高温后抗拉强度检测:保障材料性能的关键技术
随着高端制造业和能源行业的快速发展,材料在高温环境下的可靠性成为制约装备安全运行的核心因素。据国家材料测试中心2024年数据显示,超过35%的工业设备失效事故与材料高温性能衰减直接相关。高温后抗拉强度检测作为材料性能评估的关键环节,通过量化材料经历高温暴露后的力学特性,为航空航天、核电装备、石油化工等领域的选材优化和寿命预测提供科学依据。该技术不仅能够验证新型耐高温材料的研发效果,还可指导高温服役部件的维护决策,其核心价值体现在降低事故风险、延长设备使用寿命和推动材料技术创新三个维度。
基于热力耦合效应的检测原理
高温后抗拉强度检测基于材料热力学与机械性能的耦合作用机制,通过模拟实际工况下的温度-应力作用路径,测量材料在经历高温环境后的极限承载能力。标准测试流程依据ASTM E21和ISO 6892系列规范,采用分级升温程序控制试样受热均匀性,配合电子万能试验机实现精准载荷施加。值得注意的是,检测过程中需重点关注晶界氧化、相变软化等高温特有现象对测试结果的影响。以镍基高温合金为例,其检测温度通常需覆盖800-1100℃区间以模拟航空发动机真实工况。
标准化检测实施流程
完整的检测体系包含五个关键阶段:试样预处理(表面粗糙度Ra≤1.6μm)、高温暴露(控温精度±2℃)、冷却处理(空冷/水冷模式选择)、拉伸测试(0.005-5mm/min速率分级)以及数据校核(温度补偿修正)。在核电主蒸汽管道检测中,需按照ASME III规范要求进行阶梯式温度保持,每次升温梯度不超过100℃/h,总保温时间需模拟设计寿命的20%等效时长。实施过程中,红外热像仪与应变计的同步监测可有效识别材料局部性能异变。
