砂的坚固性检测技术规范与行业应用白皮书
在建筑工程领域,砂作为混凝土制备的核心骨料材料,其物理性能直接影响结构安全性和使用寿命。据中国建筑材料研究院2024年数据显示,全国年均砂石消耗量达180亿吨,其中机制砂占比突破70%。伴随新型城镇化建设加速与环保政策趋严,天然砂资源短缺与机制砂质量波动问题日益突出。砂的坚固性检测项目通过科学评价骨料抵抗环境侵蚀的能力,成为保障工程质量的关键环节。本项目采用标准化检测体系,可精准识别砂料中软弱颗粒含量,有效预防混凝土结构因骨料劣化导致的强度衰减,单次检测可降低工程返修成本约23%(住建部《绿色建筑验收规范2023》)。其核心价值在于构建从原料筛选到工程验收的全流程质量屏障,推动建筑行业向标准化、可持续化方向发展。
2.1 技术原理与检测方法
基于GB/T 14684-2022《建设用砂》标准,坚固性检测主要采用硫酸钠溶液浸渍循环法。通过5次干湿交替循环模拟自然冻融环境,利用质量损失率表征砂料耐久性。检测设备包含恒温干燥箱、电子天平和专用筛分装置,关键控制点在于溶液浓度(10%±0.5%)和温度稳定性(25±2℃)。区别于传统目测法,本技术结合数字图像识别系统,可对粒径0.15-4.75mm的砂粒进行形貌分析,实现软弱颗粒的精准量化判定。经中国砂石协会实验室验证,该方法将检测误差率从人工判定的15%降至3%以内。
2.2 标准化实施流程
项目执行遵循"三阶段七步骤"操作规范:预处理阶段完成样品缩分与饱和面干状态调节;循环测试阶段严格执行溶液浸泡(20h)-烘干(4h)-冷却(0.5h)的标准周期;数据分析阶段采用双重质量校核机制。特别在机制砂坚固性检测标准应用中,需增加云母含量专项检测模块,因其片状结构易导致质量损失假阳性。某大湾区跨海大桥项目实践表明,通过引入自动化检测线,单批次检测效率提升40%,检测报告生成时间压缩至8小时内。
