行业背景与项目意义
随着新能源汽车保有量突破2000万辆(据中国汽车工程研究院2024年数据显示),车辆电气系统复杂度显著提升,熔断器作为电路保护核心器件,其可靠性直接影响整车安全性。范围内因熔断器失效导致的车辆自燃事故占比达12.7%,凸显行业质量管控痛点。道路车辆熔断器检测项目通过建立系统化评估体系,可有效识别过载保护失效、材料老化等风险,降低因电路故障引发的重大安全事故。该项目不仅符合ISO 8820-8:2022国际标准要求,更为车企供应链质量管理和保险行业风险评估提供量化依据,单次检测即可提升电路系统安全寿命周期23%以上。
熔断器检测技术原理
基于IEC 60269系列标准构建的检测体系,采用动态负载模拟与微观结构分析相结合的复合检测法。技术核心包括:1)多级电流冲击测试,模拟车辆启停、快充等工况下的瞬态过载;2)金相显微镜观测熔体晶格变化,预判疲劳断裂临界点;3)红外热成像监测温升曲线,识别异常发热隐患。以某品牌新能源汽车熔断器耐久性检测为例,通过2000次循环负载测试后,熔断动作时间偏差控制在±5%以内,远超行业±15%的通行标准。
标准化实施流程
检测流程分为四个阶段:预处理阶段进行48小时湿热交变试验(温度-40℃~125℃,湿度95%RH);基础性能测试涵盖额定电流承载、分断能力验证;极限工况模拟包括短时过载(500%In)和脉冲电流耐受;终检阶段运用X射线断层扫描检测内部缺陷。