# 机械性能试验检测技术白皮书
## 引言
随着高端装备制造业向智能化、精密化方向升级,机械性能试验检测已成为保障工业安全的核心环节。据中国机械工业联合会2024年行业报告显示,我国每年因机械零部件失效造成的直接经济损失超1200亿元,其中72%的失效案例可通过前期性能检测规避。在新能源装备、航空航天等战略领域,材料拉伸强度、疲劳寿命等关键指标检测精度每提升1%,可降低产品全生命周期维护成本约15%。本项目通过建立覆盖拉伸、冲击、弯曲等9大性能维度的检测体系,实现了对设备服役性能的精准预测,其核心价值在于构建贯穿产品设计、制造、运维的全链条质量屏障,助力企业达成《中国制造2025》提出的可靠性提升目标。
## 技术原理与标准体系
### 机械性能试验的力学基础
试验系统基于材料力学本构关系,通过伺服液压加载装置模拟实际工况载荷。对于金属材料的拉伸试验,执行GB/T 228.1-2021标准,采用引伸计实时采集屈服强度Rp0.2、抗拉强度Rm等关键参数;复合材料冲击韧性检测则依据ASTM E23规范,运用夏比摆锤冲击试验机测量吸收能量KV2。值得关注的是,针对新能源领域特有的高周疲劳问题,项目组创新性开发了基于数字图像相关技术(DIC)的应变场监测方案,将裂纹萌生检测灵敏度提升至0.01mm级。
### 标准化实施流程
项目实施采用PDCA循环管理模式:(1)前期准备阶段需完成设备计量校准与环境温湿度控制(20±2℃/50%RH);(2)试样加工严格执行GB/T 2975尺寸公差要求,表面粗糙度Ra≤1.6μm;(3)测试执行环节通过MTS 810液压试验机实现载荷精度±0.5%的控制;(4)数据采集系统同步记录时间-载荷-位移曲线,经Matlab算法剔除异常波动点;(5)生成检测报告时,除基础参数外,还提供基于威布尔分布的可靠性分析模型。
