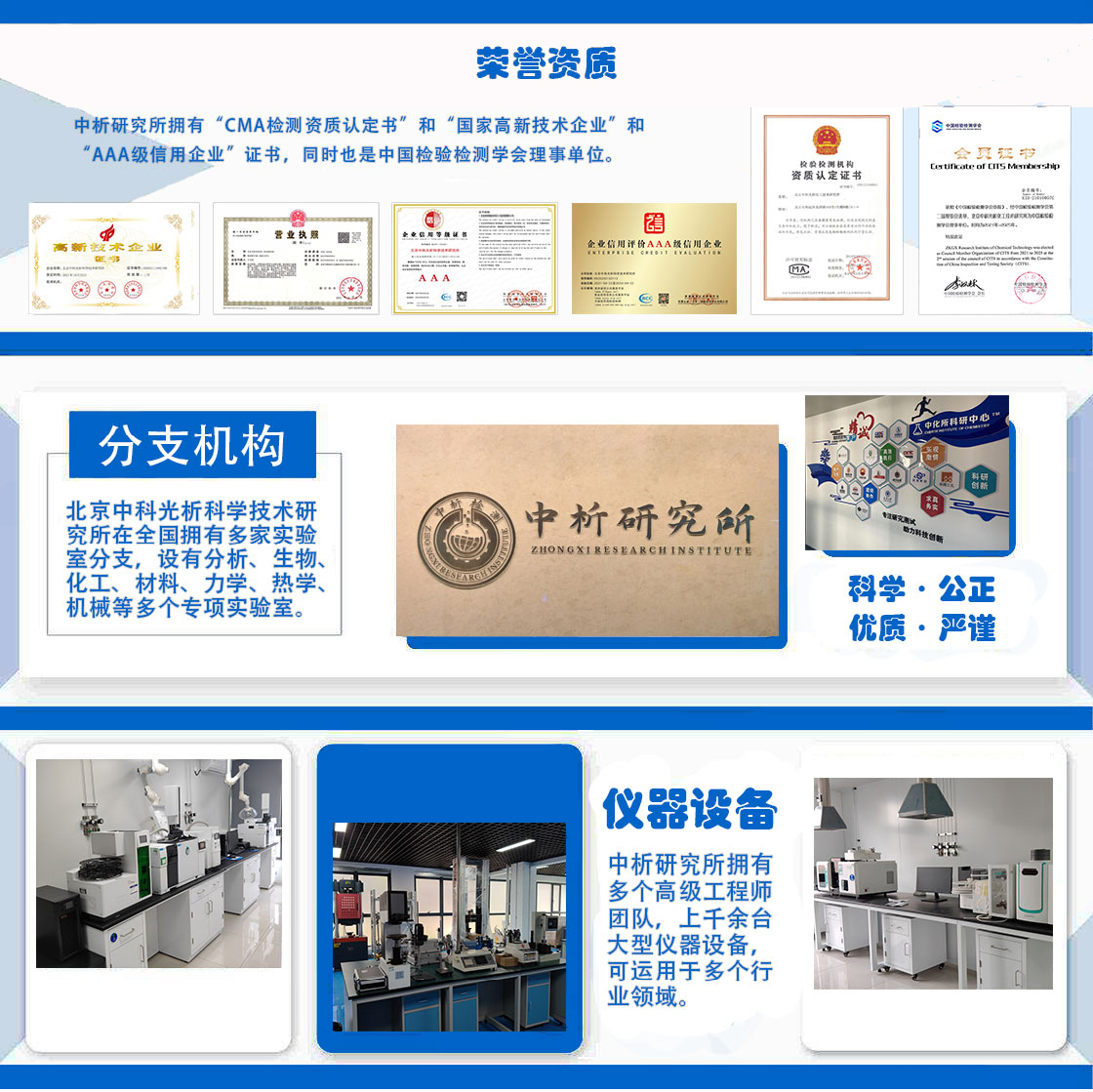
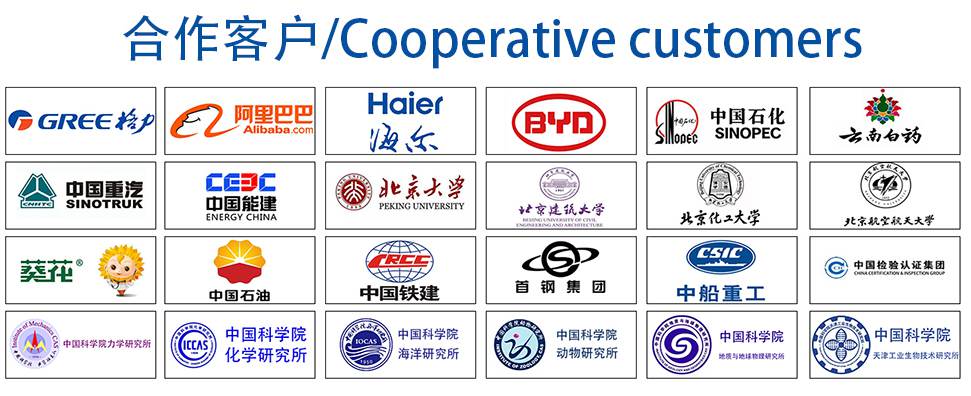