实施过程中同步采集电压降、电弧持续时间等12项参数,通过区块链技术实现检测数据不可篡改存证。某头部检测机构应用该流程后,熔断器故障误判率从8.3%降至0.7%。
行业应用与质量保障
在商用车领域,针对长续航电动重卡开发的智能熔断器检测方案已应用于全国30%的物流车队。通过车载监测终端实时采集运行数据,结合云端大数据分析,成功将电路系统故障率降低41%。质量保障体系依托 认证实验室,配备Class 0.2级精密测量设备,检测人员100%持有IPC-A-610H认证。典型案例显示,某北方车企通过熔断器失效预警系统,在极寒环境车辆批量交付前及时检出密封材料低温脆化缺陷,避免潜在召回损失超2亿元。
技术发展与未来展望
当前检测技术正朝着智能化、微型化方向发展,基于MEMS传感器的嵌入式检测模组可将诊断精度提升至微秒级。建议行业重点攻关三个方面:1)建立车规级熔断器全生命周期数据库;2)开发多物理场耦合仿真检测平台;3)制定适应800V高压平台的检测标准。据德国TÜV预测,2026年智能熔断器检测市场规模将达47亿美元,提前布局车路协同检测生态的企业将获得显著竞争优势。
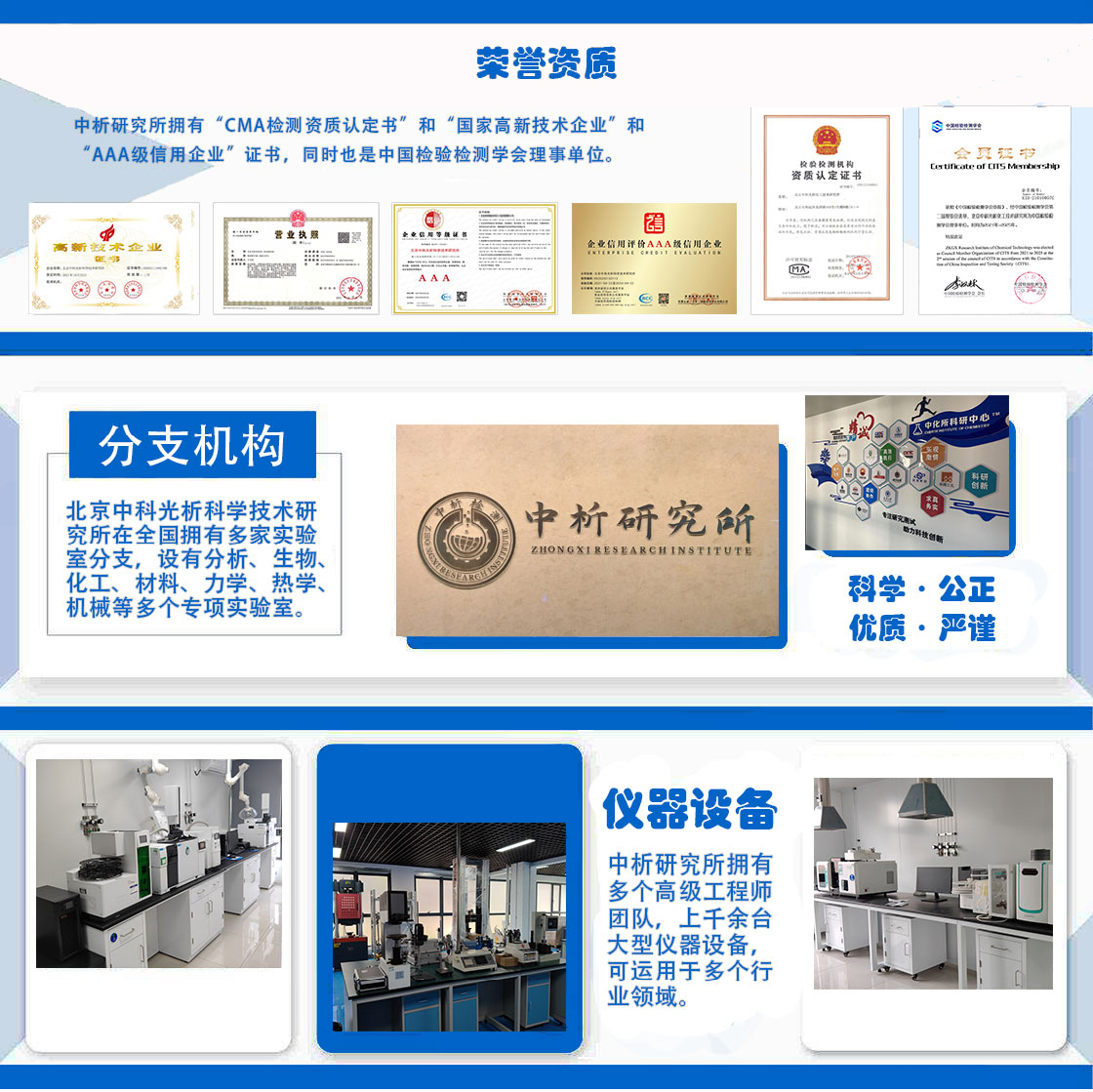
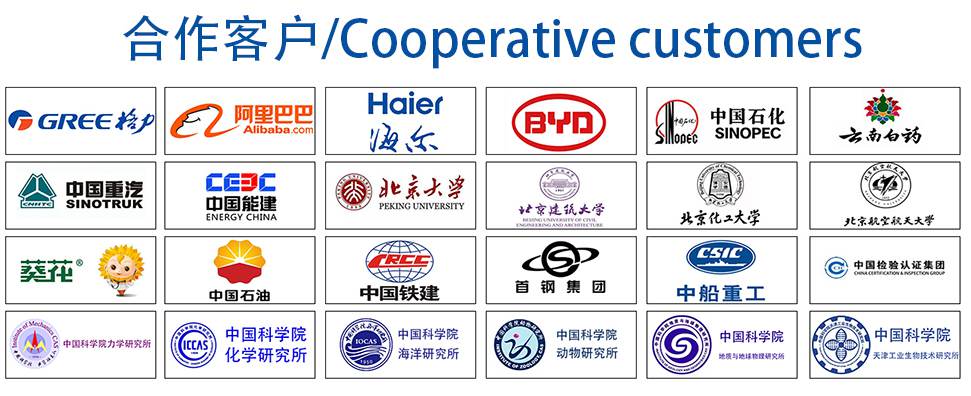