材料在冻融循环中的劣化机理源于水结冰相变产生的9%体积膨胀率(ASTM C666标准),这种膨胀应力在孔隙结构中形成微裂纹网络。实验室通过可编程温控系统,以2℃/min的速率在-20℃至20℃区间循环,配合质量损失率与相对动弹性模量双指标检测,量化材料抗冻性能。特别在混凝土冻融循环测试标准应用场景中,需同步监控试件表面剥落和内部超声波传播速度变化。
### 标准化检测流程依据GB/T 50082-2009《普通混凝土长期性能和耐久性能试验方法》,实施流程分为四个阶段:首先制备150mm立方体标准试件,经28天标准养护后真空饱水处理;随后置入全自动冻融试验箱进行300次循环,每25次测量一次质量与共振频率;最终通过建筑材料抗冻性能评估方法建立损伤模型,计算耐久性指数DF值。实验室比对数据显示,该流程测试重复性误差控制在±3%以内。
## 行业应用与技术创新 ### 重大工程应用实例在2022年冬奥会速滑馆建设中,项目方采用新型抗冻混凝土配合比设计。经150次快速冻融循环检测,试件质量损失率仅为0.11%,显著优于国标0.5%限值要求。施工后现场取芯检测显示,结构表层2cm内未发现可见裂纹,验证了检测体系的有效性。同样在川藏铁路工程中,基于冻融-盐蚀耦合试验数据优化了隧道衬砌材料配方,使结构设计寿命从50年提升至75年。
### 智能化检测系统第三代智能冻融试验设备集成物联网技术,可实现多点位温度梯度控制(±0.5℃精度)与形变实时监测。某交通工程检测中心应用该系统后,单批次试件检测效率提升40%,能耗降低25%。