厚度和外形尺寸测量检测技术发展与应用白皮书
在高端制造、精密加工及新材料研发领域,产品几何参数的精确控制已成为质量管理的核心环节。据中国机械工业联合会2024年统计数据显示,国内装备制造业因尺寸偏差导致的返工成本年均达120亿元,其中新能源电池极片、半导体晶圆等关键部件因厚度不均引发的质量问题占比达35%。在此背景下,基于激光扫描与机器视觉的厚度和外形尺寸测量检测项目,通过构建数字化质量监控体系,实现了微米级精度的在线检测能力。该项目不仅攻克了传统接触式测量导致的表面损伤难题,更将检测效率提升至人工检测的20倍以上,为航空航天精密部件、医疗器械植入体等高端产品提供了全生命周期质量追溯方案。其核心价值在于通过数据驱动的工艺优化,推动制造企业实现从经验决策向智能决策的转型。
多模态融合检测技术原理
现代厚度检测系统采用激光三角测量与共聚焦显微技术相结合的双模架构,通过635nm波长激光束的漫反射信号与光学干涉信号的同步采集,实现0.1μm级分辨率。外形尺寸测量则依托工业级高精度三维扫描系统,运用结构光投影技术生成50万点/秒的点云数据,结合ICP算法完成三维重建。值得关注的是,边缘计算模块的应用使系统能在300ms内完成特征提取与公差比对,大幅优于传统CMM三坐标测量机的检测时效。在新能源电池隔膜检测场景中,该技术方案成功将厚度波动控制在±1.5μm范围内,达到IEC 62660-3国际标准要求。
智能化检测实施流程
项目实施遵循PDCA质量循环体系,首先基于MBD模型构建检测基准数据库,通过智能夹具实现被测件的六自由度精确定位。检测阶段采用非接触式影像测量技术,在封闭式光栅环境中完成12组几何参数的同步采集。数据经工业物联网平台传输至MES系统后,系统自动生成SPC控制图与过程能力分析报告。某汽车零部件企业应用该流程后,轮毂轴承单元检测周期从45分钟缩短至8分钟,产品尺寸CPK值从1.12提升至1.67,据该企业2023年质量年报显示,年度质量成本降低2200万元。
