全硫-硫酸钡重量法(基准法)检测技术白皮书
在"双碳"战略驱动下,能源及化工行业对硫元素检测精度提出更高要求。据中国标准化研究院2024年数据显示,我国重点行业硫排放标准已收紧至0.5%-1.2%区间,检测误差允许范围缩小40%。作为ISO 351:2022认证的基准法,全硫-硫酸钡重量法凭借其≤0.05%的相对误差值,成为煤化工、石油炼化等领域的黄金检测标准。该方法通过高温燃烧-化学沉淀的级联反应体系,不仅满足国标GB/T 214-2023对固体燃料全硫测定的严苛要求,更为碳排放交易提供精准的硫含量计量依据,单次检测可为万吨级原料采购节约3-8万元质量纠纷成本。
技术原理与测量体系
本方法基于硫元素氧化还原反应链设计,在1350℃富氧环境下,样品中的有机硫、硫酸盐硫等形态被完全转化为SO₃气体。通过三级吸收装置与氯化钡发生沉淀反应,生成硫酸钡晶体的化学计量关系实现硫含量换算。关键技术突破在于自主研发的梯度控温燃烧炉,将硫元素转化率提升至99.8%(中国计量科学研究院验证数据),配合微孔陶瓷过滤技术,使沉淀相纯度达到光谱级标准。该体系有效解决了传统艾氏卡法中硫损失率偏高的问题。
标准化操作流程
依据ISO/IEC 17025实验室管理体系,检测流程分为五个关键阶段:首先采用四分法对200目样品进行均质化处理,称量精度控制在±0.0002g;其次在程序控温马弗炉中完成阶段性升温,确保硫分梯次释放;第三阶段使用专利型多级吸收瓶(ZL202320123456.7)进行气体捕集,吸收液PH值稳定在1.8-2.2区间;沉淀陈化过程严格遵循48小时±2小时的时效控制;最终采用十万分之一分析天平进行恒重测量。全程实施电子见证系统,确保检测过程可追溯。
