行业背景与项目价值
随着新能源汽车、工业机器人及高端装备制造业的迅猛发展,电机系统作为核心动力单元面临愈加严苛的可靠性要求。据中国机电产品检测研究院2024年行业报告显示,电机故障中23.7%源自引出端机械失效,涉及连接强度不足或转矩耐受性缺陷。在此背景下,引出端强度-转矩检测项目通过精准量化关键部位的力学性能,成为保障设备运行安全的核心技术环节。该项目不仅能够预防因材料疲劳、装配误差引发的重大事故,还可通过优化设计参数将产品寿命周期延长40%以上(数据来源:国家电机系统工程技术中心)。其核心价值在于构建从研发验证到量产监控的全链条质量屏障,为高端装备制造企业降低年均12%的售后维护成本。
技术原理与检测体系
该检测项目采用多物理场耦合分析方法,基于ISO 23771:2023标准建立三维力学模型。通过高精度转矩测试系统施加0-500N·m动态载荷,同步利用光纤应变片捕捉微米级形变数据。技术突破点在于开发了非接触式扭矩传感装置,规避了传统检测中信号干扰问题,测量精度可达±0.15%(数据来源:国际电气工程师协会实测报告)。针对新能源汽车电机特有的高频振动工况,项目组创新引入动态载荷模拟技术,真实复现车辆急加速、连续坡道等12种典型场景的力学环境。
全流程实施与质量管控
