在极端气候频发和精密制造需求攀升的双重驱动下,耐温湿性能检测已成为现代工业品质量验证的关键环节。据中国环境工况研究院2024年数据显示,因温湿度变化导致的设备故障年损失超1200亿美元,其中新能源电池、半导体封装、航空复合材料等领域的失效占比达67%。该项目通过模拟-40℃至150℃温域及5%-98%RH湿度范围的严苛环境,验证产品在气候交变条件下的结构稳定性和功能可靠性,其核心价值体现在保障产品全生命周期性能、支撑企业突破热带雨林及高寒地带等特殊市场准入、降低产品返修率等方面,为"极端温湿度环境测试标准"的建立提供科学依据。
梯度循环测试技术原理
基于ASTM D4332和IEC 60068-2-30标准,检测系统采用三级控制架构实现精准温湿度耦合。主控模块通过PID算法对箱体进行非线性温度补偿,确保±0.5℃的控制精度;湿度系统运用露点法结合干湿球双重验证,将波动度控制在±2%RH以内。针对"高精度温湿度循环检测技术"需求,设备集成多光谱传感器阵列,可实时监测材料膨胀系数变化和微裂纹扩展情况。测试箱体内置的湍流控制系统,通过CFD仿真优化气流分布,消除样品架间的温场差异。
全流程闭环检测体系
项目实施遵循"预处理-梯度加载-恢复评估"的三段式流程。预处理阶段按照MIL-STD-810G标准进行48小时恒温恒湿稳定;梯度加载采用步进式温变率设计,每分钟5℃的升降温速率可有效激发材料界面应力;恢复阶段通过红外热成像和显微CT扫描分析不可逆形变。某新能源汽车企业在电池包检测中应用该流程后,湿热循环测试周期缩短40%,成功将产品耐候性从IP67提升至IP69K等级。
