耐热性(塑料组件)检测:技术突破与产业赋能
随着工业4.0进程加速,塑料组件在汽车、电子、航空航天等高温场景的应用比例显著提升。据中国塑料加工工业协会2024年报告显示,耐高温塑料市场规模已达320亿美元,年复合增长率达8.7%。然而,塑料材料在高温环境下易发生软化、蠕变、分解等问题,导致产品失效风险。在此背景下,耐热性(塑料组件)检测成为保障产品可靠性的关键环节,其核心价值体现在降低质量事故率、优化材料选型及延长产品寿命周期三个方面。通过精准的热稳定性评估,企业可减少因热失效导致的召回损失,据德国莱茵TÜV统计,2023年完善耐热检测体系的企业平均质保成本降低23%。
热性能检测技术原理与创新
耐热性检测以热力学分析为核心,涵盖热变形温度(HDT)、维卡软化点(VST)、热失重分析(TGA)等关键指标。以ASTM D648标准为例,通过三点弯曲法在1.82MPa载荷下测定材料变形量达0.25mm时的温度阈值。近年发展的动态热机械分析(DMTA)技术可同步监测储能模量、损耗因子等动态参数,据中国科学院化学研究所2024年研究,该技术对交联型塑料的热稳定性评估精度提升40%。基于机器学习的预测模型正推动检测智能化,通过历史数据训练可预测新型复合材料的耐热行为。
全流程检测实施体系构建
规范化的检测流程包含五个阶段:首先依据ISO 75-2标准进行样品预处理,在(23±2)℃、50%RH环境平衡48小时;其次采用热流型DSC设备进行玻璃化转变温度测定;第三阶段执行阶梯式升温试验,以5℃/min速率从室温升至300℃;第四步通过三维形貌扫描仪量化表面形变;最终结合有限元分析模拟实际工况。某新能源汽车企业在电池支架检测中采用此流程,成功将热变形临界温度检测误差控制在±1.5℃以内。
