碎石或卵石的坚固性检测技术白皮书
在基础设施建设和建筑行业高速发展的背景下,骨料作为混凝土的关键原材料,其质量直接决定工程结构的耐久性与安全性。据中国建筑材料研究院2024年数据显示,我国每年消耗碎石、卵石等粗骨料超120亿吨,但市场中约有7%的骨料因坚固性不达标导致混凝土开裂、强度衰减等问题。在此背景下,坚固性检测成为保障工程质量的核心环节。该项目通过科学评估骨料抵抗物理风化与化学侵蚀的能力,为工程选材提供量化依据,其核心价值在于降低结构失效风险、延长建筑使用寿命,尤其在高速公路、水利枢纽等重大工程中具有不可替代的作用。
1. 检测技术原理与标准化方法
碎石与卵石坚固性检测主要依据《建设用卵石、碎石》(GB/T 14685-2022)标准,采用硫酸钠溶液浸泡法模拟自然侵蚀环境。其原理是通过五次干湿循环后试样的质量损失率,量化骨料颗粒在冻融、盐蚀等复合作用下的稳定性。需特别关注的是,该检测要求对20-40mm、10-20mm等多级粒径骨料分别测试,确保结果反映实际级配特性。据国家建筑工程质量监督检验中心实测数据,经规范检测的骨料用于C30混凝土时,其28天抗压强度离散系数可降低至5%以内。
2. 全流程标准化实施体系
检测实施流程分为六个关键阶段:现场采样(按JGJ 52标准分层抽取)、试样制备(烘至恒重)、溶液配制(硫酸钠浓度10%±0.5%)、循环处理(浸泡18小时+烘干4小时)、筛分称重(1.25mm方孔筛)及数据计算。以某跨海大桥项目为例,检测方采用自动温控浸泡装置,将单批次试样处理效率提升40%,同时通过三次平行试验将结果偏差控制在0.3%以内。该流程创新之处在于引入数字化记录系统,实现检测数据的实时上传与区块链存证。