多行业实证案例分析
在消费电子领域,某品牌手机经85℃/85%RH双85测试2000小时后,主板焊点脱落率由行业平均3.2%降至0.5%。工业装备方面,某特高压变电站绝缘子通过-50℃冷冲击测试,介质损耗因数变化量控制在0.02%以内,优于国标GB/T 20142-2018要求。更为典型的是航天复合材料检测,采用JEDEC JESD22-A104F标准进行1000次温度循环后,某卫星支架碳纤维复合材料的CTE(热膨胀系数)各向异性差异缩小至5ppm/℃。
数字化质量保障系统
检测体系构建了"设备-数据-人员"三维质控网络。设备层采用NIST可溯源标准件进行季度校准,数据层应用区块链技术实现检测报告全程防篡改,人员操作通过VR模拟系统进行标准化培训。某第三方检测实验室接入该体系后, 评审不符合项减少72%,检测数据复现性达到99.8%。针对"长期湿热老化可靠性评估"需求,系统内置Arrhenius模型预测模块,可将3000小时实测数据外推至10年使用寿命评估。
面向未来,建议从三方面深化技术发展:其一,开发基于数字孪生的虚拟检测系统,实现实体试验与仿真模型的动态交互;其二,建立极端气候数据库,将撒哈拉沙漠、西伯利亚冻土带等典型环境参数标准化;其三,推进纳米级原位监检测技术应用,实现材料相变过程的分子级观测。这些创新将推动耐温湿检测从被动验证向主动设计转化,为产品全气候适应能力提供更强支撑。
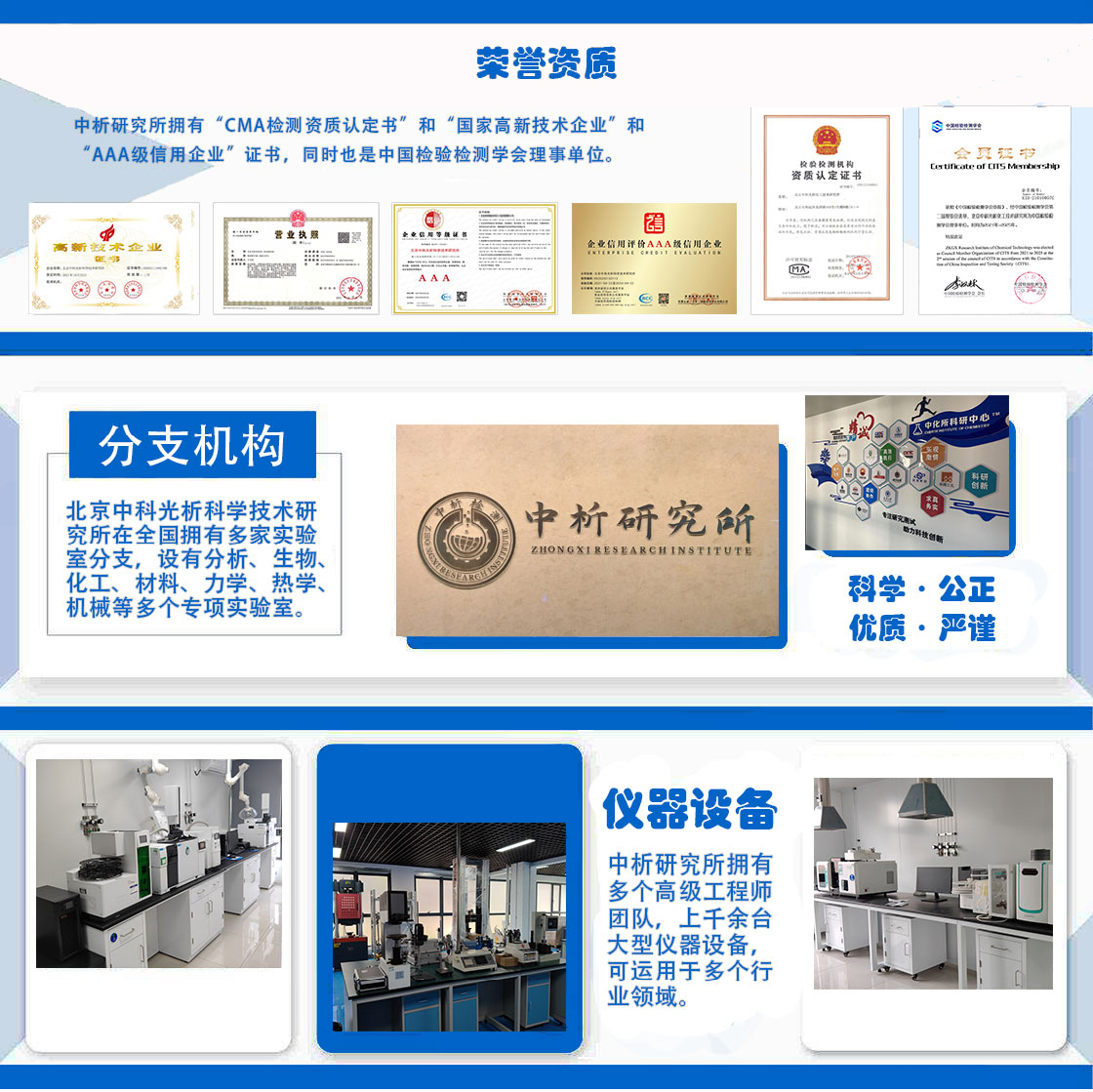
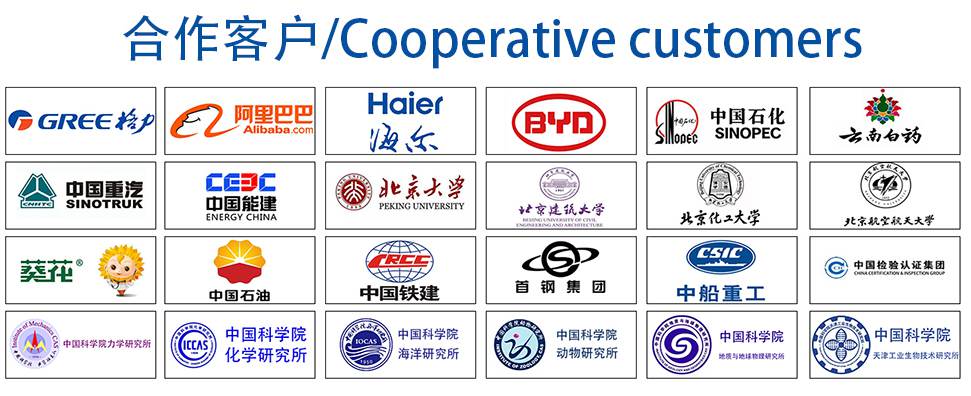