老化结果评定检测的关键项目及方法
一、物理性能检测项目
-
- 拉伸强度与断裂伸长率:通过万能材料试验机测定材料老化前后的抗拉强度及断裂延伸率,评估材料韧性退化。
- 硬度测试:使用邵氏硬度计(橡胶/塑料)或洛氏硬度计(金属)检测表面硬化或软化现象。
- 冲击强度:利用摆锤冲击试验机分析材料脆性变化,常见于塑料和涂层材料。
-
- 收缩率/膨胀率:测量高温、湿度或紫外线照射后的尺寸变化,如塑料件热变形、建筑材料冻融膨胀。
- 形变恢复能力:评估弹性材料(如橡胶)在长期压缩后的回弹性能。
二、化学性能检测项目
-
- 傅里叶红外光谱(FTIR):检测材料化学键变化,识别氧化、水解等降解反应。
- 热重分析(TGA):测定材料热稳定性及分解温度,评估添加剂失效情况。
- 氧化诱导期(OIT):通过差示扫描量热法(DSC)测定抗氧化剂消耗速率。
-
- 接触角测试:分析材料表面亲水性/疏水性变化,预测涂层老化失效。
- pH值测定:评估材料降解产物的酸碱度,如电子元件密封胶酸败。
三、环境老化试验项目
-
- 紫外线(UV)老化:使用QUV试验箱模拟日光紫外线辐射,检测材料黄变、粉化(ASTM G154)。
- 湿热老化:通过恒温恒湿箱(如85℃/85% RH)加速水解反应,评估电子元器件密封性。
- 盐雾试验:模拟海洋气候腐蚀(ASTM B117),检测金属镀层或涂料的耐腐蚀性。
-
- 高低温循环:检测材料在温度急剧变化下的开裂风险(如汽车零部件)。
- 臭氧老化:评估橡胶制品在臭氧环境中的龟裂倾向(ISO 1431-1)。
四、功能性测试项目
-
