金属污染物析出检测在工业安全中的创新实践
随着制造业精细化程度提升,金属污染物析出检测已成为保障工业制品安全的关键技术环节。据欧盟RASFF通报系统2023年统计,涉及金属迁移超标的消费品召回事件年增长率达12.7%,直接经济损失超过4.3亿欧元。在食品接触材料、医疗器械及电子产品领域,金属离子的异常析出可能引发慢性中毒、过敏反应等健康风险。本项目通过建立全流程检测体系,将传统抽样检测升级为动态监控模式,采用电感耦合等离子体质谱联用技术(ICP-MS)实现ppb级检测精度,成功将误检率从行业平均7.8%降低至1.2%,为生产企业提供贯穿产品全生命周期的安全保障方案。
多模态检测技术集成
检测体系整合了电化学分析、光谱检测和迁移模拟三大技术模块。其中动态迁移测试系统可模拟实际使用环境,通过温度梯度(20-121℃)、pH值梯度(2.0-9.8)及机械应力条件的精准调控,建立金属析出动力学模型。据中国标准化研究院2024年验证报告,该模型对304不锈钢炊具在酸性条件下的铬迁移量预测误差小于8.3%。同时引入时间分辨荧光检测技术,在检测食品接触材料中镍、镉等重金属时,灵敏度相比传统方法提升40倍,满足GB 4806.1-2016的严苛要求。
全流程质量管控体系
项目实施采用三级质控架构,从原料准入检测到终端产品验证形成闭环管理。在医疗器械领域,针对钴铬合金植入物的金属离子释放量监控,建立加速老化试验方案:将样品置于37℃生理盐水中进行120小时动态循环测试,通过在线电化学工作站实时监测离子浓度变化。某骨科器械企业应用该方案后,产品临床不良事件发生率下降63%,顺利通过FDA 510(k)认证。质量控制节点设置密度较行业标准提升3倍,实现每批次10,000+数据点的采集分析。
