拉伸强度检测基于材料在轴向拉伸载荷下的应力-应变特性,通过万能材料试验机记录试件断裂前的最大载荷值。断裂伸长率则通过标距段变形量计算得出,两者共同构成材料韧脆性评价基准。现行ASTM D638、ISO 527等标准对测试速率、试样尺寸和夹持方式作出明确规定。值得注意的是,新一代非接触式光学应变测量系统(如DIC数字图像相关技术)的应用,使应变测量精度从传统引伸计的±2%提升至±0.5%,有效解决了高弹性体材料滑移误差问题。
## 标准化实施流程与质控要点检测流程涵盖试样制备、环境调节、设备校准、测试执行四个阶段。以汽车用TPV弹性体检测为例,需按ISO 37标准制备哑铃型试样,在23±2℃、50%RH环境下调节24小时后进行测试。关键质控节点包括夹具同轴度校正(偏差≤1%)、拉伸速率控制(500mm/min±10%)以及数据采集频率设置(≥100Hz)。据国家质检总局2024年专项调查,严格执行标准流程可将检测结果离散度从12.3%降低至4.8%。
## 行业应用场景与典型案例在医疗导管生产领域,材料断裂伸长率检测直接关系产品安全阈值。某跨国企业采用GB/T 1040标准对聚氨酯导管进行多点检测,通过建立拉伸强度-壁厚度的回归模型,成功将导管破裂事故率从0.7%降至0.15%。