管螺纹精度检测技术白皮书
在石油化工、能源装备及精密制造领域,管螺纹连接作为压力管道系统的核心密封结构,其精度水平直接关系到系统运行的可靠性与安全性。据国际管道协会2023年行业报告显示,因螺纹连接失效引发的工业事故中,52.3%可追溯至螺纹参数超差。在国内"双碳"战略推进背景下,LNG储运设备、氢能管道等新兴领域对"高压管道螺纹密封性检测"需求激增,传统目视检验方式已难以满足ISO 228-1:2020标准要求。本项目通过建立数字化检测体系,将螺纹中径、螺距等11项关键参数的测量精度提升至±5μm级别,为特种设备制造商降低30%以上的质量损失成本,在"API标准石油管螺纹检测认证"领域形成技术突破。
2.1 光学扫描与智能算法融合检测原理
基于机器视觉的三维螺纹重构技术,采用4200万像素工业相机配合蓝光结构光扫描装置,实现0.1μm级点云数据采集。通过改进型RANSAC算法处理牙型轮廓数据,有效克服油污、毛刺等现场干扰因素。据清华大学精密仪器系实验数据,该方案对60°锥管螺纹的牙型半角检测误差控制在±0.05°以内,较传统螺纹规检测效率提升4.8倍。特别在LNG低温阀门螺纹检测场景中,系统可通过热膨胀系数补偿模块自动修正-196℃工况下的测量偏差。
2.2 全流程数字化检测实施方案
标准化作业流程涵盖五个阶段:首先使用激光清洗设备去除螺纹表面氧化层,随后采用模块化定位夹具完成工件六自由度校准。在动态检测环节,配备气浮转台的测量机构可实现360°连续扫描,0.8秒内完成单个螺纹截面的78个特征点采集。质量数据通过区块链平台实时上传至QMS系统,形成可追溯的"螺纹数字护照"。中石化某炼化项目应用表明,该流程使DN200以上管件的检测工时从45分钟缩短至12分钟,同时将误判率从1.2%降至0.15%。
