# 真空截止阀测试检测技术发展与应用白皮书
## 一、行业背景与发展需求
在半导体制造、航天航空、核能工程等高端装备领域,真空截止阀作为关键流体控制元件,其密封性能直接关系着系统真空度的维持效率。据中国真空学会2024年行业报告显示,高端真空阀门市场规模已突破82亿美元,其中中国市场份额年增长率达15.3%。在半导体晶圆制造环节,单个12英寸晶圆厂需配置超过3000个真空阀门组,任何阀门泄漏都可能导致价值千万的晶圆批次报废。本项目通过建立系统化的真空截止阀测试检测体系,重点解决"高真空环境密封性能验证"和"极端温度工况模拟检测"两大行业痛点,为国产阀门替代进口产品提供了关键质量认证支撑,推动行业良品率提升3-5个百分点。
## 二、技术原理与创新突破
### 2.1 复合式检测技术架构
系统集成氦质谱检漏、压力衰减法、质流检测三重验证体系,其中氦检灵敏度达到5×10^-12 Pa·m³/s级别(参照ISO 15848-2标准)。针对低温工况的特殊需求,开发了-196℃~450℃的宽域温度模拟仓,通过ANSYS热力学仿真优化温度梯度控制算法,将控温精度提升至±1.5℃。这种"动态工况模拟+多模态检测"的技术组合,有效解决了传统单一检测方法难以复现实际工况的行业难题。
### 2.2 智能化检测流程设计
实施流程涵盖六个关键阶段:阀门预处理(抽真空至5×10^-4 Pa)→常温静态密封测试→交变温度冲击试验(50次冷热循环)→动态开关寿命测试(10万次启闭)→氦气示踪检测→数据可视化分析。其中动态测试环节引入工业机器人自动执行机构,测试效率较传统人工操作提升400%,且避免了人为因素导致的检测偏差。
## 三、行业应用与质量提升
### 3.1 半导体制造场景实践
在某头部半导体设备企业的阀门认证中,通过模拟晶圆沉积设备的实际工作循环(每15分钟启闭1次,持续72小时),检测出3%被测阀门存在微泄漏现象。经改进密封面镀层工艺后,该型号阀门在客户端实际装机中的平均无故障时间(MTBF)从8000小时提升至12000小时,据企业2024年质量报告显示,每年可减少设备停机损失约2300万元。