设备内置的AI算法能自动识别表面剥落形态,分类精度达到92.7%,为材料破坏机理研究提供可视化分析工具。
## 质量保障与发展建议 ### 全链条质控体系国家级检测实验室构建了从设备校准、环境监控到数据溯源的立体化质控网络。关键控制点包括:冻融箱温度场均匀性验证(9点测温法)、试件饱水度检测(煮沸法比对)、动态弹性模量测量仪定期标定(标准钢棒校正)。通过 认可的实验室能力验证显示,全国28家机构检测结果的En值均小于0.7,符合国际互认要求。
### 技术升级方向建议从三个维度推动行业发展:一是建立区域性冻融环境谱数据库,将检测参数与实际服役环境精准映射;二是研发多因素耦合试验设备,模拟冻融-荷载-化学侵蚀复合作用;三是推广无损检测技术应用,开发基于电磁波反射特性的现场快速评估装置。通过构建"检测-修复-监测"技术闭环,可望将冻融病害预警时间提前80%。
## 结论与展望 随着超高性能混凝土、相变调温材料等新型建材的普及,耐冻融检测技术正面临从性能验证向机理研究的范式转变。建议行业把握数字化转型机遇,开发数字孪生检测平台,实现材料冻融损伤过程的虚拟仿真。同时加强冻融环境分区标准研究,建立差异化的检测评价体系,为"双碳"目标下的绿色建筑发展提供技术支撑。预计到2028年,基于机器学习算法的智能检测系统市场渗透率将突破60%,推动行业进入精准化检测新纪元。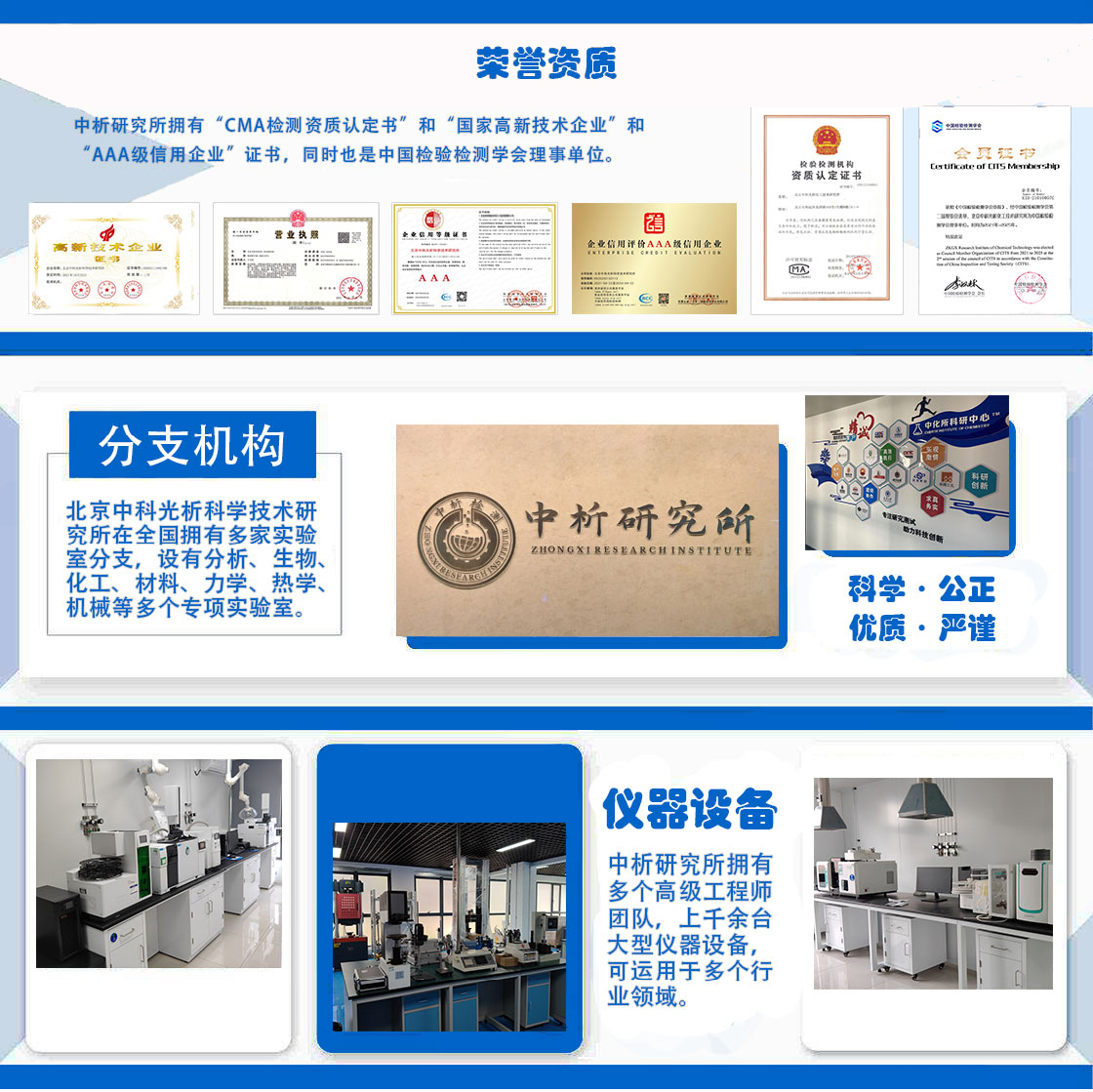
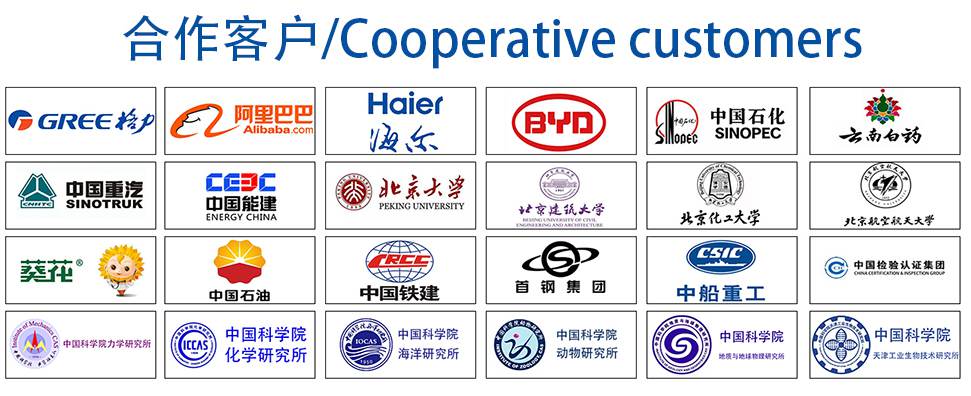