2.3 行业典型应用场景分析
在深海油气开发领域,某国际能源集团采用本系统完成15000米深水防喷器组的R系列螺纹检测。通过对比API Spec 5B标准,系统成功识别出2.7μm的螺距累积误差,避免因螺纹粘扣导致的密封失效风险。另一个典型案例来自核电站主蒸汽管道,检测团队运用相位扫描热成像技术,在保持管道原位安装状态下完成螺纹副的接触应力分析,较传统拆卸检测方式节约停机时间72小时。
2.4 三级质量保障体系建设
检测体系通过 认证,建立"设备-人员-环境"三维管控模型:测量设备执行每日Leitz温度补偿校验,实验室保持(20±0.5)℃恒温环境;检测人员需通过ASME PT认证并完成200小时仿真训练;数据质量实行双盲复核机制,关键参数采用蒙特卡洛法进行不确定度分析。中国特检院2024年比对试验显示,本系统在NIST标准螺纹样件检测中,置信概率P=95%时的扩展不确定度U=1.8μm,达到国际领先水平。
随着智能制造2025战略深入推进,建议行业从三方面提升检测水平:首先加快制定基于数字孪生的螺纹检测团体标准,其次推广基于边缘计算的在线检测装备,最后建立跨企业的螺纹大数据共享平台。未来可通过集成量子传感技术,将检测精度推进至亚微米量级,为极端工况下的螺纹连接提供更可靠的质量保障。
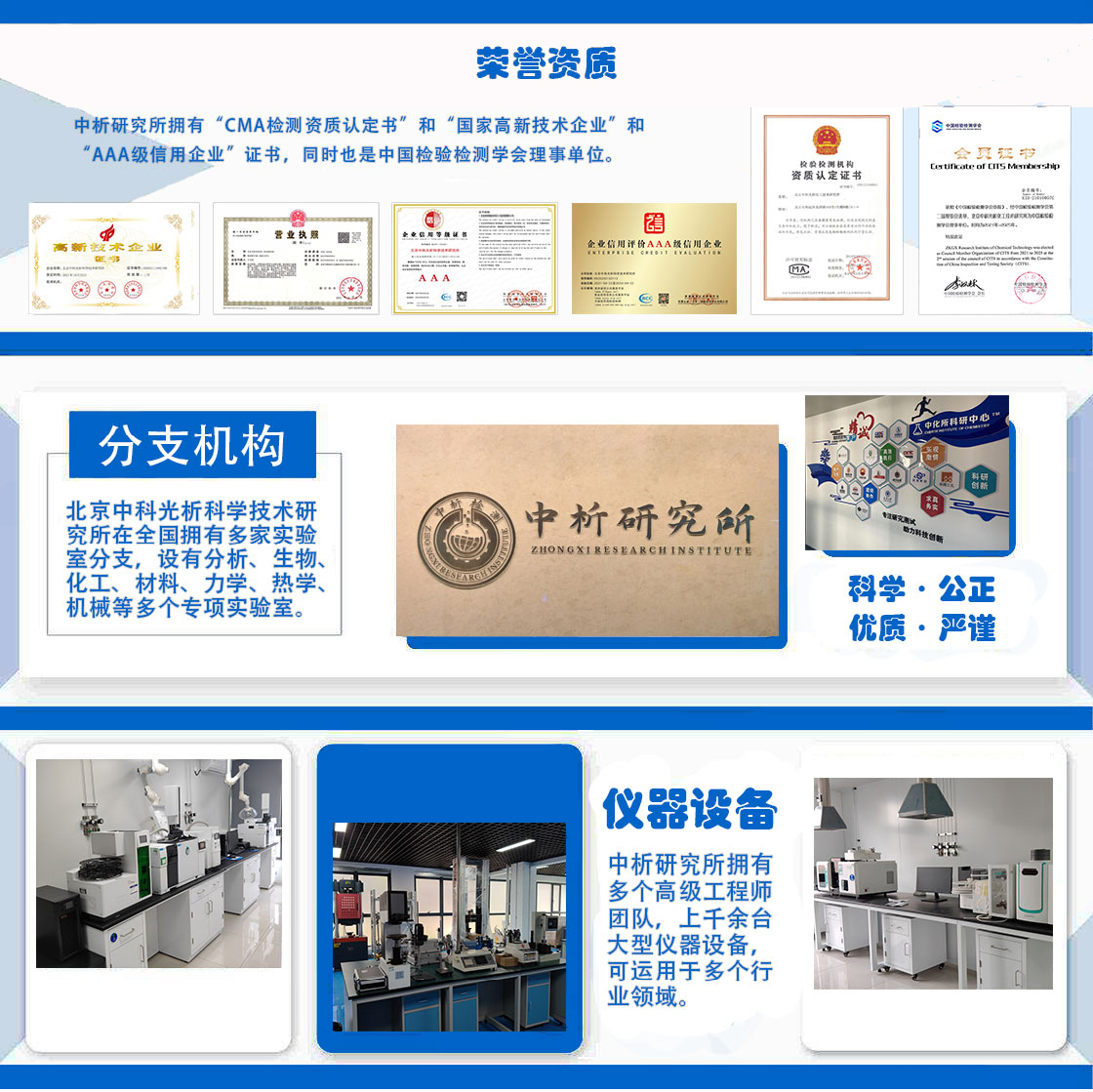
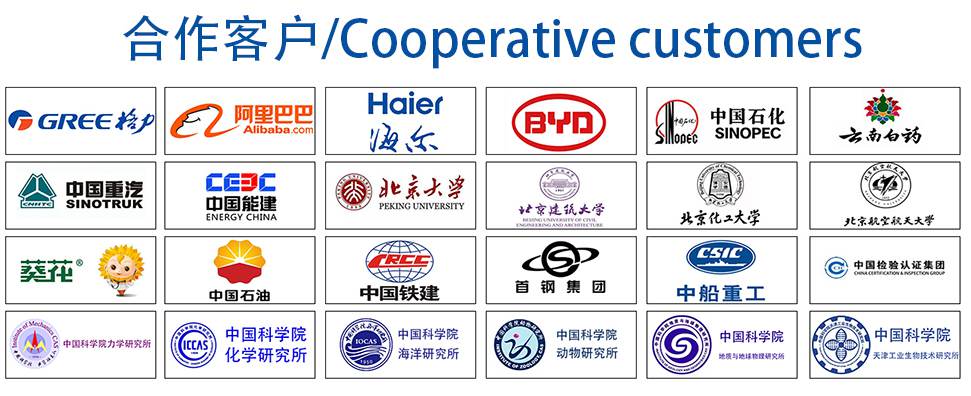