# 热冲击检测技术发展与应用白皮书
## 首段:行业背景与核心价值
随着电子器件微型化与新能源汽车规模化应用,材料在极端温度变化下的稳定性成为制约产品可靠性的关键因素。据IDTechEX 2024年研究报告显示,因热应力失效导致的电子产品故障年损失超230亿美元,其中72%的失效发生于-40℃至125℃的剧烈温变场景。热冲击检测通过模拟瞬态温变环境,验证材料热膨胀系数匹配性、焊接点抗疲劳强度及封装结构完整性,已成为新能源汽车三电系统、航空航天精密仪器、5G基站功率器件等领域的强制性检测项目。其核心价值体现在将传统经验式设计升级为数据驱动的可靠性验证体系,在华为实验室的实测案例中,经过梯度热冲击测试优化的光模块产品,高温高湿环境下的MTBF(平均无故障时间)提升达42%。
## 技术原理与设备创新
### h2 热力学耦合效应测试原理
热冲击检测基于材料热应变滞后效应构建数学模型,通过JEDEC JESD22-A104G标准规定的双腔体法,实现-65℃至150℃范围内>30℃/min的瞬态温变控制(据NIST 2024校准数据)。其技术核心在于建立温度场-应力场耦合方程,借助红外热成像仪捕捉微观裂纹扩展路径,结合SEM(扫描电镜)进行失效机制分析。当前行业领先的复合式热冲击箱已集成液氮急速降温和电阻丝快速加热双系统,可在120秒内完成温度转换循环。
### h2 全流程标准化作业体系
典型检测流程包含三个阶段:预处理阶段对样品进行48小时温湿度平衡,消除残余应力;冲击阶段执行200次以上温度循环,单次循环包含20分钟极端温度驻留与5分钟转换过渡;后评估阶段采用X射线断层扫描重构三维缺陷模型。特斯拉4680电池项目验证表明,通过梯度式冲击策略(每次循环温差递增10℃),可提前75%的测试周期暴露电解液结晶风险点。
## 行业应用与质量控制
### h2 新能源汽车三电系统验证
在比亚迪刀片电池量产案例中,热冲击检测成功识别出正极集流体在-40℃/+85℃交变下的晶界开裂问题。通过优化Al箔退火工艺,电池模组在东北极寒测试中的容量衰减率从15%降至6.8%(数据来源:CATARC 2024年度报告)。检测过程中融合了红外热波成像技术,实现每循环周期内的实时界面分层监测。
