起泡剂通过在气液界面形成稳定膜结构降低表面张力,其核心性能指标包括发泡体积(≥450mL/g)、半衰期(>120s)及携液能力(>85%)。检测体系依托ASTM D3519标准改进方案,采用动态循环模拟装置重构井下温度(80-150℃)、压力(5-25MPa)环境,结合高速摄像技术捕捉泡沫结构演变过程。值得注意的是,针对高温高压气井起泡剂稳定性检测需求,创新引入分子动力学模拟技术,可提前预判药剂在复杂地层条件下的失效阈值。
### 标准化检测实施流程完整的检测流程分为四个阶段:首齐全行药剂基础物性分析,包括pH值、密度及粘度测定;继而开展静态泡沫性能试验,获取初始发泡能力数据;随后在高温高压反应釜中进行动态模拟测试,重点考察压力波动对泡沫稳定性的影响;最终通过气液两相流实验验证实际携液效率。特别需要强调的是,检测过程需严格遵循SY/T 6465-2023行业标准,所有设备均通过 认证,确保数据可比性与国际互认。
### 行业典型应用案例在川南页岩气区块的现场应用中,某企业通过实施"页岩气开发用环保型起泡剂评价"项目,将返排液处理成本降低28%。具体而言,检测团队针对3000米深水平井的微裂缝特征,筛选出耐盐性(Cl⁻耐受>15wt%)与抗凝析油污染(含油量<5%时性能衰减<8%)的双效起泡剂,使单井日产气量提升19%(西南油气田2023年生产报告)。