行业应用场景与效益分析
在汽车发动机舱部件检测中,高温环境下塑料性能检测技术展现显著价值。某德系车企对PA66-GF35材质的进气歧管进行150℃/2000h持续热老化测试,通过傅里叶红外光谱(FTIR)发现分子链断裂阈值,据此优化了玻纤含量配比,使部件耐热寿命延长30%。电子电器领域则聚焦连接器端子应用,华为2023年导入热变形温度测试方法后,5G基站外壳在85℃环境下的尺寸稳定性达到IEC 62137-1 Class 5要求。
标准化质量保障体系演进
行业正构建四级质量保障机制:实验室通过ISO/IEC 17025认证确保检测能力;设备定期进行NIST溯源校准;建立包含287项参数的塑料热性能数据库;实施盲样比对与能力验证计划。SGS集团2024年实验室间比对数据显示,热变形温度测试的实验室间偏差已从2019年的±4.2℃压缩至±1.8℃。区块链技术的引入使检测数据不可篡改性达到99.99%,显著提升结果公信力。
展望未来,建议从三方面深化发展:首先建立跨行业的热-力-化多场耦合检测标准,应对复杂工况需求;其次开发基于数字孪生的虚拟检测系统,实现全生命周期热管理;最后加强生物基耐高温材料的评价体系研究,推动绿色制造转型。随着检测精度突破0.5℃量级,塑料组件的热可靠性将支撑更多前沿领域的创新应用。
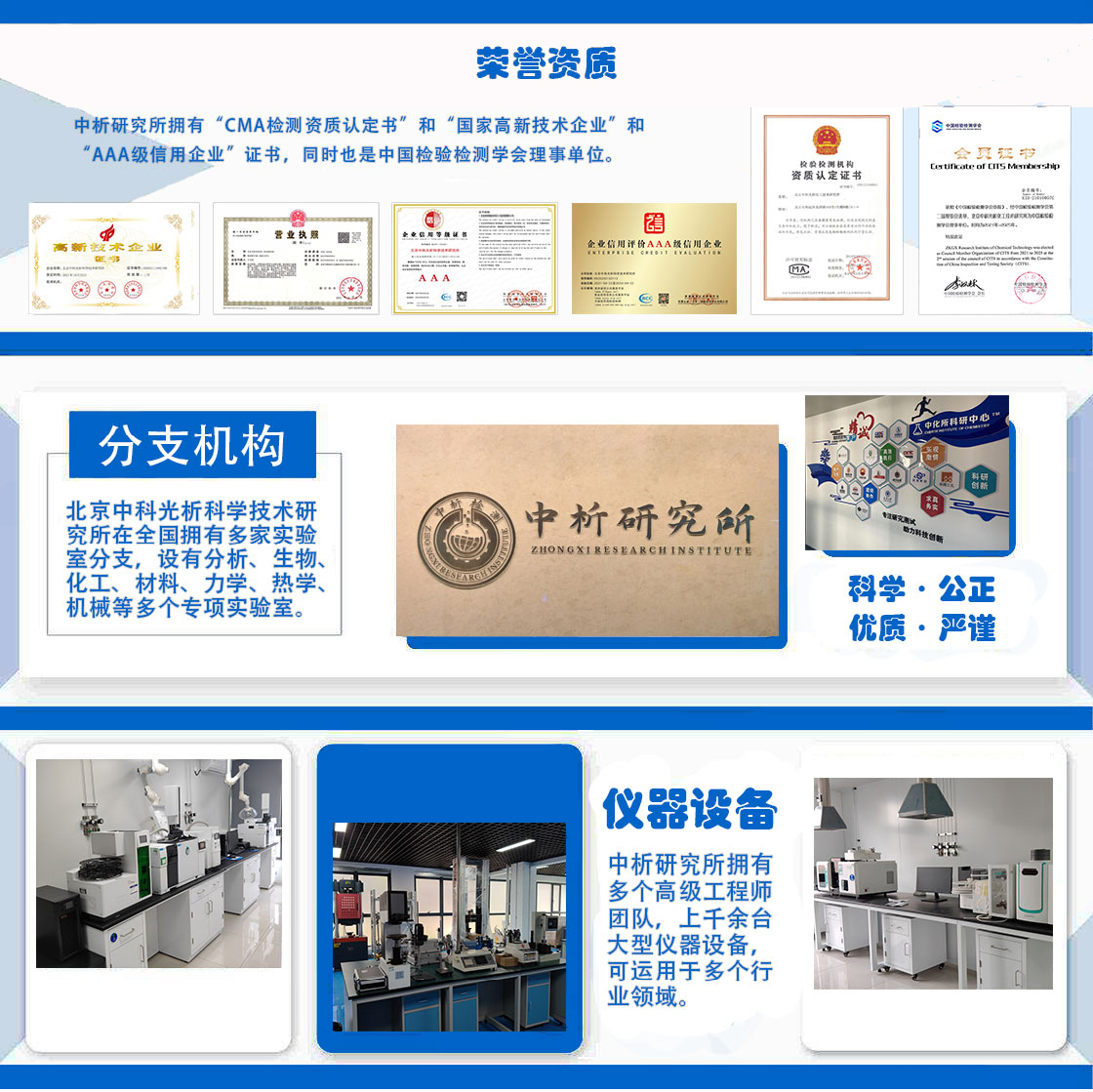
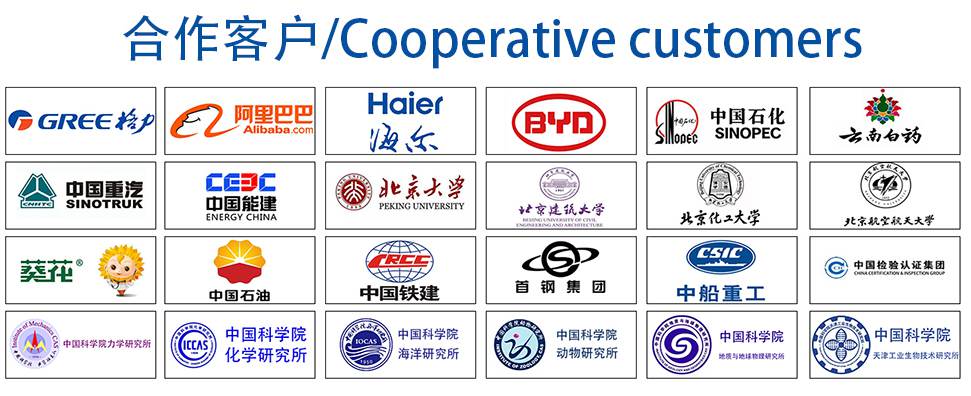