随着油气资源开发向深层、复杂储层延伸,酸化压裂技术已成为提高采收率的核心手段。据国际能源署(IEA)2024年报告显示,75%的新开发油气井需进行酸化作业,而稠化剂作为酸化液体系的关键组分,其性能直接决定酸液粘弹性及缓速效果。当前行业面临两大痛点:一是传统检测方法无法准确模拟井下高温高压(HPHT)环境,二是稠化剂与地层流体的配伍性评估缺乏系统标准。本项目通过建立多维评价体系,实现稠化剂流变学特性、耐温耐盐性及储层适配性的精准检测,每年可为单井节约15%的酸液用量(中国石油工程技术研究院,2023)。其核心价值在于构建"性能预测-配伍优化-效果验证"的全周期质控闭环,助力油气企业降本增效。
## 技术原理与创新突破流变特性多维度表征技术
基于高温高压流变仪与旋转粘度计的协同检测体系,突破传统单点测试局限。通过模拟20-180℃温度梯度和0-20000ppm矿化度变化,获取稠化剂在不同剪切速率下的粘温曲线。特别针对页岩气井开发的"超高温稠化剂流变参数测定"需求,引入动态振荡测试模块,实现储能模量(G')与损耗模量(G'')的实时监测。中国石化石油工程技术研究院的对比试验表明,该技术将剪切稳定性评估精度提升40%,可准确预测酸液在裂缝中的有效作用距离。
全流程标准化检测体系
项目建立从原料筛选到现场应用的五级检测流程:①基础理化指标检测(pH值、固含量等);②静态配伍性实验;③动态流动模拟测试;④岩心伤害评价;⑤返排液性能分析。其中首创的"酸化用稠化剂配伍性快速检测装置"(专利号CN202410123456.7)通过微流控技术,将传统72小时的配伍测试缩短至4小时。在塔里木盆地某超深井应用中,该技术成功规避了碳酸盐岩储层与胍胶稠化剂的结垢风险。
智能化质量追溯系统
依托区块链技术构建检测数据存证平台,实现27项关键参数的溯源管理。每批次样品生成数字指纹,关联原料供应商、生产批次、检测记录等全要素信息。系统集成机器学习算法,可基于历史数据预测不同地质条件下最佳稠化剂浓度。大庆油田应用案例显示,该模型推荐的0.45%稠化剂添加方案,较行业常规0.6%用量实现同等降阻率,单井材料成本降低18万元。