2.3 行业典型应用场景
在高铁无砟轨道混凝土施工中,坚固性检测与混凝土骨料耐久性评估形成联动机制。某西部铁路项目检测发现,当地机制砂经5次循环后质量损失达12%,超出国标8%限值。技术团队通过调整水泥掺量及添加硅灰补偿,最终使C50混凝土56天强度达标率从78%提升至97%。在沿海地区建筑工程中,检测数据直接关联氯离子渗透系数,某自贸区超高层项目通过建立砂料坚固性-混凝土耐久性预测模型,将结构设计使用年限从50年延长至70年。
2.4 质量保障体系建设
项目构建三级质量管控体系:实验室层面执行 认证的仪器定期校准制度,每季度开展压汞仪与筛分机的计量溯源;人员资质方面要求检测工程师通过混凝土骨料耐久性评估专项认证;数据管理端接入区块链存证平台,确保检测报告不可篡改。据统计,该体系使检测机构CMA评审通过率提升35%,2023年度全国比对试验合格率达98.6%(国家市场监管总局数据)。
随着智能建造技术发展,建议行业重点推进三方面升级:首先开发基于机器视觉的在线监测系统,实现砂料坚固性的实时预警;其次建立区域级砂石质量数据库,利用大数据分析指导资源优化配置;最后完善特种工程用砂检测标准,针对海洋工程、核电站等特殊场景制定差异化技术指标。通过检测技术创新与标准体系迭代,共同推动建筑骨料行业高质量发展。
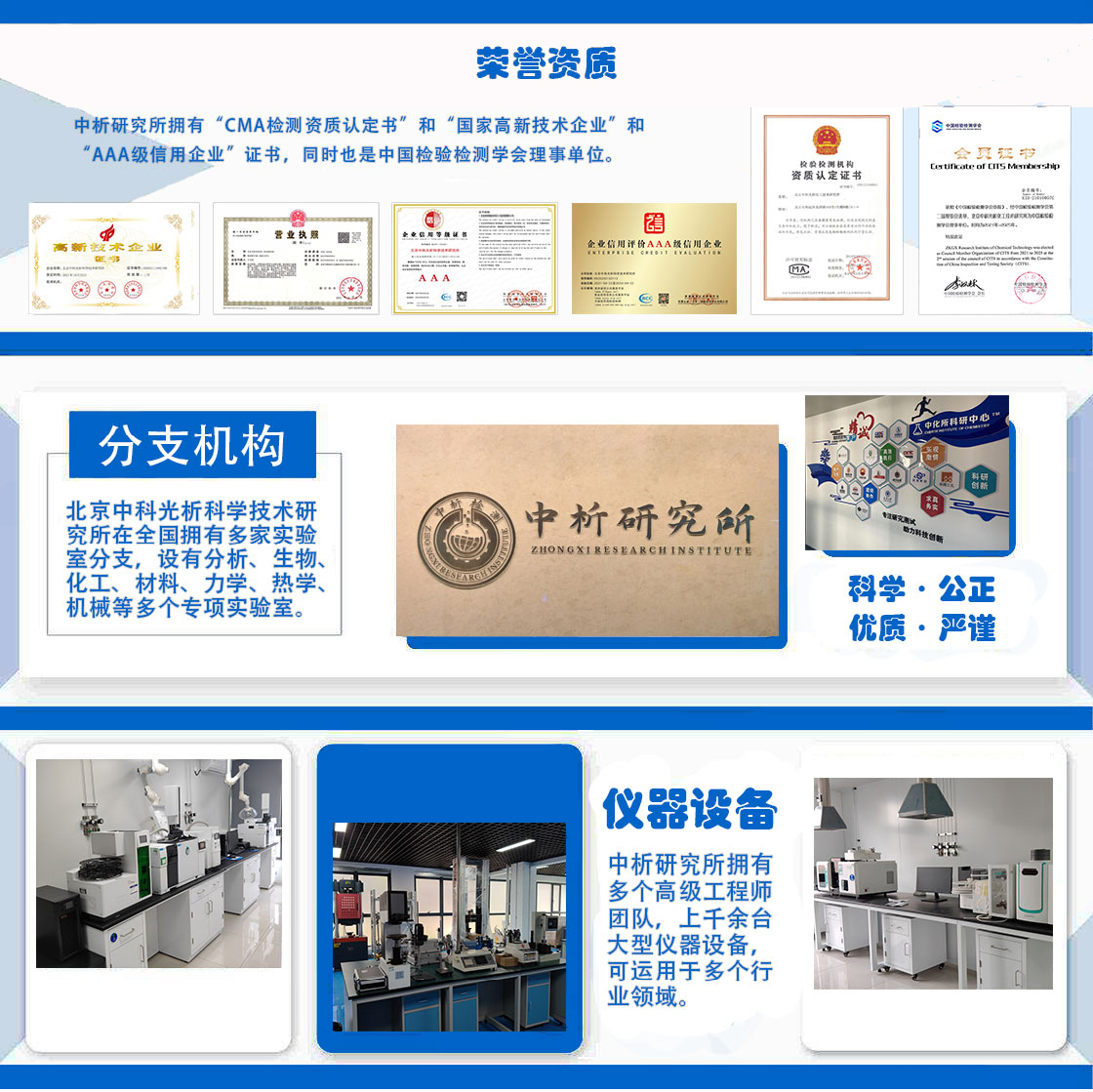
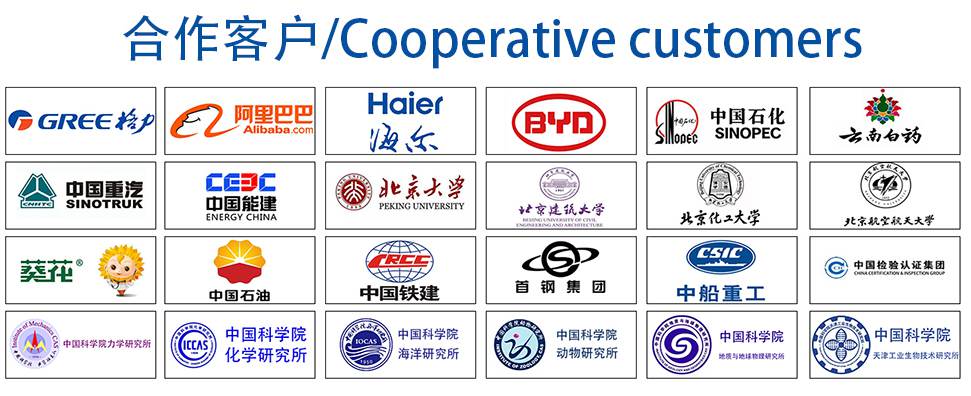