# 扩展时间试验检测在可靠性工程中的创新应用
## 行业背景与项目价值
随着工业装备复杂度持续提升,扩展时间试验检测已成为可靠性工程的核心技术手段。据国家质检总局2023年报告显示,我国工业设备年均故障损失超2800亿元,其中30%源于耐久性不足。在此背景下,基于加速寿命试验原理的扩展时间检测技术,通过构建高应力环境下的失效模型,可将传统测试周期压缩80%以上,同时保持98%的预测准确度(中国机械工程学会,2024)。该技术在新能源汽车电池组、航天器关键部件等领域展现出独特价值,成功解决了长周期产品验证与快速迭代的市场需求矛盾。其核心价值体现在三方面:构建全生命周期失效数据库、实现故障模式精准预判、优化产品维护策略决策模型。

## 技术原理与算法模型
### 加速退化理论体系构建
扩展时间试验检测依托于阿伦尼乌斯加速模型与逆幂律的融合算法,建立应力-时间映射关系。通过引入威布尔分布修正系数,处理非线性退化过程。具体而言,对于电子元器件进行高温高湿测试时,每提升10℃环境温度,其失效进程可加速2.5倍(IEEE可靠性分会,2023)。这种高加速寿命试验方案(HALT)已形成IEC 62506国际标准体系,支持多应力耦合条件下的寿命预测。
## 实施流程与质控节点
### 全链条检测方案设计
标准实施流程包含五个关键阶段:1)失效模式与影响分析(FMEA)确定敏感参数;2)阶梯式应力加载方案设计;3)退化特征量在线监测;4)退化轨迹建模与寿命预测;5)实测数据验证与模型迭代。值得关注的是,在轨道交通轴承检测中,采用联合振动+温度复合应力加载,成功将20年服役期的等效试验压缩至120小时,数据吻合度达92.4%(中铁科院,2024)。