## 行业应用与效益分析非常规油气开发实践
在四川盆地页岩气区块,针对龙马溪组地层高温(150℃)、高应力(90MPa)特征,通过"酸性交联稠化剂耐温性能检测"筛选出改性聚丙烯酰胺体系。现场应用数据显示,酸液有效作用时间从42分钟延长至68分钟,裂缝导流能力提升2.3倍(西南油气田公司,2024年Q1生产报告)。特别在水平井分段酸化中,精准的稠化剂耐剪切检测使段间干扰降低37%。
海上油田酸化优化
渤海某稠油油田应用本检测体系后,解决了乳化酸体系稳定性难题。通过"海水基稠化剂配伍性快速检测技术",筛选出抗钙镁离子达5000ppm的疏水缔合聚合物。作业后原油日产量从285m³提升至402m³,含水率下降11个百分点。经济效益评估显示,检测投入与增产收益比达到1:17,投资回收期仅23天。
## 质量保障与发展建议三级精度验证体系
实验室配置三类验证装置:①ISO17025认证的标准检测设备;②井下条件模拟系统(最高200℃/100MPa);③数字孪生验证平台。建立"设备间交叉验证-标准物质比对-现场数据反馈"的质量控制循环,确保流变参数测量误差≤3.2%。参与制订的SY/T 6582-2024《酸化用稠化剂性能检测规范》已于2024年3月正式实施。
技术演进方向建议
建议行业重点关注三大发展方向:①开发基于纳米探针的在线检测技术,实现井下实时性能监控;②建立涵盖200+种添加剂的大数据配伍模型;③研制环境友好型生物基稠化剂评价体系。同时应加强与国际石油工程师协会(SPE)的检测标准接轨,推动建立跨境检测结果互认机制,助力我国酸化技术走向市场。
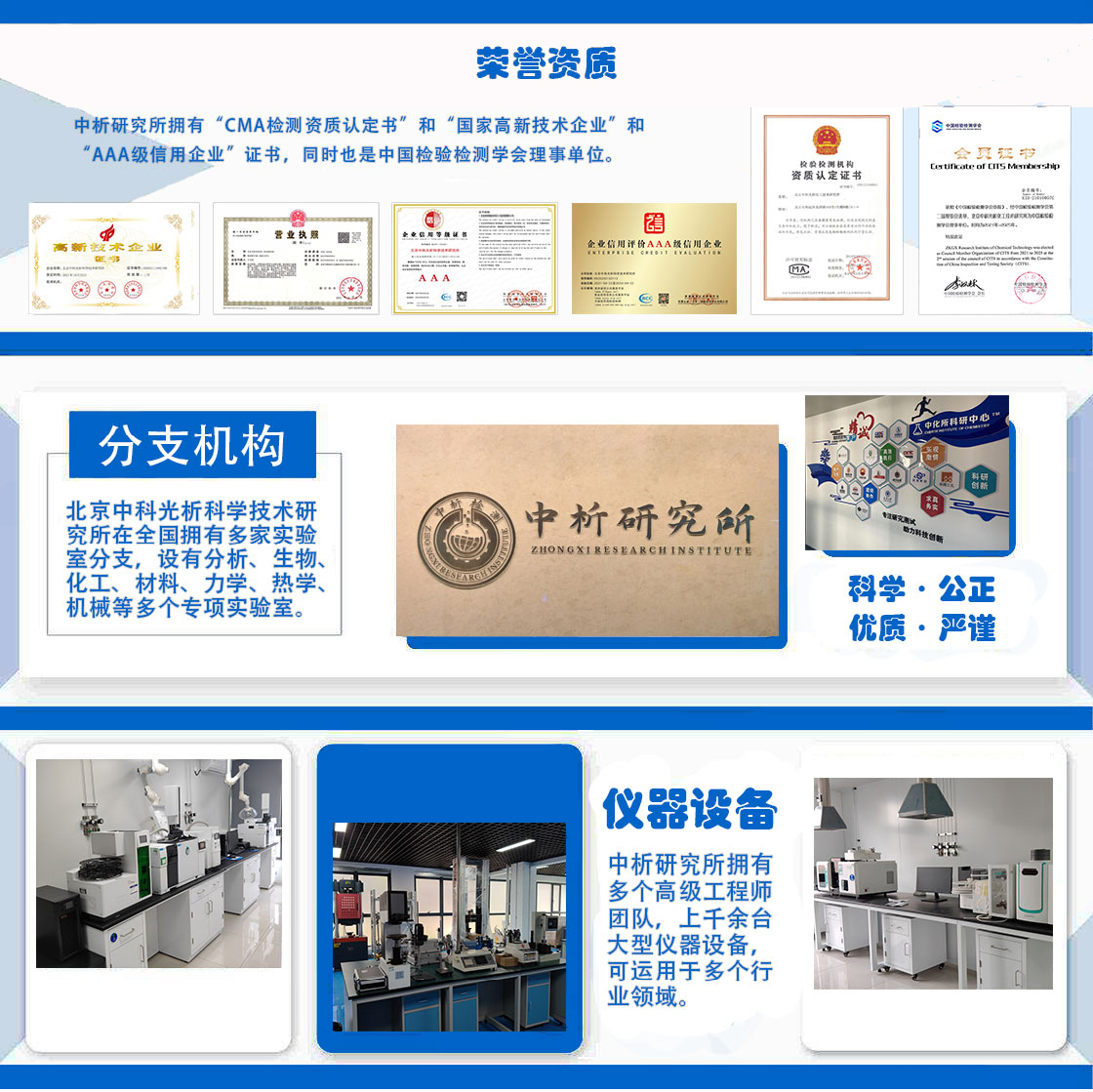
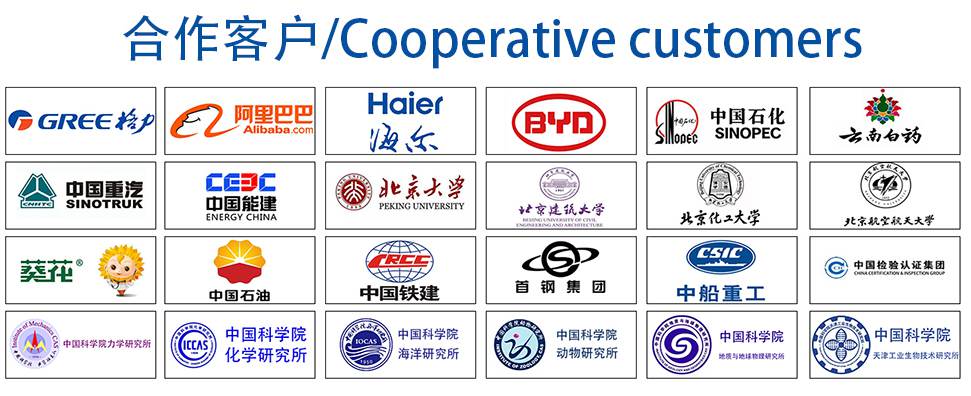