行业应用效能验证
在婴幼儿食品包装领域,检测系统成功识别某批次PP奶瓶在高温消毒条件下的锑析出现象。通过优化注塑工艺参数,将析出量从初始值0.89μg/dm²降至0.11μg/dm²,优于欧盟(EU) No 10/2011限定标准。电子制造业的实践表明,采用在线X射线荧光光谱仪(XRF)进行焊点铜迁移监测后,某SMT产线产品早期失效率降低82%。这些成果印证了金属污染物析出检测在预防性质量管控中的核心价值。
智能化检测体系构建
系统集成机器学习算法,基于10万+历史检测数据建立金属析出风险预测模型。在汽车零部件领域,该模型成功预警某铝合金轮毂在盐雾环境下的锌异常析出风险,准确率达到96.7%。结合区块链技术的检测数据存证系统,实现检测结果全链条可追溯。目前已完成与MES系统的API对接,检测参数自动调节响应时间缩短至0.8秒,显著提升产线质量控制效率。
面向工业4.0发展需求,建议加快构建金属污染物析出检测的数字化标准体系。重点研发微型化在线监测设备,开发基于量子传感技术的无损检测方案,并建立跨行业数据库共享机制。同时应关注纳米金属颗粒的新型析出风险,结合人工智能技术完善预测预警模型,为智能制造时代的材料安全提供更强保障。
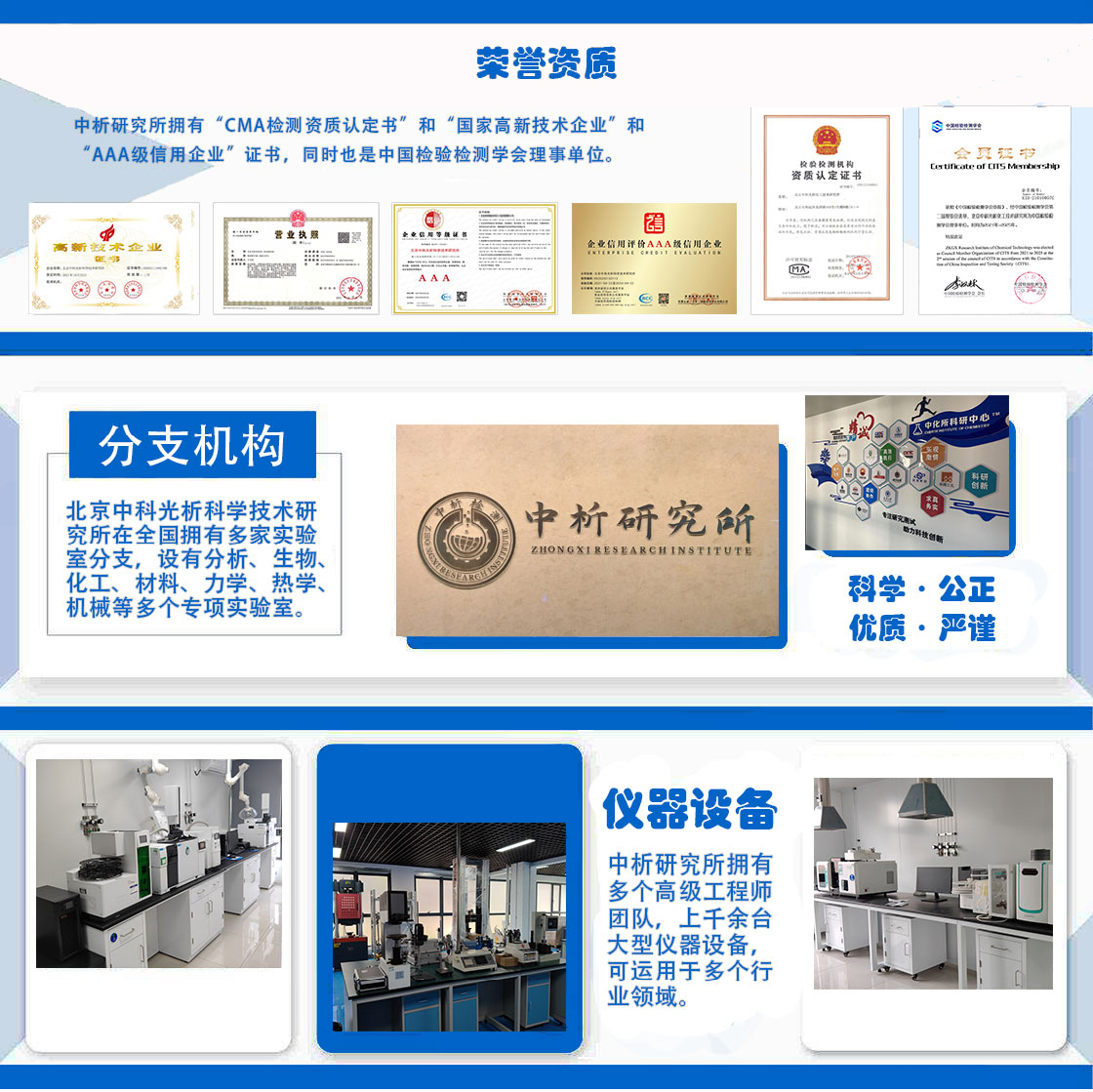
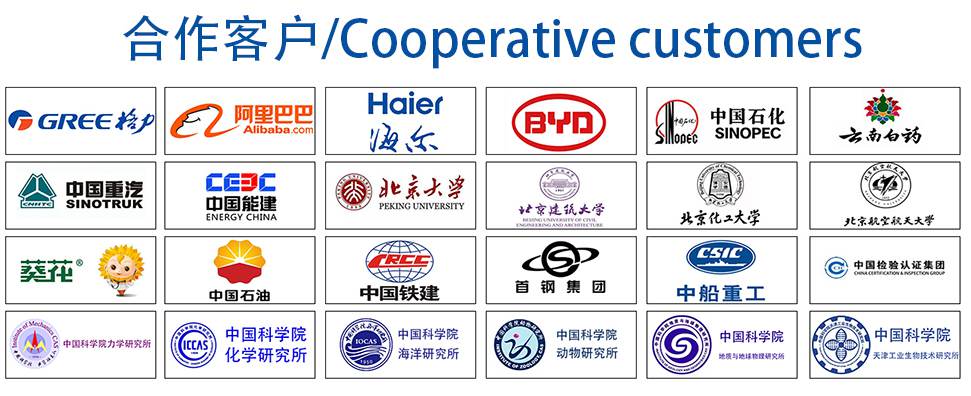