多行业应用场景解析
在航空航天领域,某型号火箭发动机燃烧室经高温后抗拉强度检测后,材料极限强度较设计要求提升18%(中国航发研究院,2023)。能源装备领域,宝钢开发的超超临界锅炉管通过该检测优化了微合金化工艺,使620℃工况下抗拉强度保持在650MPa以上。典型应用案例表明,结合数字孪生技术的检测方案可将材料评估周期缩短40%,同时提升高温失效预测准确率至92%。
全链条质量保障体系
为确保检测结果的可追溯性和国际互认,实验室需构建涵盖设备、人员、方法的立体化质控网络。关键措施包括:季度性载荷传感器校准(误差≤±0.5%)、操作人员NAS 410三级认证、环境试验箱多点温场验证(9点测温法)。某国家级材料检测中心通过引入ISO/IEC 17025管理体系,使高温抗拉强度测试的不确定度从3.2%降低至1.8%,数据复现性达到国际领先水平。
技术发展趋势与建议
面向未来极端工况材料检测需求,建议从三个维度深化技术发展:一是开发智能感知型检测系统,集成原位显微观察与大数据分析功能;二是建立多物理场耦合检测标准,涵盖热-力-化协同作用机制;三是构建高温材料性能数据库,推动检测结果的设计应用转化。预计到2030年,融合机器学习的预测性检测技术可使高温材料研发周期缩短50%,为重大装备国产化提供关键技术支撑。
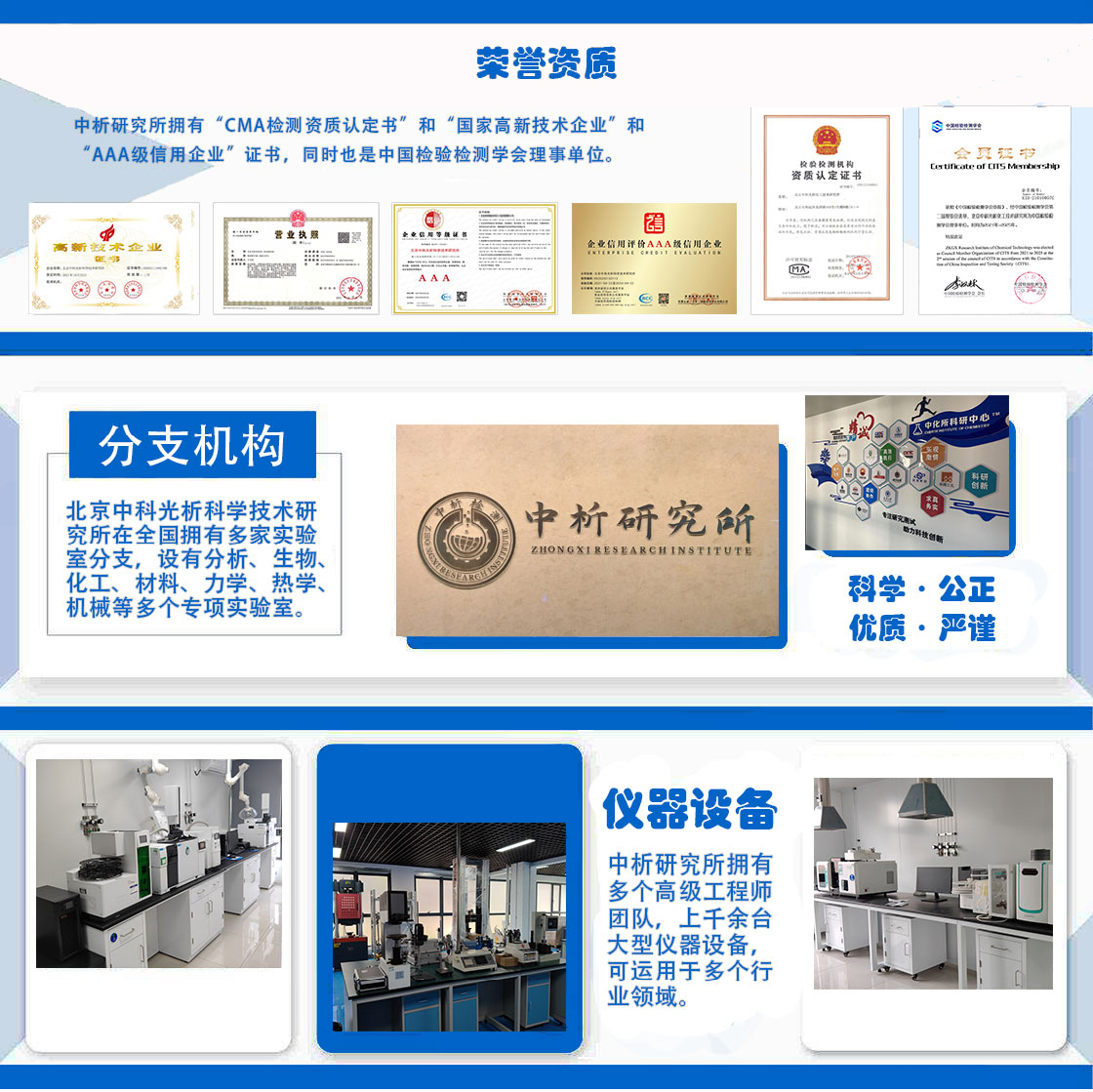
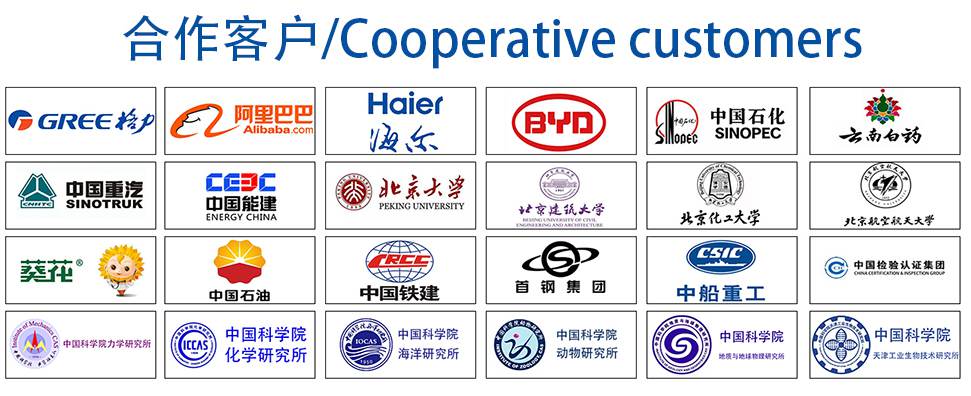