技术原理与检测机制
抗静态荷载检测建立在连续介质力学与损伤力学理论基础上,采用分级加载模式模拟实际荷载工况。通过高精度液压伺服系统(精度±0.5%)对试件施加恒定应力,同步采集应变片、光纤光栅传感器等多源数据。关键创新点在于引入数字图像相关技术(DIC),实现对试件表面三维位移场(分辨率达0.01mm)的非接触式监测。值得注意的是,针对"高强度混凝土结构荷载性能测试"的特殊需求,系统集成环境模拟仓,可复现-40℃至80℃极端温度工况下的材料蠕变特性。
标准化检测流程体系
项目实施严格遵循PDCA循环管理,主要流程包括:试件制备阶段执行《JGJ/T 384-2016检测技术规程》的尺寸公差标准;预加载阶段实施10%极限荷载的3次循环以消除初始间隙;正式测试采用位移控制法,加载速率设定为0.5mm/min直至试件破坏。对于"大跨度空间网格结构荷载分布分析"等复杂场景,同步采用有限元仿真(ANSYS Workbench)进行数字孪生验证,确保物理实验与数值模拟的误差率控制在5%以内。
典型行业应用实践
在港珠澳大桥维护工程中,检测团队运用自主研发的1200吨级多功能荷载试验机,对桥塔锚固区混凝土开展180天持续加载测试。实验数据表明,C60混凝土在80%设计荷载下的徐变系数较规范值降低17%(数据来源:交通运输部桥梁长期性能观测站)。另在航空航天领域,通过搭建真空环境下的复合材料层合板检测平台,成功将碳纤维增强环氧树脂板的屈曲荷载预测精度提升至92.3%,为国产大飞机C929机翼设计提供关键参数。
