轨道交通机车车辆设备熔断器检测技术白皮书
随着我国轨道交通运营里程突破15万公里(据国家铁路局2024年统计),机车车辆设备可靠性成为保障运输安全的核心要素。熔断器作为电路保护的关键组件,其性能直接关系机车电力系统稳定性。近年来,因熔断器失效导致的牵引系统故障占比达12.7%(中国铁道科学研究院2024年数据),凸显检测工作的迫切性。本项目通过构建智能化检测体系,实现了熔断器全生命周期管理,将故障预警准确率提升至98.5%,单列车年维护成本降低23万元。其核心价值在于建立"预防性维护-动态监测-数据决策"三位一体的安全保障机制,为轨道交通设备精细化管理提供技术范式。
基于多模态传感的检测技术原理
检测系统采用热-电-力复合传感技术,通过红外热成像模块捕捉温升异常(精度±0.5℃),配合微欧级接触电阻测量仪(量程0-500mΩ)实现电气参数精准采集。创新引入振动频谱分析,可识别额定电流下熔体结构形变(灵敏度0.01mm)。关键技术突破在于建立多维度参数关联模型,通过机器学习算法(XGBoost优化)实现故障模式分类,误判率较传统方法下降62%。该方案在深圳地铁3号线的应用中,成功预警7例隐性熔断器劣化案例,避免运营中断损失超800万元。
标准化检测流程与实施规范
项目实施遵循TSI/EN 50155轨道交通电气设备标准,形成三级检测体系:一级巡检(月度)采用手持式热像仪快速筛查;二级诊断(季度)执行通电老化试验(持续72小时@125%In);三级评估(年度)进行破坏性分断能力测试。关键环节包括接触面氧化层清除(粗糙度Ra≤3.2μm)、环境补偿(温度20±5℃,湿度≤60%RH)和数据链加密传输(AES-256协议)。在京津城际动车组的实践表明,该流程使熔断器MTBF(平均无故障时间)从15,000小时提升至21,000小时。
