漆膜划圈试验检测的技术发展与行业应用
随着工业涂料在汽车制造、航空航天、建筑装饰等领域的广泛应用,涂层附着力成为衡量产品质量的核心指标。据中国涂料工业协会2024年报告显示,我国工业涂料市场规模已达4200亿元,其中因涂层脱落导致的质保纠纷占比达17.3%。漆膜划圈试验作为国际通用的附着力检测方法,通过标准化评估涂层与基材的粘结强度,为产品质量控制提供关键数据支撑。该项目不仅可验证涂料配方的合理性,更能优化涂装工艺参数,降低产品使用周期内的维护成本。尤其在新能源汽车电池壳体防护、海洋装备防腐涂层等关键领域,其检测结果直接关系到设备安全性与使用寿命,具有显著的经济效益和社会价值。
漆膜划圈试验的技术原理与实现路径
该检测基于机械划伤原理,采用特制划格刀具在漆膜表面形成交叉网格划痕。根据ASTM D2197标准,刀具以固定压力(通常为750g±10g)在10秒内完成6×6的等距划痕,划痕间距依据涂层厚度设置为1-3mm不等。通过观察划痕交叉处漆膜脱落面积的比例,按ISO 2409分级标准判定附着力等级。相较传统拉开法,划圈法的优势在于可直观反映涂层抗剪切破坏能力,且对曲面、异形件等复杂基材具有更好的适用性。
标准化检测流程与质量控制要点
实施流程涵盖样品预处理、环境调控、设备校准三大环节。首先需在温度23±2℃、湿度50±5%RH的恒温恒湿箱中养护试样48小时,消除环境应力的影响。检测时使用经计量认证的电动划格仪,刀具角度保持30°±1°,行进速度控制在20mm/s。某第三方检测机构的实践表明,引入机器视觉系统后,脱落面积计算的误差率从人工判读的12%降至2.3%。关键质控点包括刀具磨损度监测(每50次检测更换刀头)和压力传感器校准(每季度标定一次)。