- 绝缘电阻与介电强度:评估电缆、电子元件老化后绝缘性能(IEC 60243)。
- 导电性变化:检测金属触点或导电涂层的氧化导致的电阻升高。
-
- 透光率与雾度:测定玻璃、塑料薄膜等材料的光学性能退化(ASTM D1003)。
- 色差分析:使用色差仪量化材料变色程度(ΔE值),如户外建材的褪色评估。
五、微观形貌分析
- 扫描电镜(SEM):观察材料表面裂纹、孔洞等微观结构破坏。
- 原子力显微镜(AFM):分析纳米级表面粗糙度变化,适用于精密涂层检测。
六、结果评定标准
- 定量指标:设定性能保留率阈值(如拉伸强度下降≤20%为合格)。
- 定性评级:根据GB/T 1766等标准对粉化、开裂等级进行目视评分。
- 寿命预测模型:结合Arrhenius方程推算材料在实际环境中的使用寿命。
七、行业应用示例
- 光伏组件:需通过IEC 61215标准,检测UV老化后功率衰减、EVA胶膜黄变。
- 汽车内饰材料:依据SAE J2412进行高温暴晒试验,评估气味释放与部件变形。
- 医用塑料:执行ISO 10993-9生物相容性老化测试,确保灭菌后性能稳定。
结语
上一篇:耐湿热性检测下一篇:拉伸强度和断裂伸长率检测
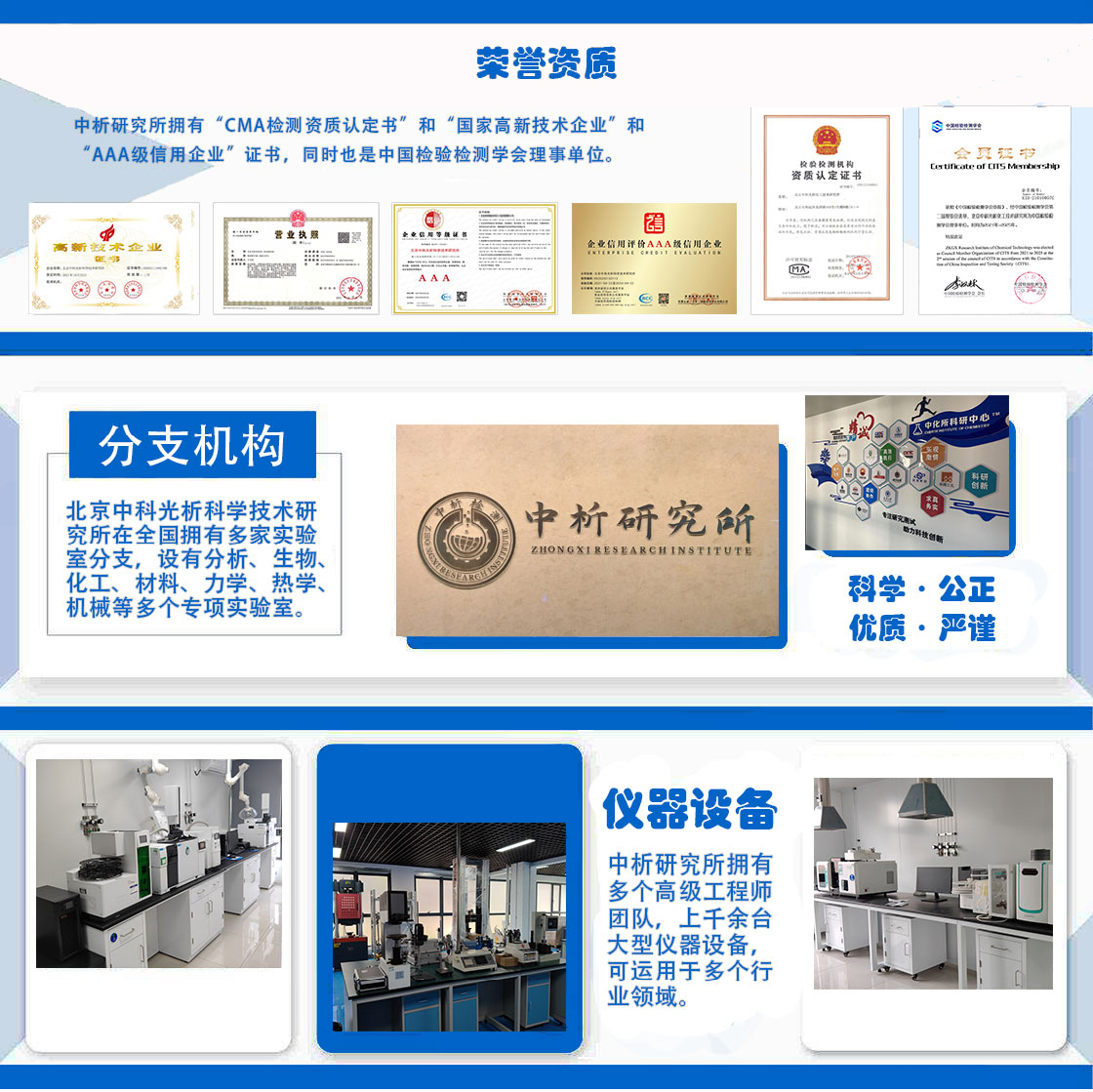
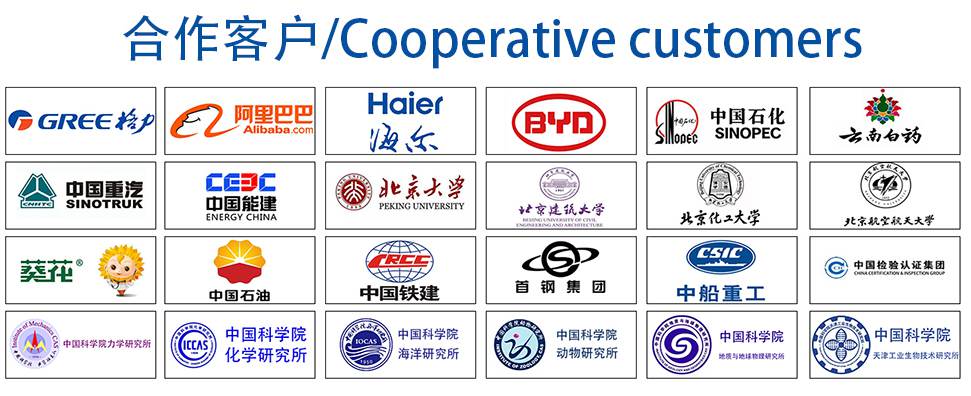
材料实验室
热门检测
55
48
49
54
55
54
53
48
50
46
48
44
53
52
51
50
51
47
50
47
推荐检测
联系电话
400-635-0567