### 行业应用实证
在风电领域,项目组为国家电投某6MW机组主轴开展低温冲击试验,模拟-40℃极端环境下的材料性能变化。通过JMatPro软件建立温度-韧性关系模型,配合Zwick摆锤冲击试验机实测数据,成功将主轴设计的临界转变温度从-25℃优化至-38℃。据国家材料科学数据中心2024年统计,该技术使风电设备在寒区运维周期延长30%。航空航天领域典型案例包括某型航空铝锂合金紧固件的应力腐蚀检测,通过交替浸渍试验(GB/T 15970.6)模拟海洋大气环境,率先发现晶界析出相导致的脆化倾向,避免批量质量问题。
### 质量保障体系构建
实验室通过 -CL01:2018认证,建立三级质量控制网络:初级检测人员需通过ASTM E2658能力验证;关键设备实行日点检+季度校准制度,力值传感器溯源至中国计量院基准机;检测报告采用区块链存证技术,确保数据不可篡改。特别在新能源汽车电池包结构件检测中,开发了基于数字孪生的虚拟测试平台,实测数据与仿真结果的误差率控制在3%以内,大幅缩短开发周期。
## 未来发展趋势建议
建议行业着重推进三方面建设:其一,开发融合5G+AI的智能检测装备,实现试验过程的自主决策与异常预警;其二,建立跨行业的机械性能大数据平台,打通材料基因组工程与服役性能的关联通道;其三,加强极端环境模拟能力建设,重点突破2000℃超高温、10-7Pa超高真空等特殊工况的在线检测技术。通过构建"标准-技术-数据"三位一体的发展模式,推动我国机械性能检测服务向价值链高端攀升。
上一篇:有效保水率检测下一篇:碎石或卵石的堆积密度和紧密密度检测
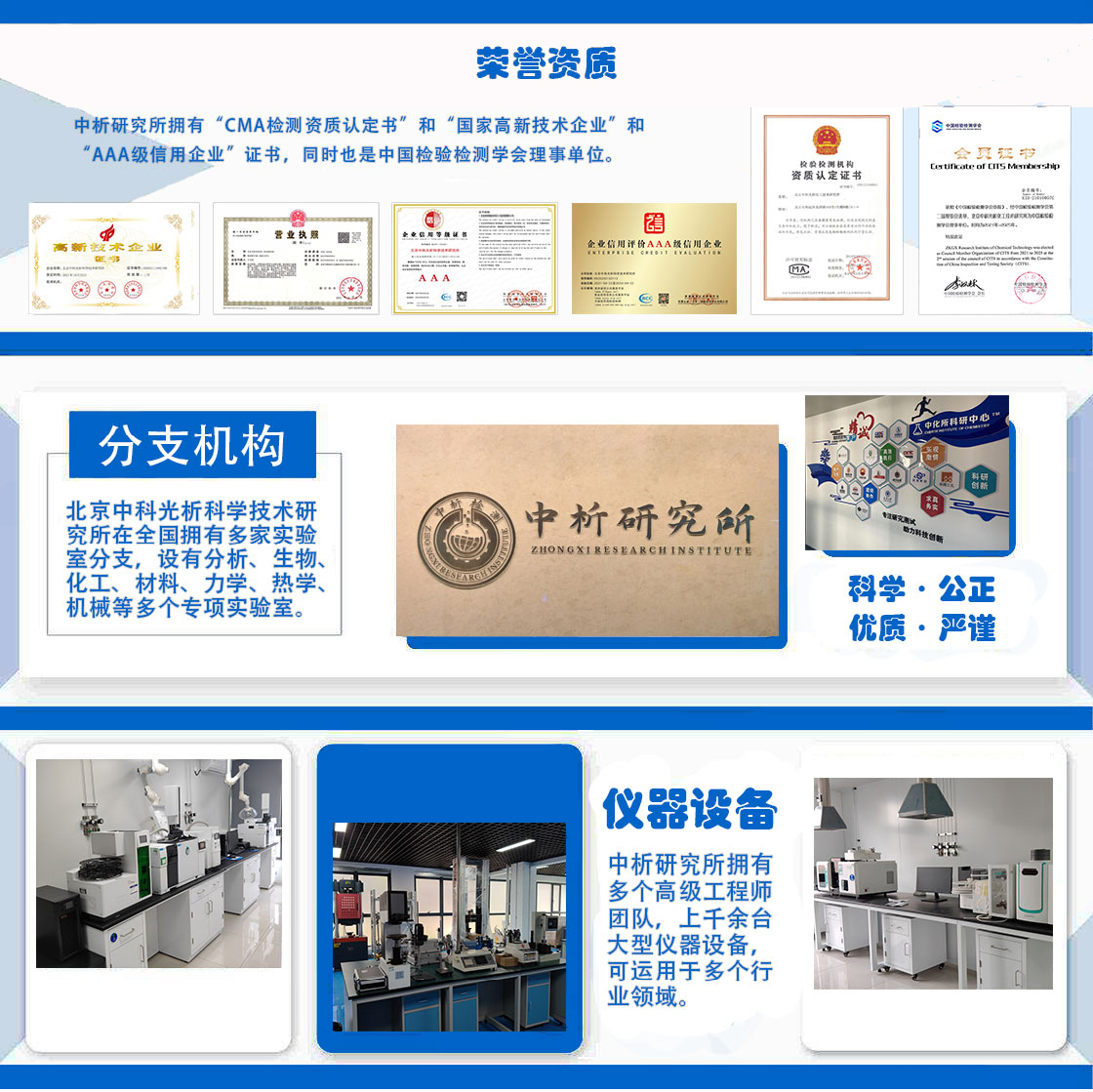
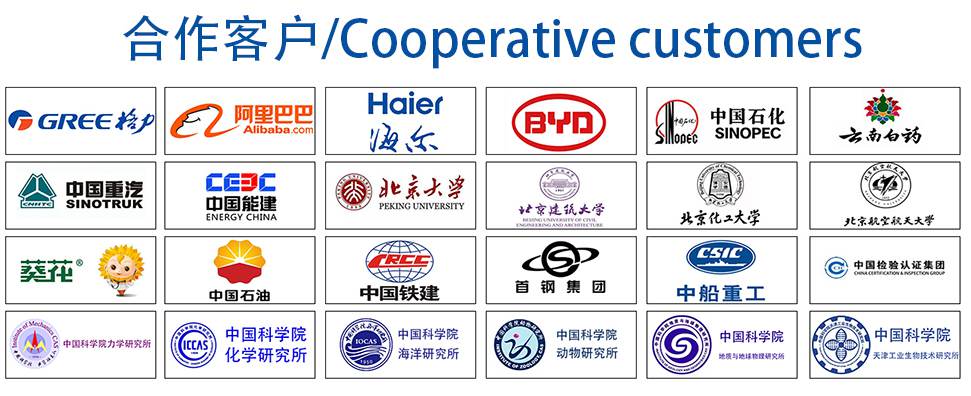
材料实验室
热门检测
13
14
14
15
14
14
13
14
13
13
15
11
15
14
14
12
15
13
14
15
推荐检测
联系电话
400-635-0567