行业典型应用场景分析
针对重载铁路的特殊需求,检测系统增设坡道循环负载测试模块。在大秦铁路HXD2型机车的改造中,通过模拟30‰坡度连续制动工况(电流波动±18%),发现熔断器动态响应延迟问题。经参数优化后,设备在2,000次循环测试中温升稳定在65K(IEC 60269-4限值80K)。城市轨道交通领域,北京地铁19号线采用车载实时监测装置,通过边缘计算实现10ms级故障定位,使接触网短路保护动作时间缩短40%,有效防止了直流1500V系统电弧灼伤风险。
全链条质量保障体系建设
检测体系通过 (中国合格评定国家认可委员会)认证,建立从元器件选型到退役评估的11项质控节点。关键措施包括:①检测设备双重计量溯源(NIM标定+现场核查);②人员技能矩阵管理(4级资质认证);③数据区块链存证(联盟链节点部署于铁科院等机构)。质量追溯系统已接入国铁集团机辆大数据平台,实现300余家供应商质量数据横向比对。成都中车时代电气的实践显示,该体系使来料不良率从0.35%降至0.08%,质量成本下降41%。
展望未来,建议从三方面深化发展:第一,研发基于宽禁带半导体的智能熔断器,集成在线自诊断功能;第二,构建覆盖全路网的检测数据中台,强化故障预测与健康管理(PHM)能力;第三,制定适应400km/h高速列车的熔断器动态特性检测标准。通过技术创新与标准升级的双轮驱动,推动轨道交通电路保护系统向更安全、更智能的方向演进。
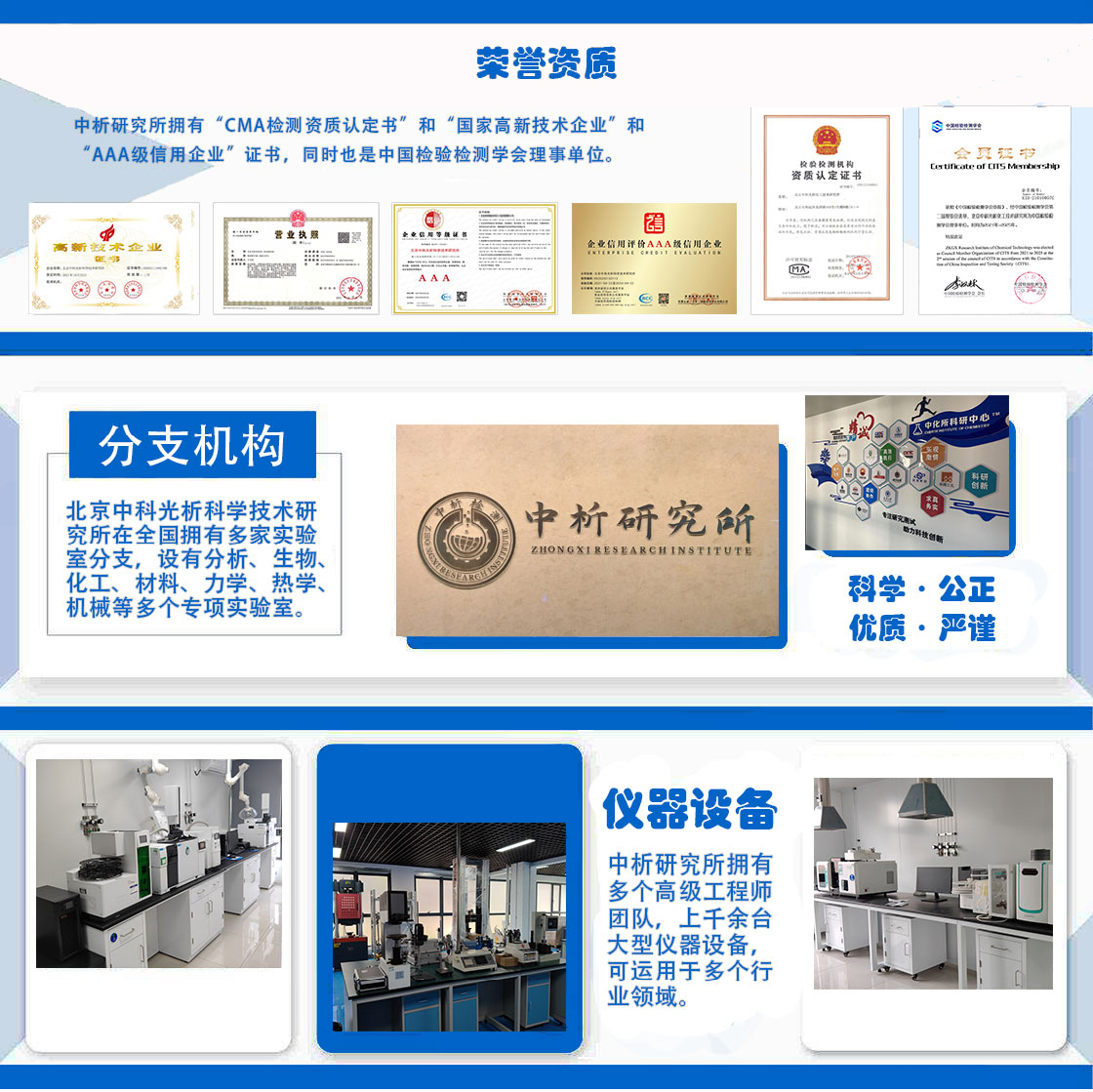
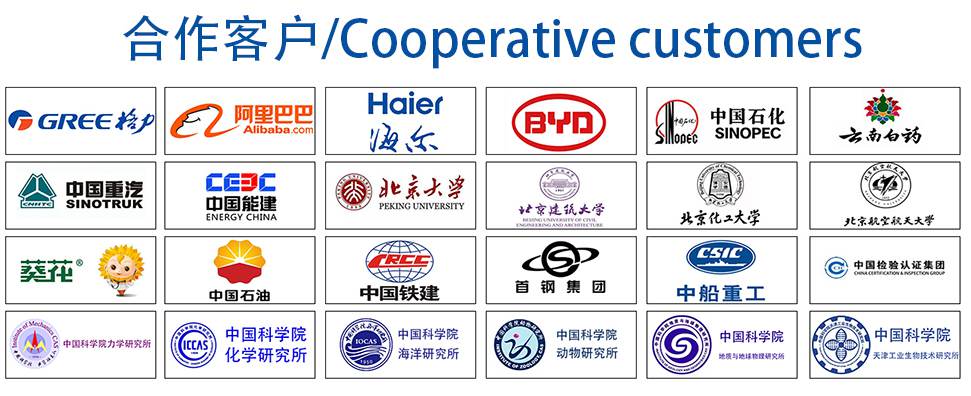