烧损深度检测技术及核心检测项目分析
一、烧损深度的定义与检测意义
- 设备寿命评估:判断关键部件(如锅炉管道、涡轮叶片)的剩余使用寿命。
- 安全性保障:预防因材料失效引发的泄漏、断裂等事故。
- 工艺流程优化:通过损伤数据分析改进生产工艺。
二、核心检测项目分类
1. 高温氧化层厚度检测
- 适用场景:冶金、电力行业的锅炉、燃气轮机部件。
- 检测参数:
- 氧化层厚度(μm级精度)。
- 氧化层与基体材料的结合强度。
- 氧化产物成分分析(如FeO、Fe₃O₄比例)。
2. 机械摩擦烧蚀深度检测
- 适用场景:汽车发动机活塞环、制动系统。
- 检测参数:
- 表面烧蚀凹坑深度(0.1–2 mm范围)。
- 烧蚀区域硬度变化。
- 微观裂纹扩展长度。
3. 化学腐蚀烧损检测
- 适用场景:化工设备、海洋工程结构。
- 检测参数:
- 腐蚀坑深度及分布密度。
- 腐蚀产物厚度(如锈层)。
- 基体材料元素流失量(通过EDS能谱分析)。
4. 电弧烧损检测
- 适用场景:电力开关触点、输电线路。
- 检测参数:
- 电弧烧蚀坑的熔融深度。
- 烧损区域的导电性变化。
- 碳化层厚度及绝缘性能。
三、检测技术及设备
1. 无损检测技术
- 超声波测厚法:利用高频声波反射测量氧化层厚度,精度±0.01 mm。
- 涡流检测:适用于导电材料的近表面缺陷检测(深度<5 mm)。
- 激光共聚焦显微镜:三维形貌重建,分辨率达纳米级。
2. 微损/有损检测技术
- 金相切片法:通过切割、抛光、腐蚀后观察截面,精度最高但破坏样品。
