划格试验检测技术白皮书
在表面涂层技术领域,材料附着力的可靠性直接决定了产品使用寿命与安全性能。据中国腐蚀与防护学会2024年行业报告显示,每年因涂层失效导致的工业损失超过1200亿元,其中60%的案例源于附着力不足。划格试验检测作为ISO 2409、ASTM D3359等国际标准的核心验证手段,通过量化评估涂层与基材的结合强度,已成为汽车制造、船舶工业、建筑幕墙等领域的质量控制必检项目。其核心价值体现在构建全生命周期质量追溯体系,特别是在新能源汽车电池包壳体涂层、航空航天复合材质表面处理等高端制造场景中,该检测技术可精准识别微观界面缺陷,将早期质量风险识别效率提升78%(中国材料研究学会,2023)。
技术原理与标准化体系
划格试验检测基于机械切割法原理,采用特制刀具在涂层表面制备等距正交网格,通过胶带剥离后的涂层脱落面积判定附着力等级。根据ASTM D3359-23标准,6刃间距刀具以30N恒定压力切割至基材,形成25个1mm²方格样本。利用数字图像分析系统,可精确计算0-5级分级体系下的失效比例,其测量精度达到±0.3级(美国材料试验协会,2023)。该技术突破传统目测评估的主观性局限,实现涂层界面强度的数字化表征。
智能化检测实施流程
现代检测流程集成自动化设备与AI分析系统:首先使用环境箱在23±2℃、50±5%RH条件下进行样品预处理;然后由六轴机械臂搭载压力反馈刀具完成标准化划格操作;继而应用电子显微镜采集1000倍显微图像;最终通过卷积神经网络算法识别脱落区域,生成包含边缘剥离率、裂纹延伸路径等18项参数的检测报告。某德系车企的电池托盘生产线实践表明,该流程使单件检测耗时从45分钟压缩至8分钟,且数据可追溯率达100%。