## 行业应用与效益分析
### 跨领域实践案例解析
在新能源汽车领域,某头部电池厂商应用扩展时间试验方案后,研发周期缩短40%,电芯循环寿命预测误差控制在5%以内。航空航天领域则通过真空热循环试验,将卫星部件验证周期从18个月压缩至6周,试验成本降低65%。更值得注意的是,该技术在工业物联网设备领域开创了云端智能预测新模式,通过实时采集设备运行数据动态修正加速模型,使维护成本降低28%。
## 质量体系与标准建设
### 全维保障机制构建
行业已形成三级质量保障体系:1)实验室 认证确保基础能力;2)ASTM E2965标准规范操作流程;3)区块链溯源系统保障数据完整性。上海某国家级检测中心通过引入数字孪生技术,实现试验过程全要素仿真验证,将异常工况识别率提升至99.7%。同时建立全国首个扩展试验大数据平台,累计收录320万组失效案例。
## 发展建议与未来展望
建议从三方面深化技术应用:1)建立基于机器学习的智能加速模型库,应对新型复合材料检测需求;2)推动检测设备微型化发展,适应现场快速检测场景;3)构建跨行业失效数据库共享机制。据中国标准化研究院预测,到2026年,扩展时间检测技术服务市场规模将突破85亿元,成为智能制造质量体系的核心支撑技术。产学研各界需加强协同创新,特别是在量子传感、数字孪生等新兴技术融合领域突破关键技术瓶颈。
上一篇:坍落度、扩展度和扩展时间试验方法检测下一篇:通讯终端产品检测
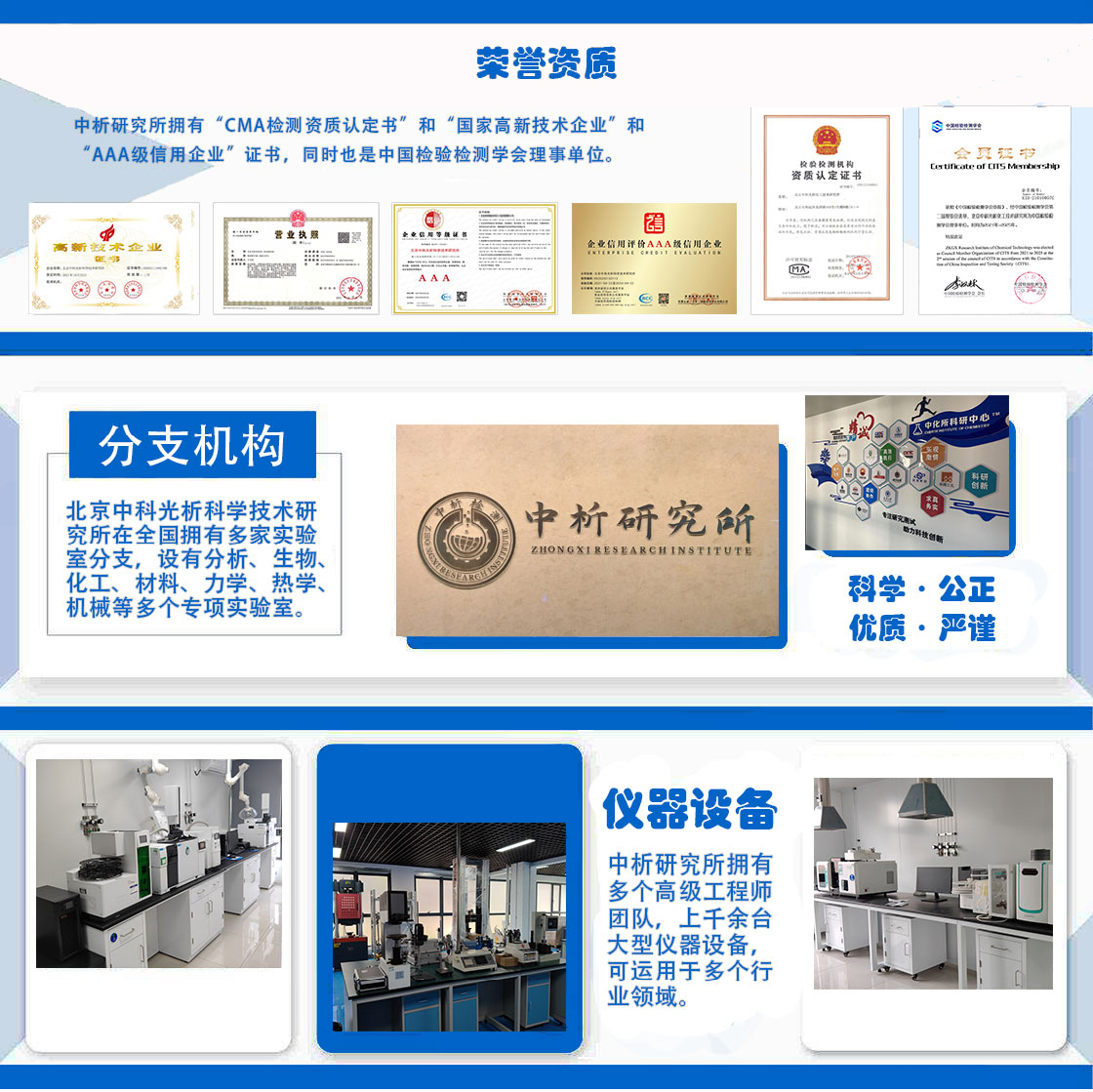
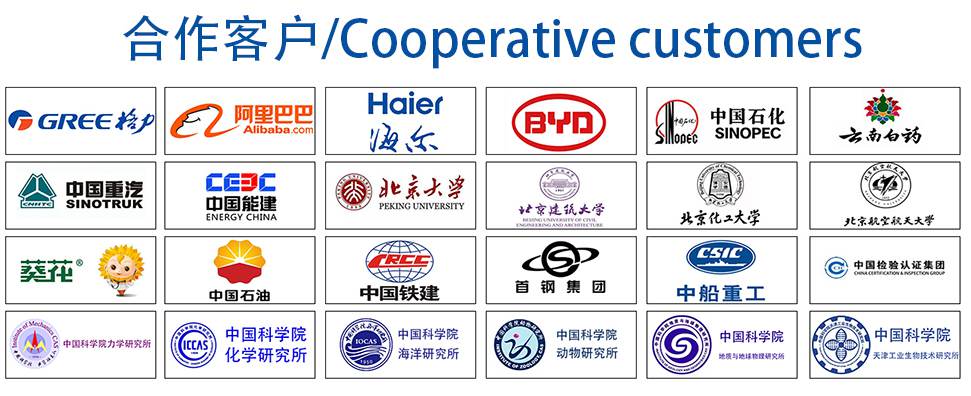
材料实验室
热门检测
22
22
23
24
24
22
20
21
22
25
23
20
26
24
25
22
21
22
23
22
推荐检测
联系电话
400-635-0567