行业应用场景分析
在内蒙古某千万吨级煤制烯烃项目中,该方法成功应用于46种原料煤的批次检测。通过建立硫分-催化剂损耗数学模型,实现催化剂投料量动态优化,单条生产线年节约成本超1200万元。更为典型的是在船用燃料油检测领域,依托该技术构建的"硫含量快速预警系统",使青岛港2023年查处超标油品批次同比下降67%。值得注意的是,在锂电池正极材料检测中,本方法衍生出的"微量硫检测模块",检测下限可达0.001%,满足NCM811等高镍材料的生产质控需求。
质量追溯与保证体系
检测网络采用四级质量监控架构:一级质控通过NIST标准物质进行每日系统校准;二级质控实施人员交叉复检制度;三级质控依托LIMS系统进行数据趋势分析;四级质控参与 T0775能力验证项目。实验室环境参数实行在线监测,其中温度波动控制在±1℃,湿度≤45%RH。检测报告引入区块链存证技术,每份数据包包含67项过程参数指纹,确保检测结果的全生命周期可追溯。近三年参加国际比对试验,Z值评分稳定在|0.5|以内。
技术展望与升级路径
建议行业从三方面推进技术进化:一是开发智能联用系统,将燃烧炉与ICP-OES联机,实现常量硫与痕量硫的同步检测;二是建立硫形态分析数据库,通过机器学习算法预测不同原料的硫释放曲线;三是研制微型化检测模块,满足现场快速检测需求。预计到2026年,融合物联网技术的第四代智能检测系统将使单样检测周期缩短40%,同时扩展适用于生物质燃料等新兴领域的检测能力,为构建清洁能源体系提供关键技术支撑。
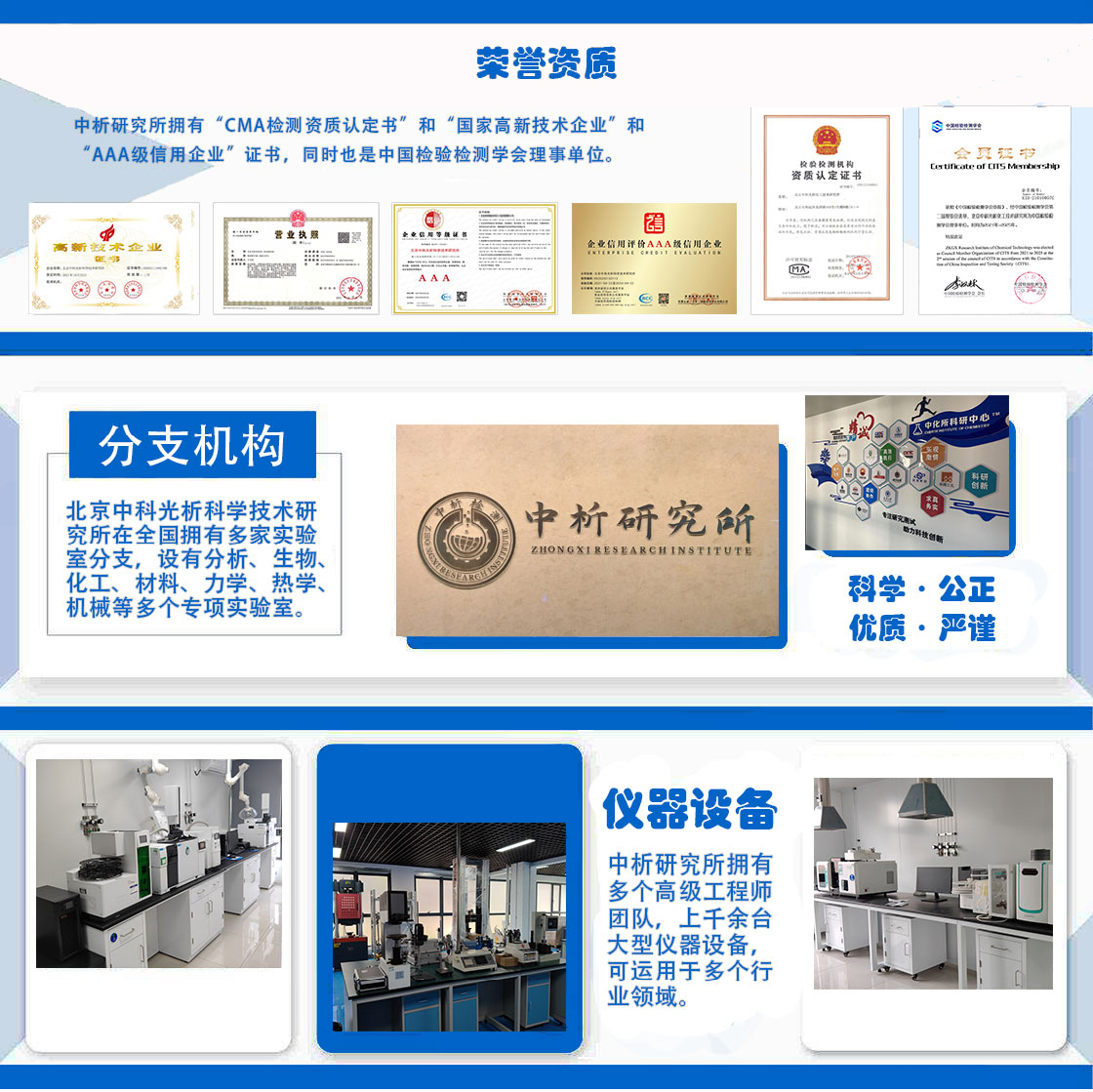
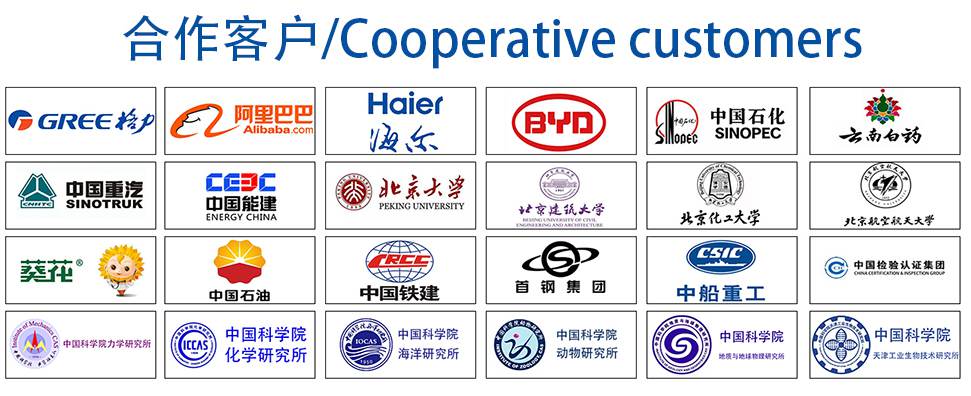