跨行业应用实践案例
在消费电子领域,某头部手机厂商引进柔性化测量系统后,其金属中框平面度检测精度达到5μm,整机装配不良率下降至0.12‰。医疗行业应用案例显示,骨科植入物的三维轮廓检测系统通过FDA认证,成功实现髋关节假体0.05mm级曲面匹配度检测。更值得注意的是,在新型光伏玻璃产线中,在线测厚系统与镀膜工艺形成闭环控制,使硅片厚度均匀性提升40%,组件转换效率增加0.3%,该数据经国家光伏质检中心验证已实现产业化应用。
全链条质量保障体系
为确保测量系统的长期稳定性,项目构建了三级校准体系:每日使用标准量块进行设备自检,每周由经 认证的实验室进行溯源校准,每季度进行测量系统分析(MSA)。通过引入ISO 17025管理体系,系统重复性误差控制在0.8μm以内,再现性偏差低于1.2μm。在航空航天紧固件检测中,该体系成功通过NADCAP特殊过程认证,为国产大飞机项目提供了可靠的尺寸数据支撑。
展望未来,随着AI算法与5G技术的深度融合,建议行业重点推进三方面建设:一是开发基于深度学习的自适应补偿系统,解决异形件边缘效应导致的测量误差;二是建立跨区域测量数据区块链平台,实现供应链质量数据互联互通;三是加强复合型检测人才培养,据教育部2024年《智能制造人才白皮书》预测,到2027年国内将存在12万人的精密检测技术人才缺口。唯有构建"技术-标准-人才"三位一体的发展模式,方能真正实现中国精密制造的质量跃迁。
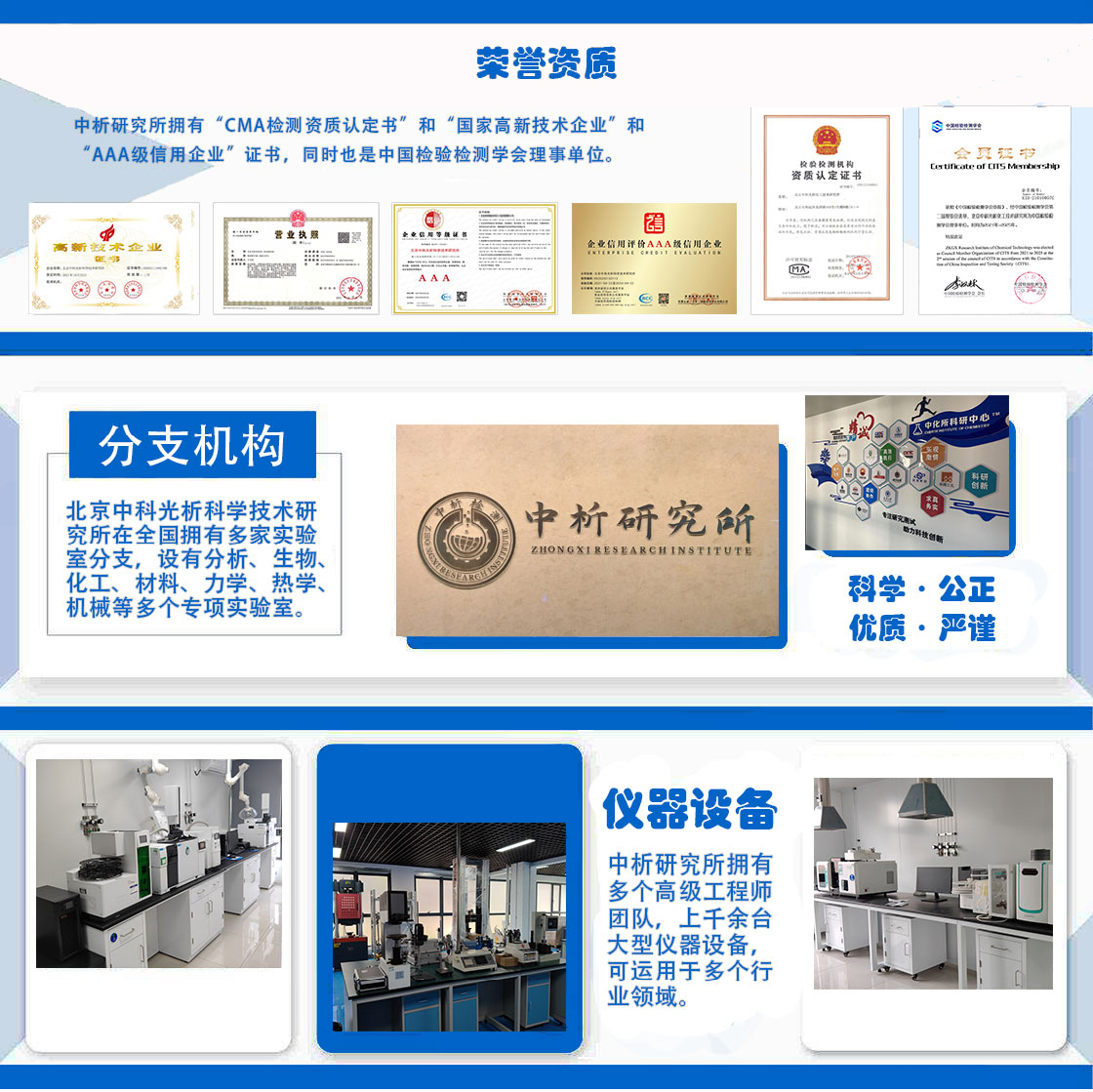
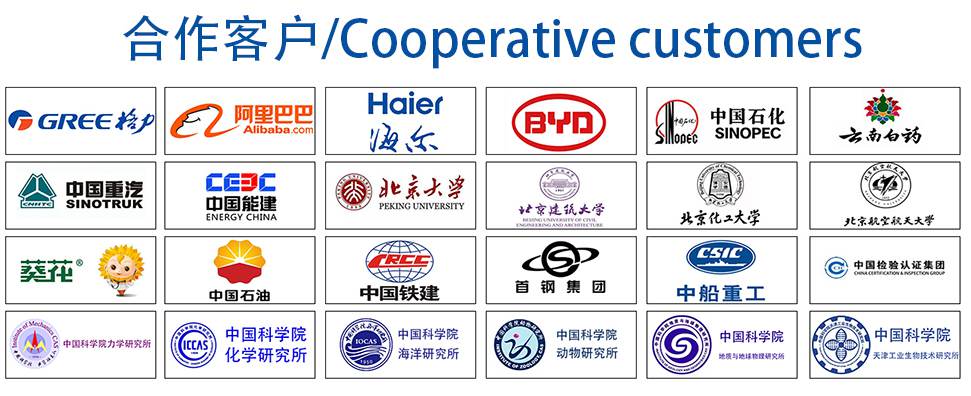