另一典型案例是塔里木高温气田,通过建立"井筒温度-压力梯度检测模型",成功将泡排作业周期从72小时延长至120小时。
### 全过程质量保障体系检测机构构建了三级质量控制系统:初级检测采用自动化仪器减少人为误差,中级验证通过平行样比对确保重复性误差<3%,终级评审引入区块链技术实现数据溯源。值得关注的是,针对页岩气开发用环保型起泡剂评价,实验室创新开发了生物毒性快速检测模块,可在30分钟内完成EC50值测定,满足日益严格的环保监管要求。所有检测报告均附带QR质量追溯码,客户可通过数字平台实时调阅原始实验数据。
## 发展建议与未来展望 面向"十四五"油气开发智能化转型目标,建议从三方面深化检测体系建设:首先构建区域性智能检测网络,将现场快速检测设备与云端数据库互联;其次加强高含硫气田专用起泡剂检测标准研制,填补现行标准在极端工况下的技术空白;最后推动检测结果与数字孪生系统融合,实现泡排作业参数的实时优化。通过技术创新与标准升级双轮驱动,预计到2026年可将我国起泡剂检测技术标准覆盖率提升至95%,为非常规油气资源高效开发提供坚实保障。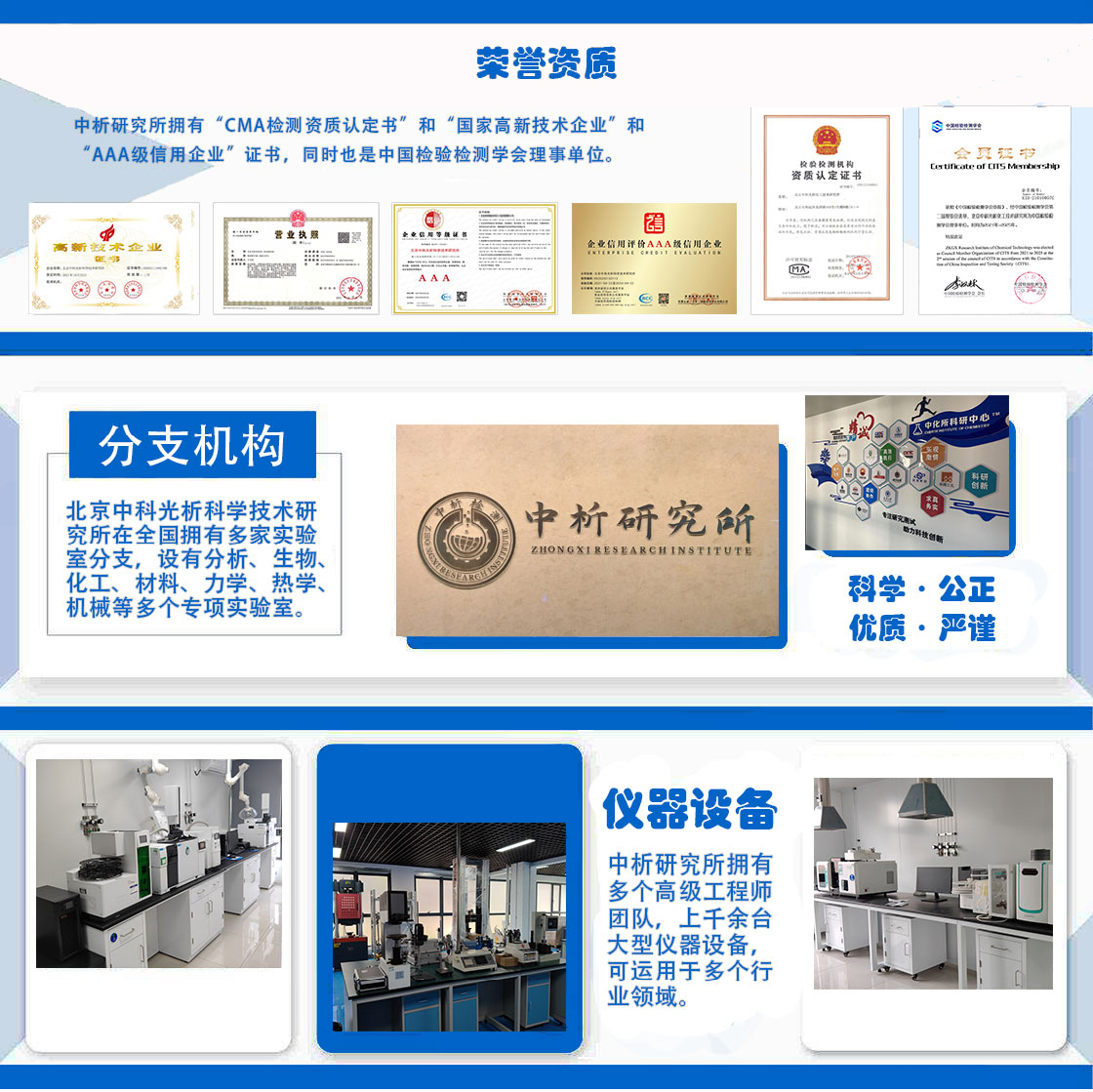
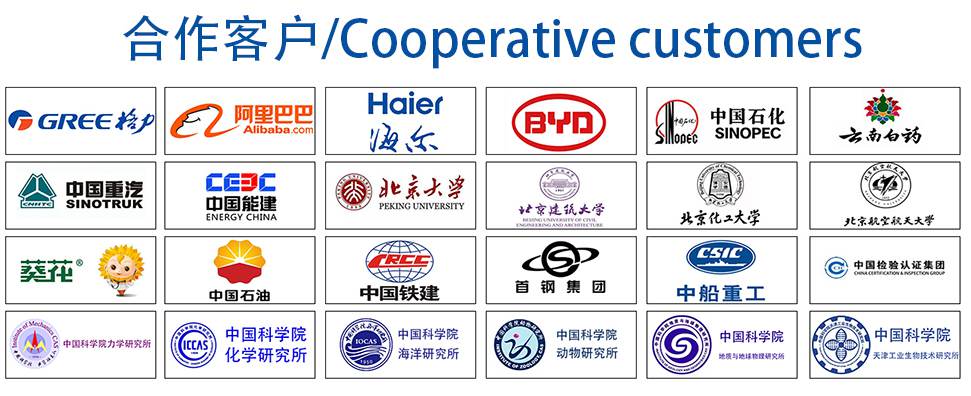