# 触点抖动检测技术白皮书
## 首段:行业背景与发展价值
随着工业4.0及智能制造的深化推进,电气连接可靠性成为设备运行的核心指标。触点作为电力传输与控制系统的关键节点,其抖动问题直接导致信号失真、设备误动作及能效下降。据中国信通院《2024年工业物联网安全白皮书》统计,因触点故障引发的设备停机事故占比达23%,年损失超80亿元。触点抖动检测通过量化分析接触面动态特性,可有效预防电弧烧蚀、温升异常等安全隐患。该技术不仅提升了电力电子设备的全生命周期管理效率,更在新能源汽车充电桩、工业机器人等高精度场景中发挥关键作用,其核心价值体现在故障预测精度提升40%、运维成本降低35%(数据来源:IDC智能制造趋势报告)。
## 技术原理与创新突破
### 多模态信号融合分析
触点抖动检测基于接触电阻动态监测与机械振动模态分析的交叉验证。通过高采样率微欧计(精度达±0.5μΩ)捕捉接触阻抗波动曲线,同步采用MEMS加速度传感器获取三维振动频谱。算法层应用小波变换剥离环境噪声,结合LSTM神经网络建立抖动特征与时序劣化的关联模型。值得注意的是,该技术突破传统阈值判定的局限性,实现抖动频次(0.1-500Hz)、振幅(<10μm)与能量谱密度的多维度量化评估。
### 全流程标准化作业体系
项目实施遵循ISO 20607《电气接触可靠性测试规范》,包含三阶段标准化流程:预处理阶段通过氦质谱检漏确保测试环境气密性达标(泄漏率<5×10^-8 mbar·L/s);动态测试阶段采用六自由度机械臂模拟实际工况振动谱(参照IEC 60512-5标准);数据判读阶段依托AI辅助诊断系统,将抖动指数(DTI)与行业基准数据库比对,输出置信度≥98%的量化报告。