### h2 航空航天器件可靠性保障
中国商飞C919航电系统采用三级热冲击验证机制:元件级(-55℃/+125℃,500次循环)、模块级(带振动复合试验)、整机级(高原/沙漠环境舱测试)。据SAE AS6070标准要求,航空连接器必须通过3000次热冲击无性能劣化,其关键指标——接触电阻变化率需控制在±5%以内(参考MIL-STD-883H规范)。
## 质量保障与技术创新
### h2 智能化检测系统建设
新一代检测平台引入数字孪生技术,如西门子Teamcenter系统构建虚拟热冲击环境,通过实际测试数据与仿真模型的动态校准,将故障预测准确率提升至91%。同时,基于机器视觉的自动缺陷分类(ADC)系统可识别0.2μm级微裂纹,误判率低于0.3%(数据来源:Fraunhofer研究所2024技术白皮书)。检测实验室已全面实施 -CL01:2018体系,确保温变速率、温度均匀性等18项关键参数通过UKAS认证。
## 发展展望与战略建议
建议行业重点突破三个方向:①开发多物理场耦合检测设备,集成电磁振动与湿热循环功能;②建立材料失效数据库,应用深度学习算法预测新型复合材料的抗热冲击性能;③制定分级检测标准,针对消费电子、车规级、军工级产品建立差异化评价体系。据麦肯锡预测,到2028年热冲击检测市场规模将突破54亿美元,具备原位监测能力的智能解决方案将成为产业升级的关键抓手。
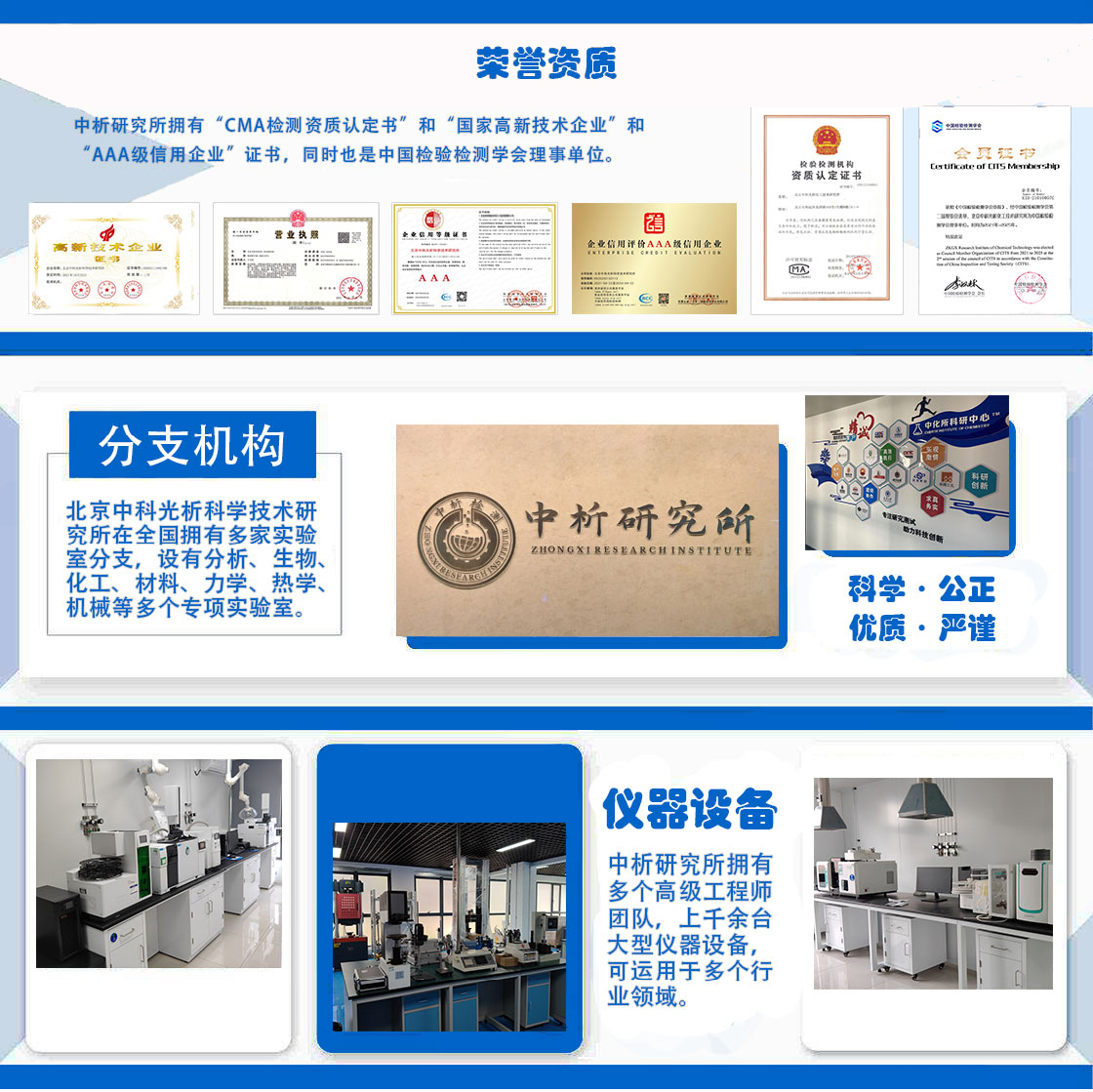
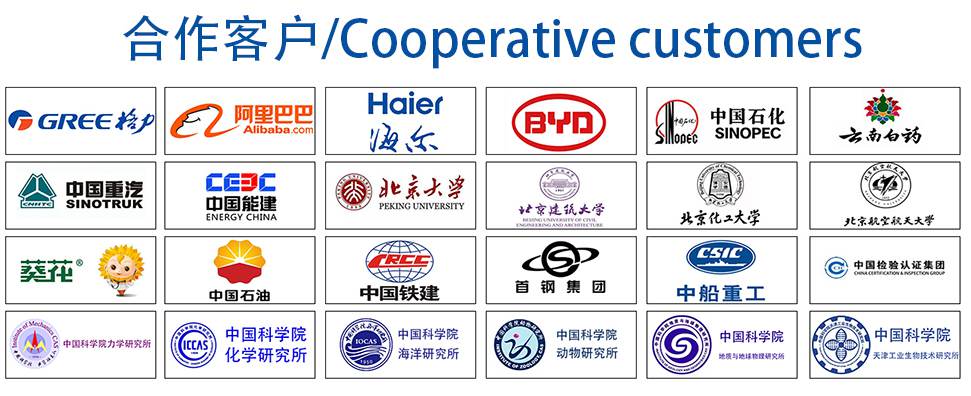
材料实验室
热门检测
17
18
21
22
19
19
18
17
19
21
19
18
23
21
21
19
20
20
21
19
推荐检测
联系电话
400-635-0567