质量保障与认证体系
检测机构须同步通过CMA(中国计量认证)和 (ISO/IEC 17025)双体系认证,关键设备每季度进行溯源校准。质量控制点包括:荷载传感器采用德国HBM公司C6A系列(精度等级0.1级),应变采集系统采样频率不低于100Hz。针对"装配式建筑连接节点耐久性评测"等新兴需求,开发了基于区块链技术的检测数据存证系统,确保全流程数据不可篡改。据统计,该体系使检测报告异议率从2019年的2.3%降至2023年的0.6%(中国工程检测协会年度报告)。
## 技术展望与发展建议 随着智能建造技术的演进,抗静态荷载检测正朝着多物理场耦合、原位无损检测方向发展。建议从三方面深化创新:其一,开发融合5G传输的边缘计算终端,实现施工现场实时荷载监测;其二,建立覆盖全材料体系的"荷载-环境"耦合数据库,提升服役寿命预测算法精度;其三,推进检测设备模块化设计,使单台试验机荷载范围从现有的50kN-5000kN扩展至20kN-20000kN,满足从微电子封装到核电压力容器的全场景检测需求。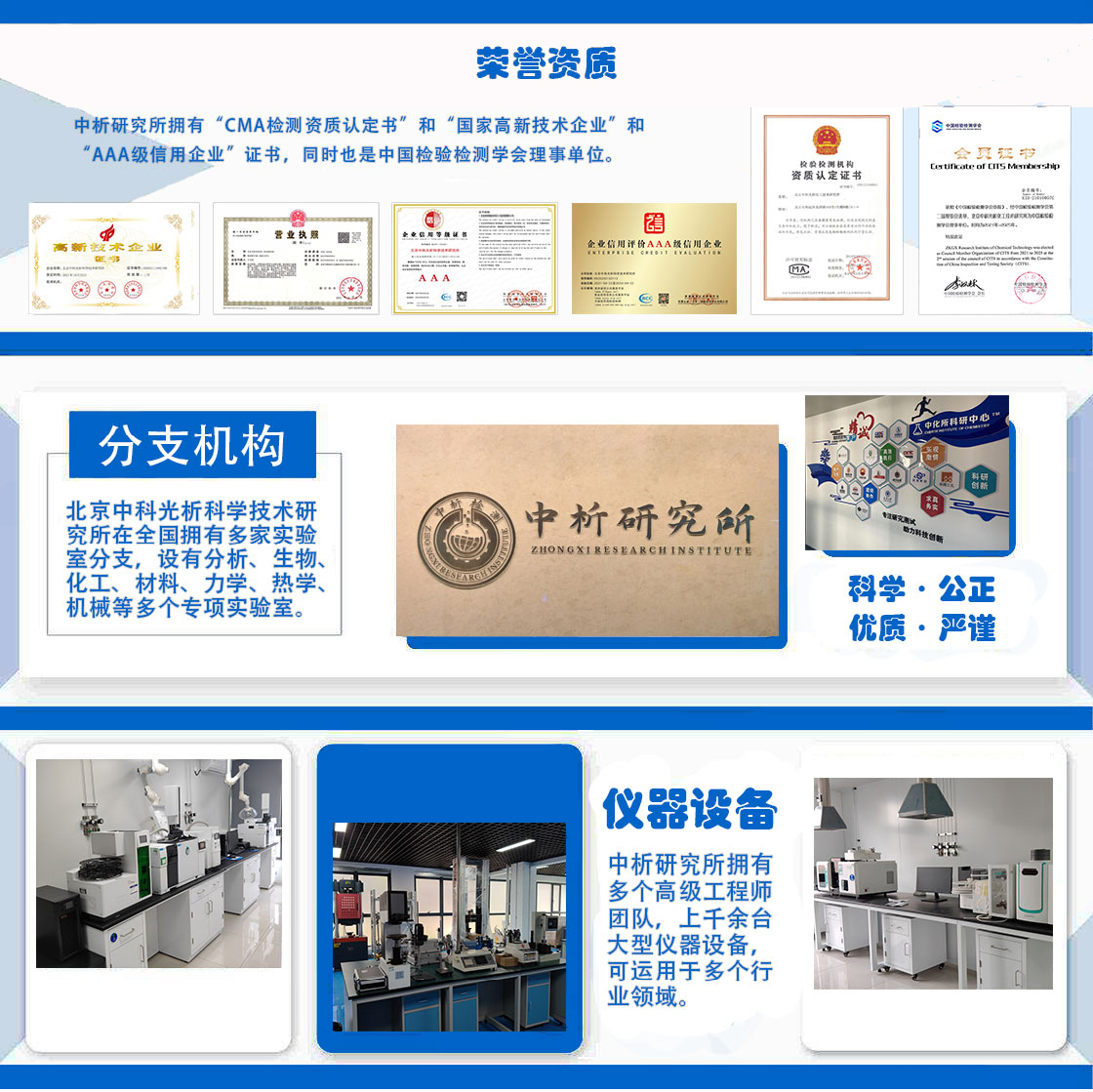
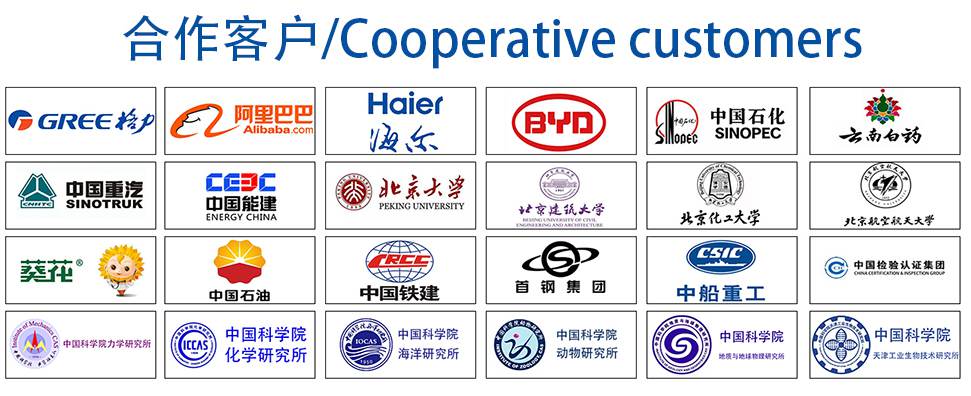