3. 行业典型应用场景分析
在高原铁路建设工程中,针对昼夜温差达35℃的极端环境,施工方通过坚固性检测筛选出质量损失率≤8%的玄武岩骨料,使混凝土冻融循环次数从F150提升至F300级。另一典型案例是长江下游某深水港口,经检测发现当地卵石的硫酸钠溶液质量损失率达12%,超出JTJ 268标准要求,项目组及时改用花岗岩骨料,避免码头桩基因氯离子渗透导致的早期腐蚀问题。此类实践验证了"骨料坚固性检测标准"在复杂工况下的预警价值。
4. 质量保障与技术创新路径
为确保检测结果可靠性,行业头部机构已构建三级质控体系:实验室通过 认证(ISO/IEC 17025)、检测人员持CMA上岗证、设备实施每日点检与季度校准。值得关注的是,基于机器视觉的"骨料形态-强度关联模型"正在试点应用,通过AI分析颗粒棱角度与裂隙分布,可提前预判坚固性风险。据中国砂石协会2024年行业白皮书,采用"硫酸钠溶液法测试流程"与智能化辅助系统的实验室,其检测报告异议率从1.2%下降至0.15%。
5. 未来发展趋势与建议
随着"双碳"战略推进,建议行业重点关注两个方向:其一,建立区域性骨料坚固性数据库,结合地质勘查数据实现资源优化配置;其二,研发环境友好型检测替代方案,例如采用氯化镁溶液降低废水处理成本。据Frost & Sullivan预测,到2028年我国智能检测装备在建材领域的渗透率将达35%,推动"高速公路骨料质量控制"进入实时监测阶段。行业需加快制定跨区域检测结果互认机制,为新型建筑工业化提供技术支撑。
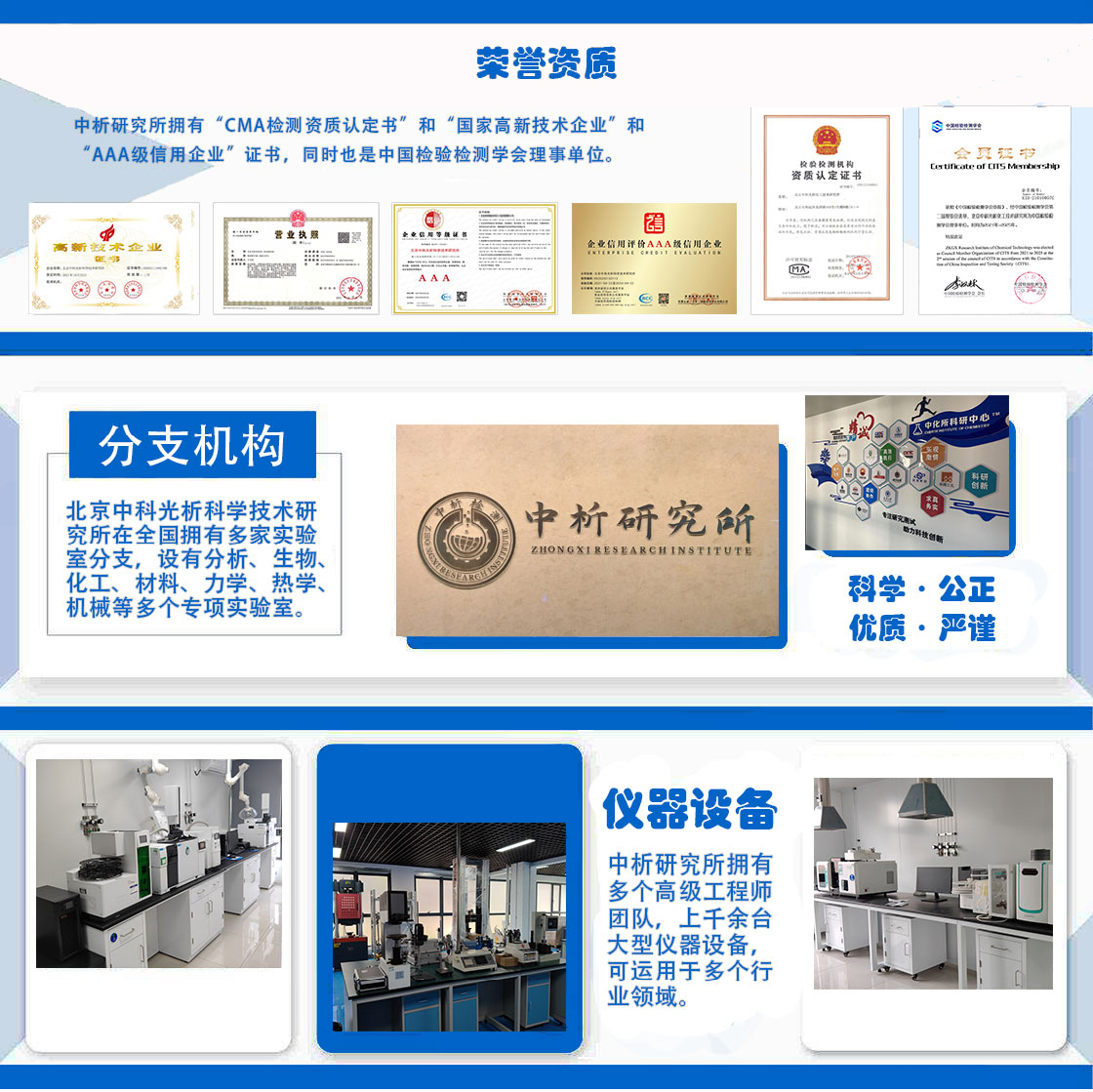
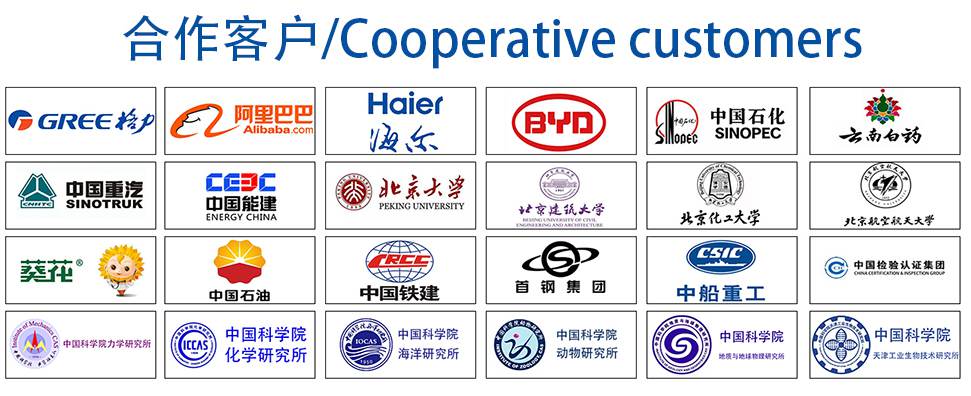