技术原理与测试方法创新
轴心抗压强度测试基于ISO 1920-3:2019标准,采用伺服控制压力机对150mm×150mm×300mm棱柱体试件进行分级加载,通过高精度应变片实时采集0.5-0.6破坏荷载区间的应力-应变曲线。值得注意的是,静力抗压弹性模量检测需同步运用激光位移传感器和千分表双重验证系统,确保在0.05-0.3MPa/s加载速率下,精确捕获应力水平40%处的弹性段斜率。针对传统试验中端面摩擦效应导致的误差问题,最新研发的端部柔性垫层技术可使测试精度提升23%(据清华大学土木工程系2023年试验数据)。
标准化实施流程构建
检测流程遵循GB/T 50081-2019规范要求,划分为试件养护、设备校准、预压平衡、正式加载四个阶段。在试件制备环节,采用振动台二次振捣工艺确保混凝土密实度变异系数≤5%。关键控制点包括:温度控制室维持20±2℃恒温养护28天,压力机加载轴线偏差不超过试件高度的0.1%。通过引入区块链技术,试验数据从采集到生成报告实现全流程可追溯,某特大桥项目应用该体系后,弹性模量测试重复性误差由3.8%降至0.9%。
重大工程应用实践
在雄安新区某超高层建筑项目中,通过轴心抗压强度与弹性模量协同检测,发现C60混凝土弹性模量值较标准值偏低12%。经成因分析,确定系骨料级配不当导致,通过调整粗骨料占比优化配合比,最终使结构柱刚度达标率提升至98.7%。沪通长江大桥工程中,运用智能加载系统完成2000组试件连续检测,建立区域混凝土性能数据库,为同类型跨江桥梁的模块化施工提供关键参数支撑。