而在风电叶片用环氧树脂体系开发中,运用动态力学分析(DMA)联用拉伸测试,可同步获取储能模量(E’)与断裂伸长率的温度依存性数据,为材料低温韧性优化提供关键依据。
## 质量保障体系构建策略完善的质量保障需贯穿设备管理、人员能力、数据追溯三大维度。实验室须定期进行计量溯源性验证,使用标准样品(如ERM-EF001系列)进行能力验证。人员培训应覆盖材料学基础、设备操作规范和 -CL01认可准则要求。某第三方检测机构通过部署LIMS系统,实现检测数据自动采集与区块链存证,使报告可追溯性达到ISO/IEC 17025:2017的A级要求。
## 技术展望与发展建议随着智能传感与机器学习技术的融合,拉伸测试正朝着智能化方向发展。建议行业重点推进三方面建设:开发基于机器视觉的实时缺陷检测系统,建立材料性能-微观结构的多尺度关联数据库,以及制定适应新型复合材料的测试标准。特别是在柔性电子器件、固态电池隔膜等前沿领域,需突破现有检测方法在超薄材料(<50μm)和高应变速率(>1000mm/min)场景下的技术瓶颈。据中科院材料研究所预测,到2026年智能化检测设备的市场渗透率将突破40%,推动检测效率提升300%以上。
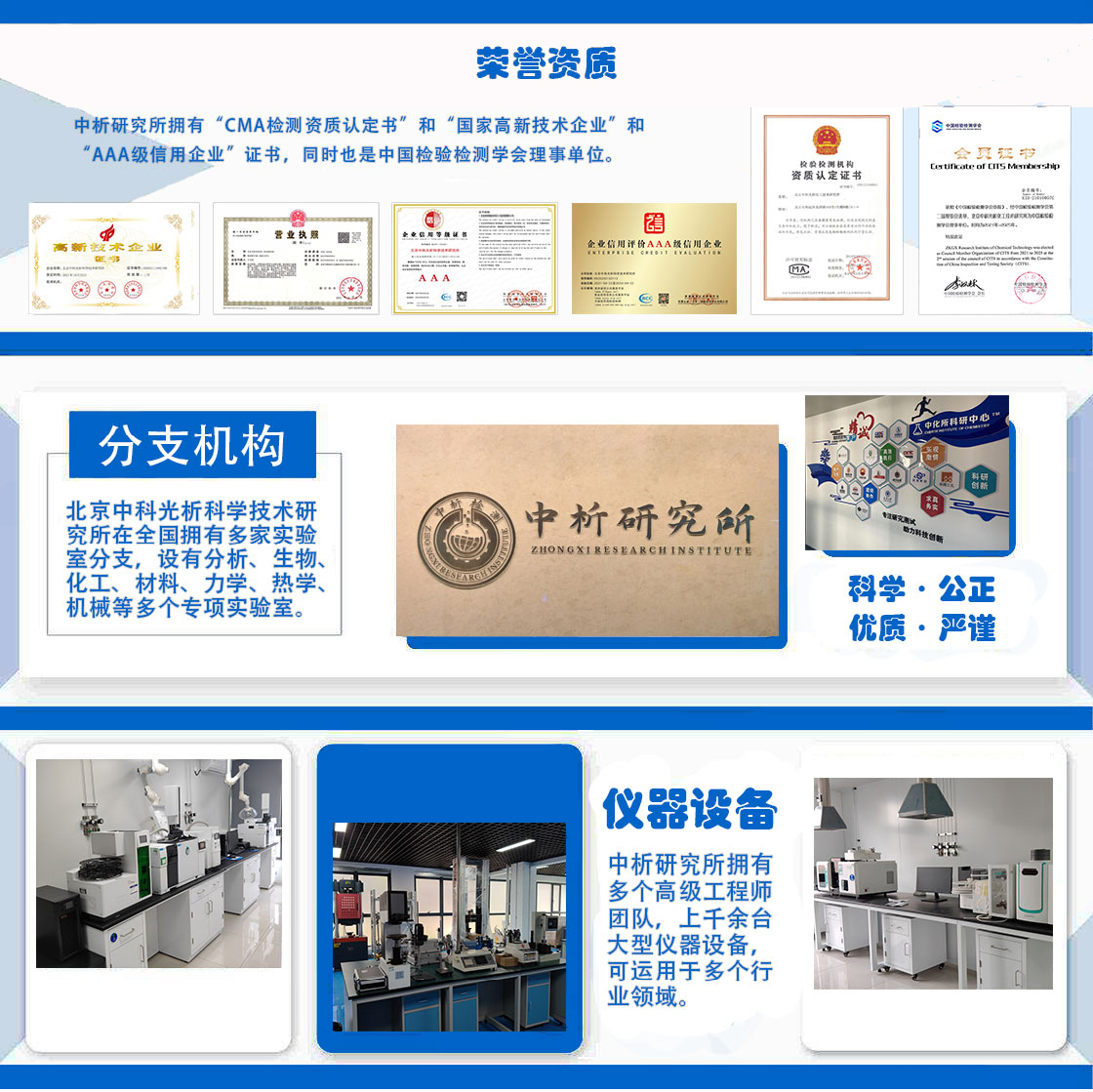
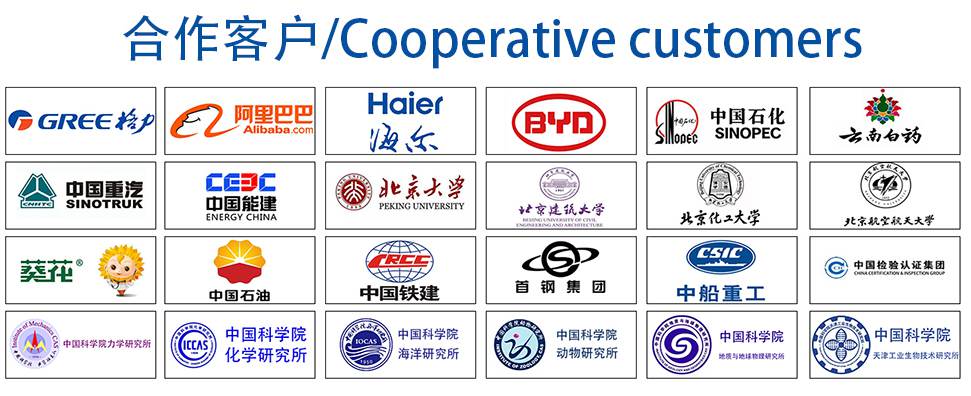