典型行业应用场景与效益分析
在轨道交通领域,中车集团将划圈试验纳入动车组涂装工艺标准。通过对环氧底漆-聚氨酯面漆体系的系统检测,将涂层附着力等级从2级提升至1级(最高等级),使车体涂层耐盐雾性能延长至3000小时。某新能源汽车企业应用改进型划圈法,结合高低温循环试验(-40℃至85℃),将电池托盘涂层的附着力稳定性提高40%,有效预防电解液渗透风险。据国家材料服役安全科学中心测算,规范化的划圈检测可使工业涂装综合成本降低8-12%。
质量保障体系的构建与创新
行业领先机构已建立三维质量保障模型:设备层面采用激光干涉仪校准划痕精度(误差≤0.02mm);操作层面开发智能压力反馈系统,实时监控划痕深度波动;数据层面构建区块链存证平台,确保检测结果不可篡改。某外资涂料企业的实践显示,通过集成物联网技术的自动划圈检测线,单次检测周期缩短70%,数据可追溯率达到100%。
展望未来,建议从三方面深化技术创新:一是开发适用于超薄涂层(<20μm)的显微划痕检测模块;二是建立基于大数据分析的涂层失效预警模型;三是完善极端环境(如深海高压、太空辐照)下的附着力评价体系。随着智能传感技术与材料计算科学的融合发展,漆膜划圈试验将向高精度、自动化、场景自适应方向持续进化,为涂层材料的全生命周期管理提供更强大的技术支撑。
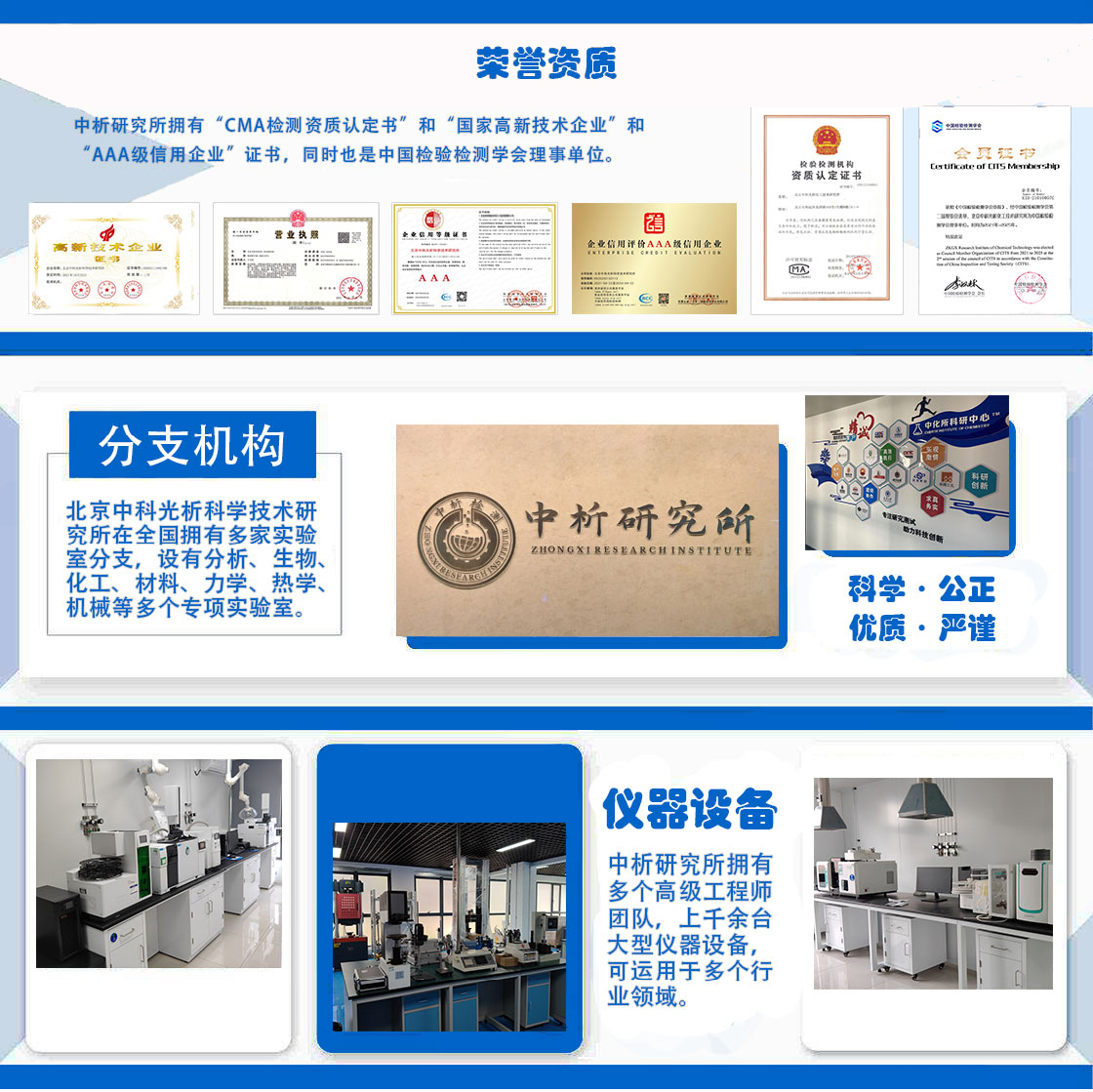
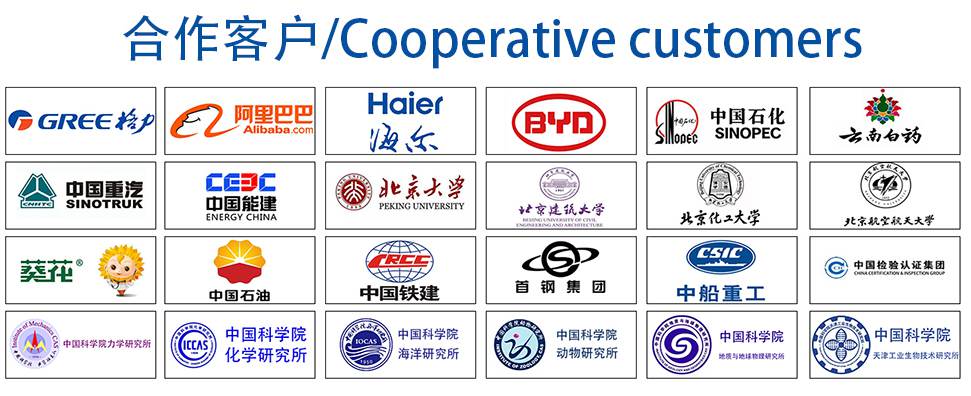