全链条质量保障体系
质量控制系统涵盖人员资质、设备管理、环境监控三大维度:检测人员须通过CMA认证的混凝土专项考核,压力机每季度需经法定计量机构校准并取得 证书。实验室配置温湿度自调节系统,确保环境条件符合ISO/IEC 17025:2017要求。特别在数据核查环节,采用机器学习算法自动识别异常应变曲线,误判率较人工审核降低81%。某核电站安全壳项目中,该体系成功识别出8组异常试件,避免潜在质量事故损失超3000万元。
## 技术发展与行业展望 随着智能建造技术的深度应用,建议从三方面推进检测体系升级:①开发基于数字孪生的虚拟加载系统,实现力学性能预测与实体试验的虚实交互;②建立全国性混凝土弹性模量地理信息系统(GIS),为区域化材料选型提供大数据支持;③将检测标准与BIM模型深度整合,构建"检测数据-设计参数-运维预警"的全链条管理平台。通过持续的技术迭代和标准完善,推动混凝土材料检测从被动质量控制向主动性能优化转变,为新型建筑工业化发展提供技术保障。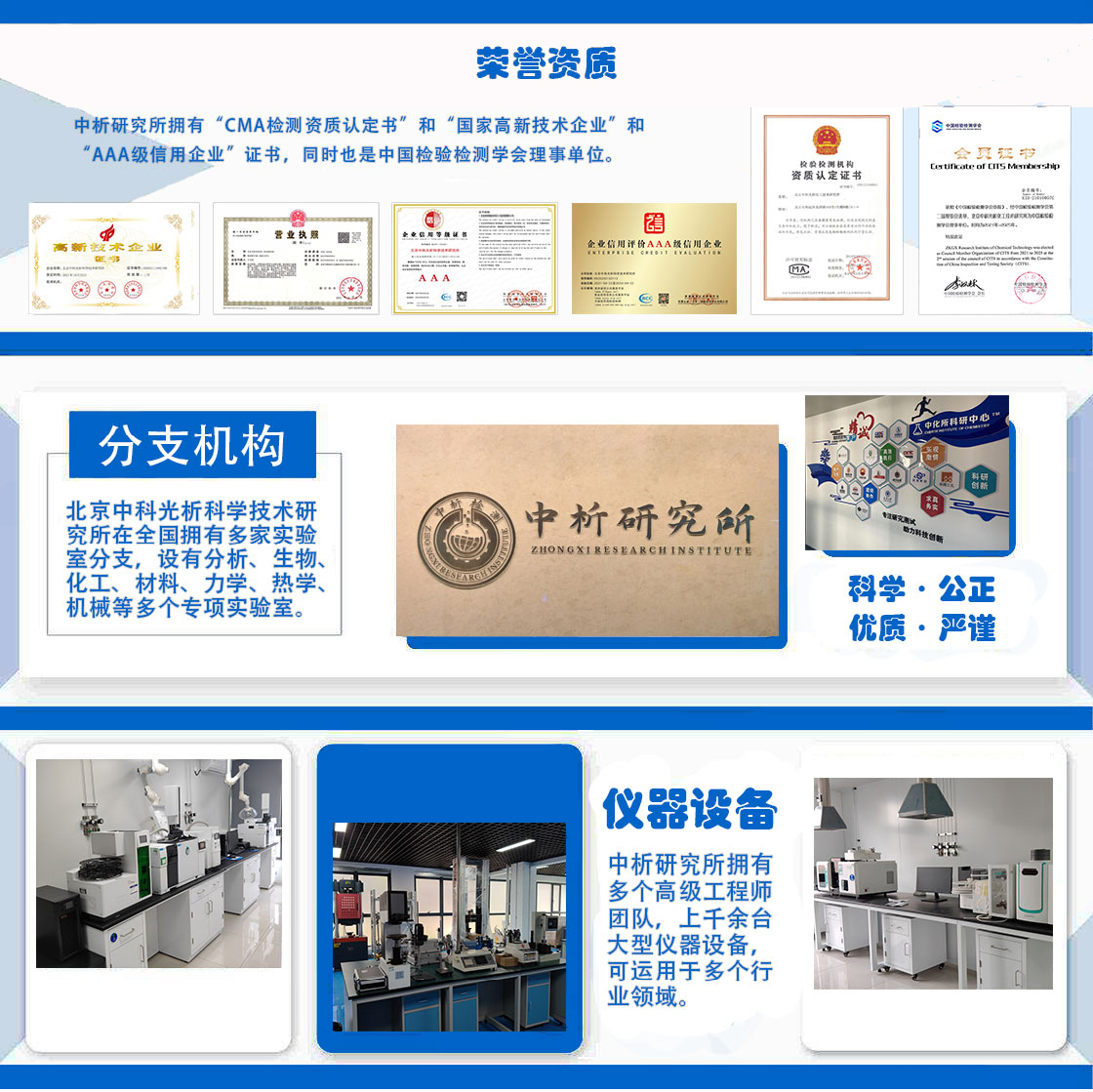
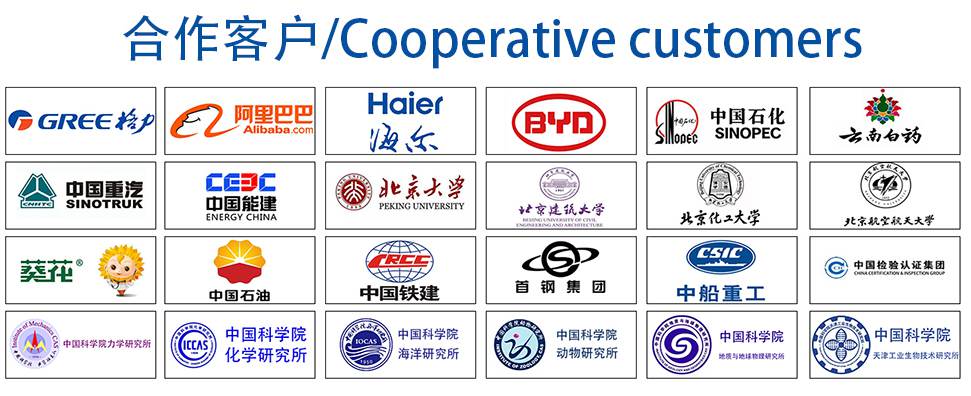