- 显微硬度计:测量烧损区与基体的硬度梯度,间接评估损伤深度。
3. 智能化检测方案
- AI图像分析:结合工业相机与机器学习算法,实现烧损区域的自动识别与深度计算。
- 红外热成像:通过温度场分布推测内部烧蚀结构。
四、检测流程标准化
- 预处理阶段:
- 清洗表面油污及松散氧化物。
- 选择代表性检测区域(如焊缝、应力集中区)。
- 数据采集:
- 采用多技术融合(如超声+金相)提高准确性。
- 数据分析:
- 建立烧损深度与使用时间的回归模型。
- 结果判定:
- 依据行业标准(如ASTM E3-11、ISO 18516)评估是否需维修或更换。
五、典型应用案例
- 航空航天领域:某型发动机涡轮叶片服役后,通过激光扫描发现烧蚀深度超限(>0.3 mm),触发提前更换预警。
- 石化行业:加氢反应器内壁经10年运行,金相分析显示基体腐蚀深度达1.2 mm,指导设备降级使用。
六、技术挑战与发展趋势
- 挑战:复杂曲面检测适应性差、多层材料界面区分困难。
- 趋势:
- 多模态传感器融合技术。
- 在线实时监测系统集成。
- 基于大数据的剩余寿命预测模型。
上一篇:聚苯板的尺寸稳定性检测下一篇:燃烧性能等级检测
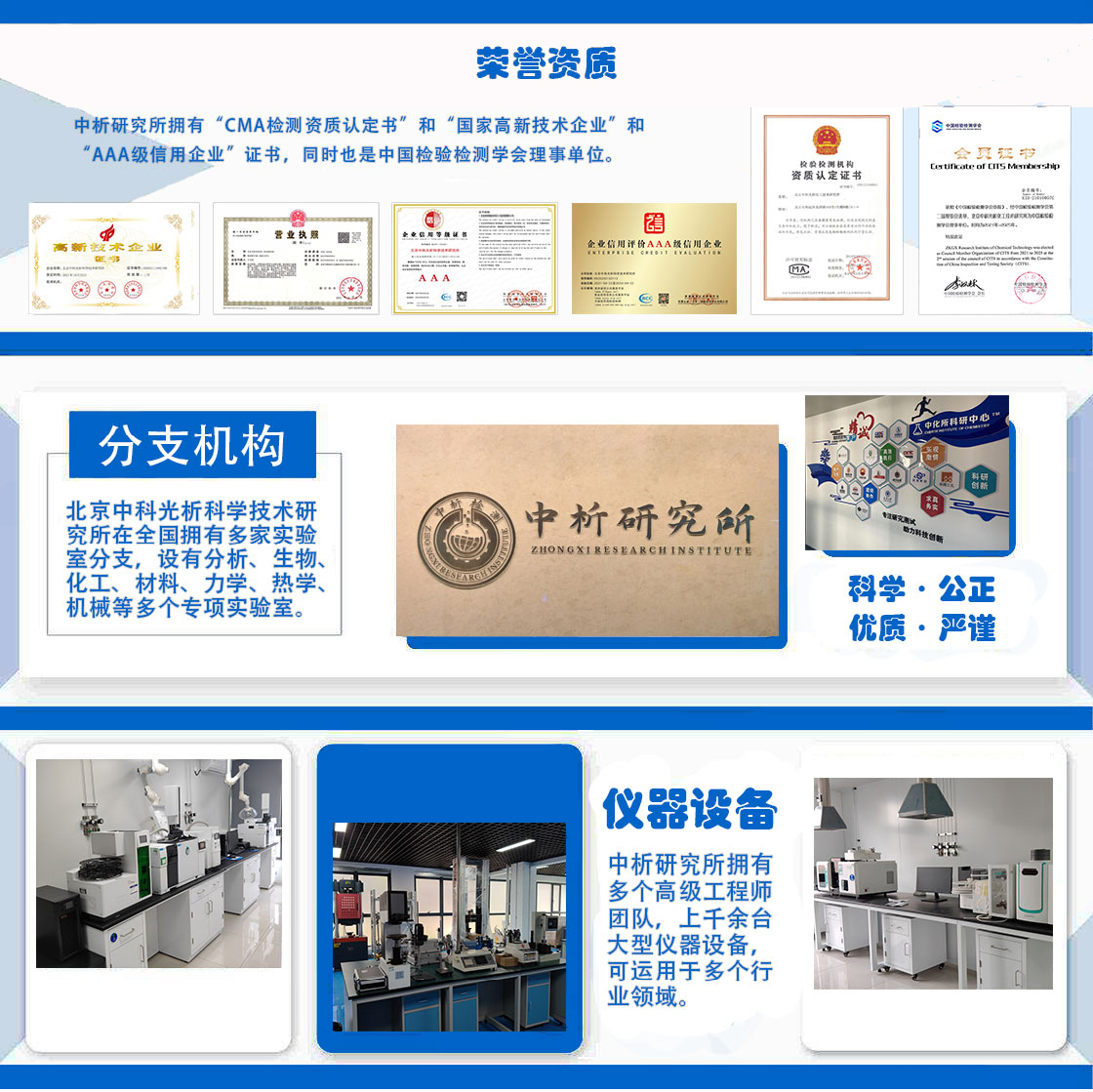
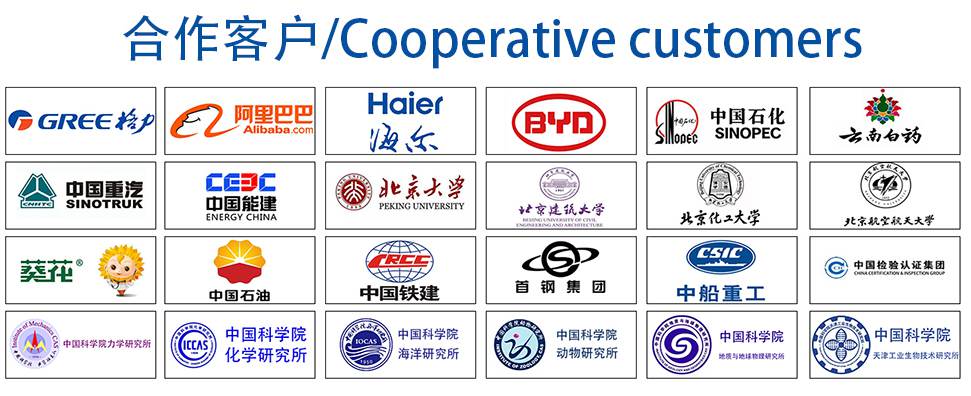
材料实验室
热门检测
11
14
12
15
18
15
13
12
13
16
18
16
15
16
11
14
22
17
18
17
推荐检测
联系电话
400-635-0567