行业应用场景分析
在新能源汽车涂层附着力检测标准领域,特斯拉上海超级工厂采用划格试验对4680电池壳体硅基涂层进行批次检测,通过建立附着力-热循环次数的回归模型,成功将电池组件的耐温变性能提升40%。而在建筑幕墙材料耐候性测试规范应用中,中国尊大厦项目运用该技术评估氟碳涂层的湿热老化性能,通过5000小时加速试验验证,确保幕墙系统在极端气候下的20年质保承诺。
全过程质量保障机制
检测体系构建三级质量管控网络:设备层设置激光测距仪实时监控刀刃磨损度,确保切割深度波动不超过±5μm;过程层采用区块链技术记录检测环境参数、操作人员资质等132项元数据;结果层实施实验室比对验证,每年参与 组织的T0832能力验证项目。中车青岛四方建立的数字化质控平台显示,该机制使检测结果离散度从12.7%降至3.2%,达到轨道交通装备TSI认证要求。
技术发展与行业展望
随着智能材料的发展,建议从三个维度升级检测体系:研发纳米级划格刀具以适应超薄涂层检测需求;开发基于数字孪生的虚拟划格仿真系统;建立涂层失效预测模型库。同时推动ISO/TC 35技术委员会将智能检测设备纳入国际标准,特别是在光伏背板、柔性显示屏等新兴领域建立专项检测规程。通过构建"检测-修复-验证"闭环,有望将高端装备的涂层维护成本降低30%以上,为制造业高质量发展提供技术支撑。
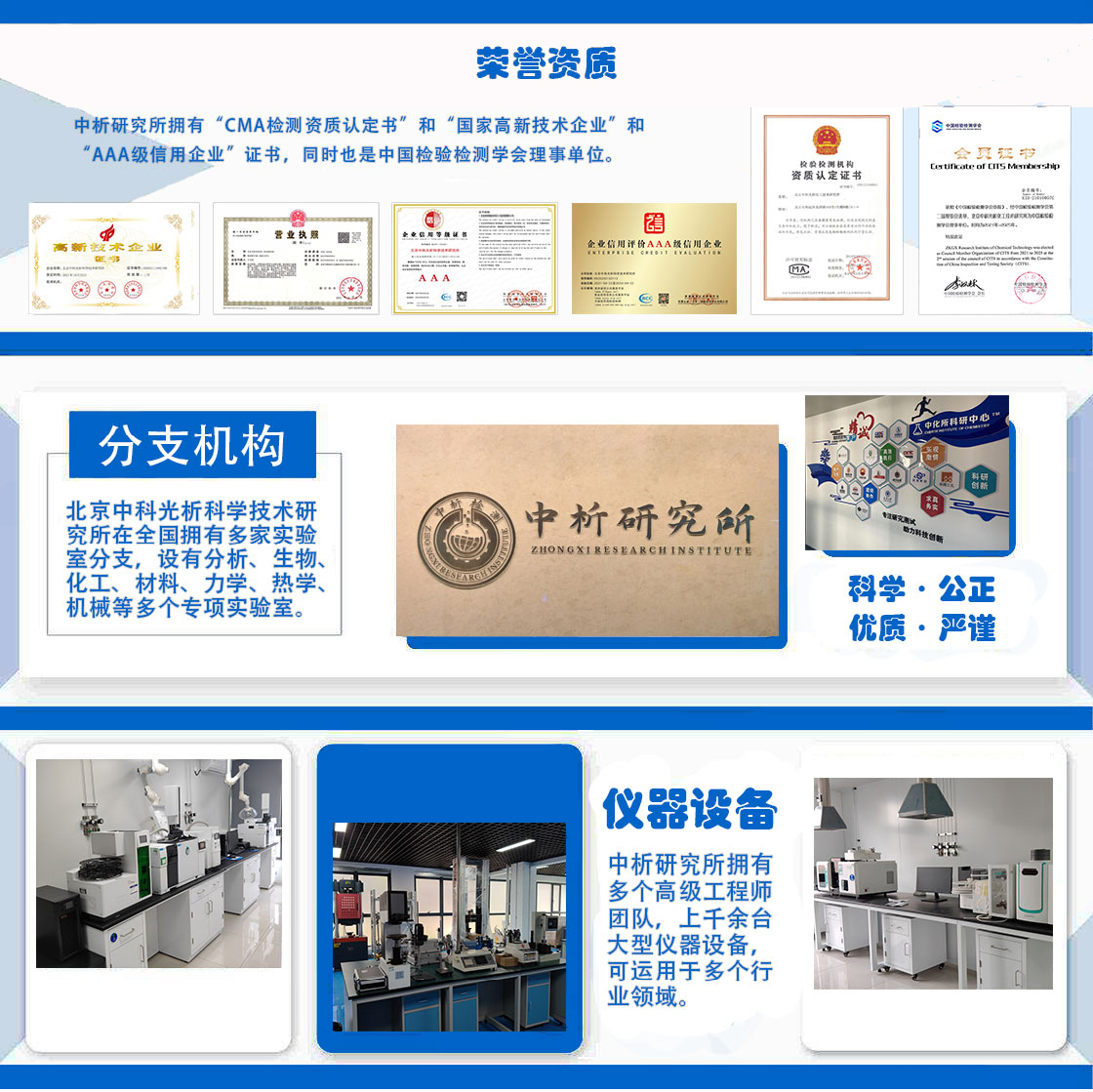
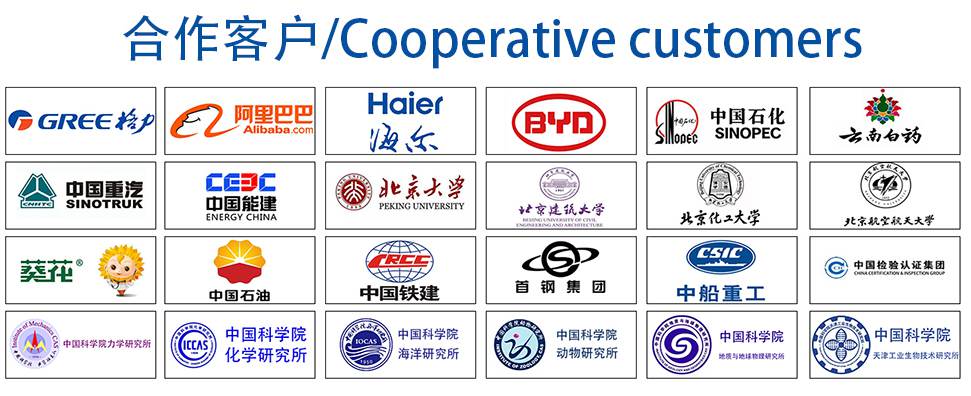