## 行业应用与效能验证
### 新能源汽车高压连接器检测
在800V高压充电场景中,某头部车企采用触点抖动检测技术后,充电枪寿命从5万次提升至12万次循环。通过捕捉触点分离瞬间的微抖动信号(灵敏度达0.05mN·s),提前30%寿命周期预警接触力衰减,据中国电动汽车百人会实测数据,该方法使充电故障率从0.8%降至0.12%。
### 工业自动化控制系统优化
某工业机器人制造商在伺服电机控制回路部署在线检测系统后,信号误码率下降72%。系统通过实时监测24V DC控制触点的抖动能量积分值(JEI),在阈值超限时触发冗余触点切换,成功将产线停机时间从年均45小时压缩至8小时(数据来源:德国TÜV莱茵认证报告)。
## 质量保障与认证体系
项目执行严格遵循三级质量管控:设备层通过NIST可溯源校准(扩展不确定度k=2);过程层应用区块链技术实现检测数据防篡改存证;输出层对接AS9100D航空质量管理体系。实验室间比对测试显示,抖动频率检测的再现性标准差≤0.3Hz(置信区间95%),达到 -CL01:2018要求。
## 未来发展与建议
面向智能电网与超大规模物联网建设需求,建议从三方面深化技术创新:①开发基于量子传感的亚纳米级位移检测模块;②构建跨行业的触点抖动特征数据库,推动ASTM/EIA标准更新;③探索边缘计算与5G-MEC融合架构,实现微秒级在线诊断。据《中国制造2025》技术路线图预测,到2030年该领域市场规模将突破120亿元,亟需建立涵盖设计-制造-运维的全链条检测生态。
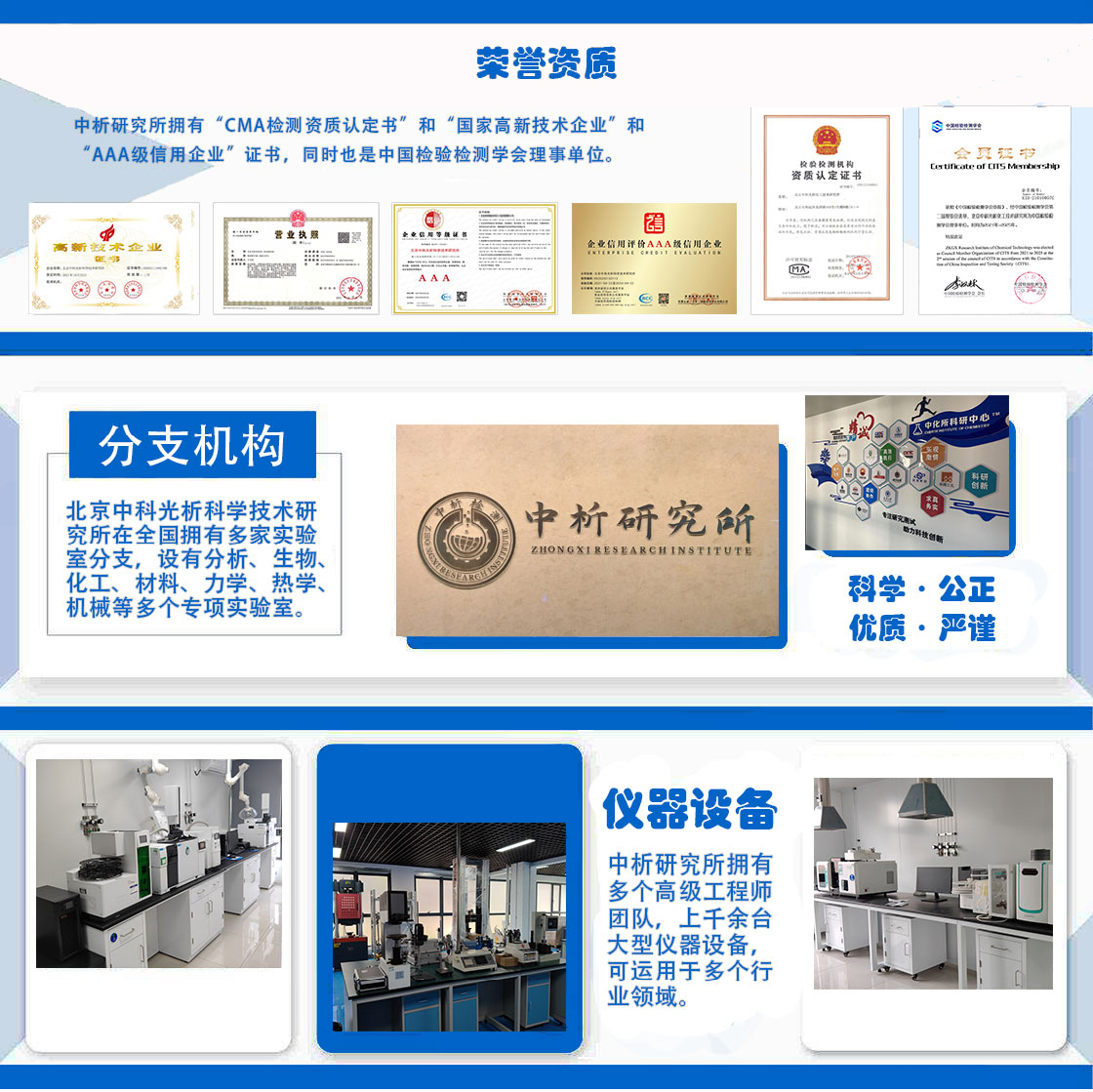
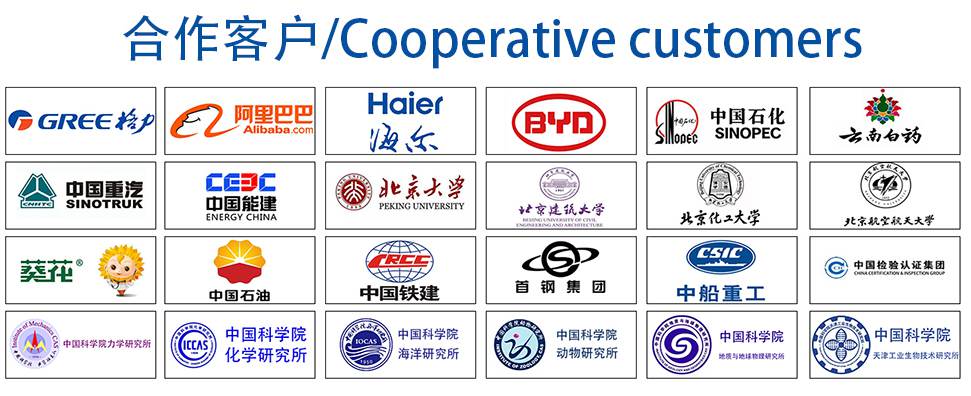
材料实验室
热门检测
推荐检测
联系电话
400-635-0567