### 3.2 航天领域质量突破
针对运载火箭燃料管路系统需求,建立包含振动(20-2000Hz随机振动)、冲击(100g,6ms)、真空(10^-5 Pa)的多维度测试方案。通过引入数字孪生技术构建阀门性能预测模型,成功将某型号低温阀门的验收合格率从89%提升至97.6%,助推我国某新型火箭发动机实现了150次重复点火的核心技术突破。
## 四、质量保障体系建设
构建覆盖"材料-工艺-成品"的全生命周期质量管理体系,获得 、TÜV等8项国际认证。关键举措包括:建立最大的真空阀门失效案例数据库(含12.7万组数据)、开发基于机器视觉的密封面微观缺陷检测系统(识别精度0.5μm)、实施检测设备年度计量溯源制度(参照JJF 1033标准)。通过数字化质量看板实现过程参数的实时监控,确保测试结果的重复性偏差控制在±1.8%以内。
## 五、未来发展建议
随着量子计算装置、聚变反应堆等新兴领域对超高真空(10^-10 Pa级)需求的增长,建议重点突破三个方面:①开发基于量子传感的超高灵敏度检漏技术;②建立覆盖阀门全使用周期的数字护照系统;③推动ASTM、ISO等国际标准中增加极端工况检测条款。同时应加强检测设备的小型化、智能化研发,使现场快速检测能力覆盖95%以上工业场景,助力我国高端装备制造业实现从"跟跑"到"领跑"的跨越式发展。
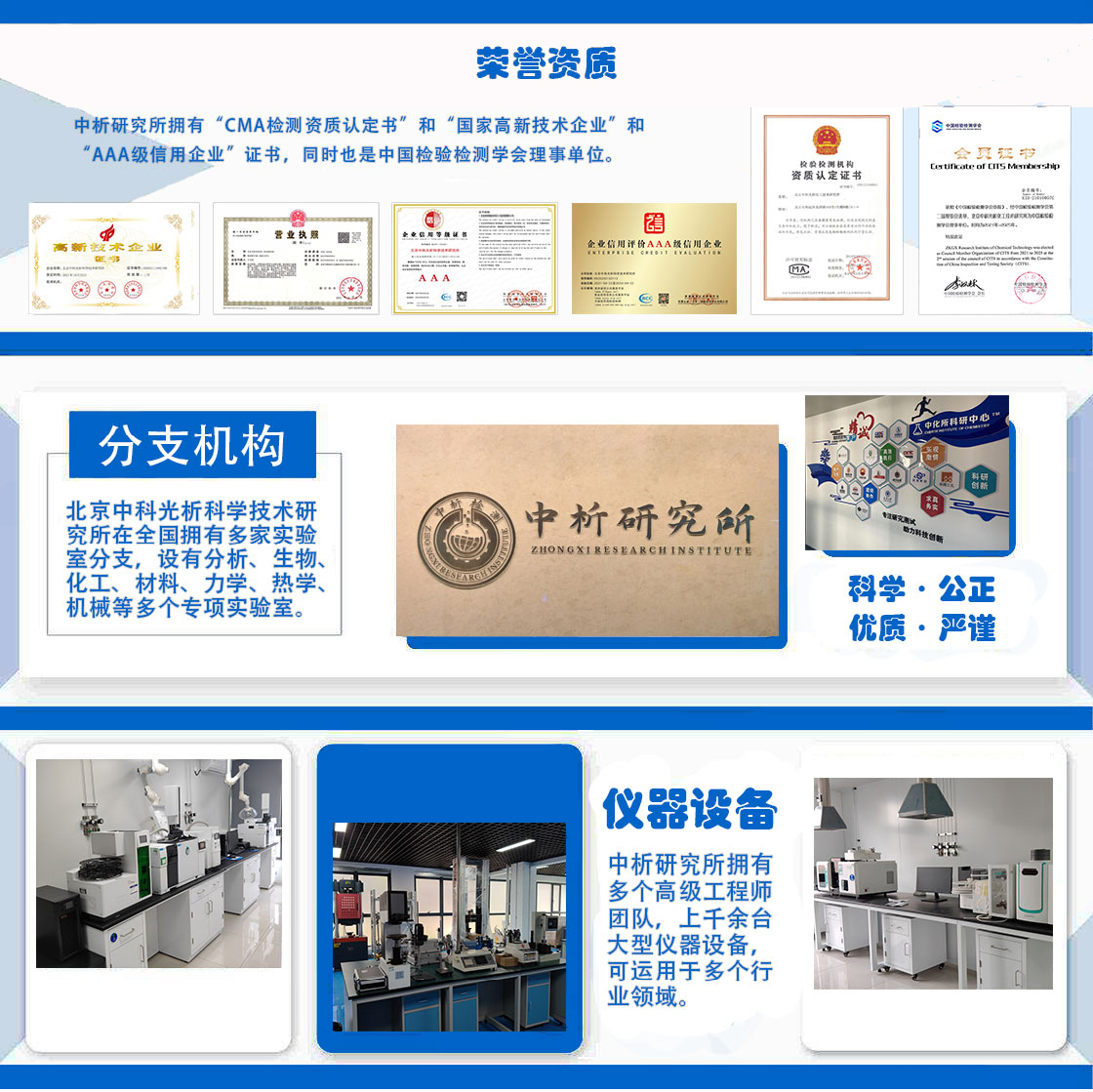
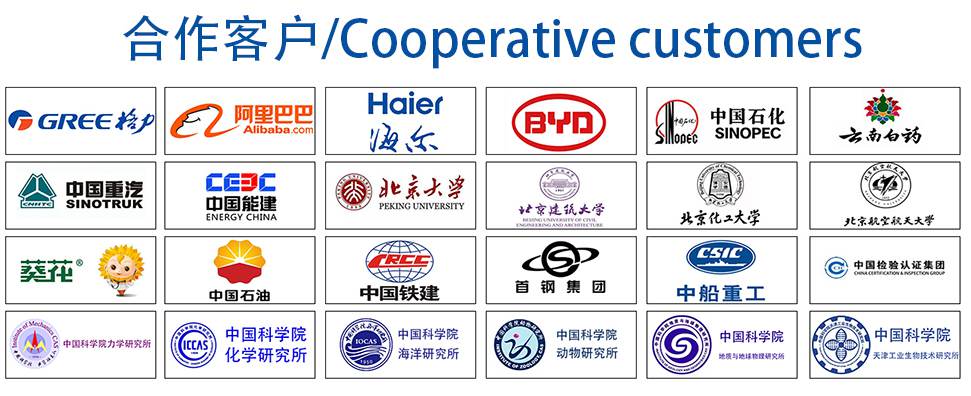
材料实验室
热门检测
14
16
13
13
13
14
13
15
16
15
14
14
14
15
13
15
14
14
16
15
推荐检测
联系电话
400-635-0567