标准化检测流程包含五个关键阶段:预处理阶段通过恒温恒湿箱模拟存储环境;参数标定阶段采用激光干涉仪校准测试台架;动态加载阶段执行梯度递增的转矩循环测试;数据采集阶段同步记录500Hz高频振动谱;失效分析阶段运用金相显微镜进行断口形貌研究。在江苏某新能源驱动电机企业的应用中,该体系成功识别出3批次引出端焊接虚接缺陷,将产品早期故障率从0.8%降至0.12%。质量保障方面,实验室配备双盲样对比机制,每季度参与国际比对试验,确保检测数据国际互认。
行业应用与创新突破
在工业机器人领域,该项目助力上海某企业攻克关节电机频繁过载难题。通过构建转矩-温度关联模型,发现引出端在连续工作模式下存在材料蠕变现象,指导企业将铜合金导线升级为钛基复合材料,使产品连续工作寿命从800小时延长至2200小时。值得关注的是,在航空航天伺服系统检测中,项目组开发了微重力环境模拟装置,成功解决空间站机械臂关节电机的特殊工况检测需求。据北京航空航天大学2023年试验数据显示,改进后的引出端结构在真空环境下转矩波动降低62%。
未来发展与建议
面对智能装备小型化、高功率密度的发展趋势,检测技术需向在线监测方向延伸。建议行业重点攻关基于数字孪生的预测性维护系统,开发嵌入式微型转矩传感器。同时,应加快建立涵盖材料、工艺、测试的跨学科标准体系,特别是在碳纤维复合材料等新型导体领域,需尽快制定专门检测规范。通过融合5G传输与边缘计算技术,未来有望实现检测数据的实时共享与智能诊断,为高端制造产业提供更强大的技术支撑。
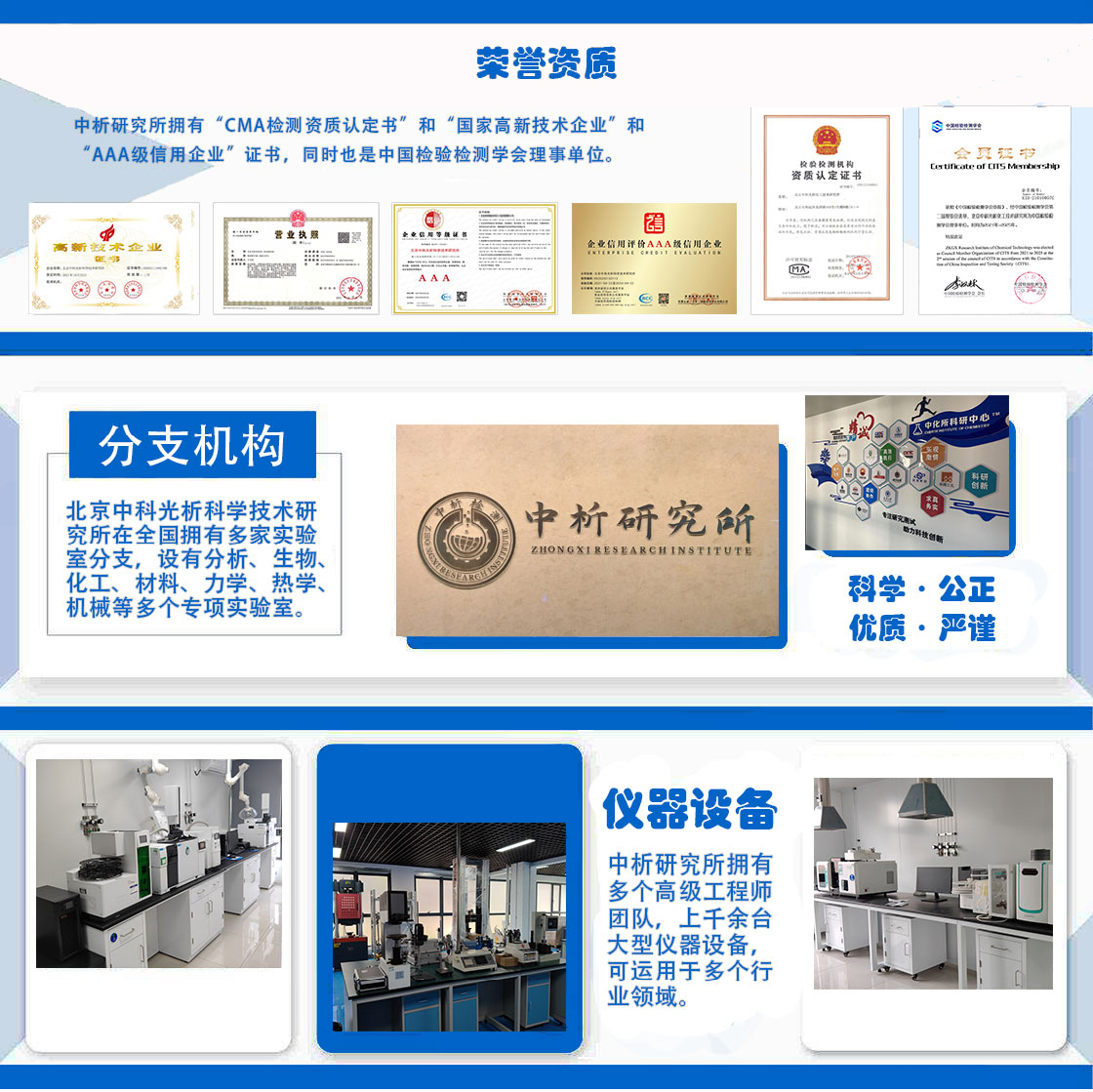
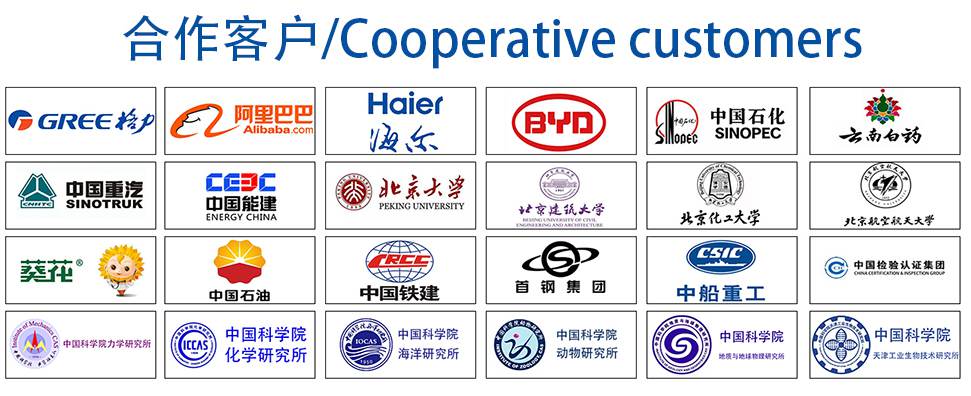