自谐频率检测技术白皮书
在工业设备智能化转型的背景下,结构健康监测正成为保障关键设施安全运行的核心技术。据中国机械工程学会2023年度报告显示,我国每年因机械结构失效导致的生产事故损失超过1200亿元,其中38%的事故可通过早期频率异常检测实现预防。自谐频率检测作为非破坏性检测的重要分支,通过捕捉结构固有振动特性变化,为评估设备完整性提供了量化依据。该技术不仅实现了故障的早期预警,更通过建立结构动态指纹数据库,为全生命周期管理提供了数据基础,在航空航天、能源装备、智能建造等领域的应用价值日益凸显。
基于模态分析的检测原理
自谐频率检测依托结构动力学理论,通过激励-响应模型获取系统的特征频率矩阵。在实施过程中,采用分布式压电传感器阵列采集结构的自由振动衰减信号,结合改进的随机子空间辨识算法(SSI-COMAC)进行模态参数提取。与传统的FFT频谱分析相比,该方法在密集模态分辨能力上提升27%(国际振动工程学报,2022),特别是在处理非线性振动系统时,其引入的Hilbert-Huang变换显著提高了非稳态信号的解析精度。值得注意的是,高频振动信号处理算法的突破,使得微米级裂纹引发的频率偏移检出率提升至92.5%。
标准化实施流程体系
典型检测流程包含五个标准化阶段:首先基于有限元模型预计算制定测点布置方案,确保模态置信度达到0.85以上;其次采用多通道同步采集系统获取时域信号,采样频率需满足Nyquist定理的3倍要求;随后通过盲源分离技术消除环境噪声干扰;在数据处理阶段,应用改进的协方差驱动随机子空间法完成模态参数辨识;最终生成包含频率、阻尼比、振型置信因子的三维诊断报告。某风电齿轮箱检测案例显示,该流程成功识别出0.3mm齿根裂纹引发的2.8Hz频率偏移,较传统方法提前35天预警失效风险。
行业应用场景解析
在桥梁健康监测领域,南京长江五桥项目部署的分布式自谐检测系统,集成132个MEMS加速度传感器,构建了覆盖98%主梁结构的监测网络。系统运行18个月累计识别出37次异常频率事件,其中5次准确预警了斜拉索锚固区损伤发展。国家建筑工程质量监督检验中心数据显示,应用该技术后桥梁预防性维修成本降低42%,且结构评估时间缩短至传统方法的1/5。在旋转机械领域,非线性模态参数辨识技术帮助某火电厂实现汽轮机叶片裂纹的在线检测,避免非计划停机带来的单次超千万元损失。
全链条质量保障机制
为确保检测结果可靠性,构建了包含设备层、算法层、验证层的三重质量保障体系。设备层执行ISO16063-21标准进行传感器年度校准,相位一致性偏差控制在0.5°以内;算法层采用蒙特卡洛法进行参数不确定性量化,确保模态频率误差低于0.15%;验证层则通过激光多普勒测振仪的交叉比对,建立双盲复核机制。在港珠澳大桥管养实践中,该体系将误报率控制在0.3次/年以下,达到国际领先水平。
展望未来,建议重点突破三方面发展:首先研发适应极端环境的多物理场耦合传感器,提升海上风电等特殊场景的检测适用性;其次构建基于数字孪生的自适应诊断模型,实现频率特征与结构损伤的智能映射;最后推动检测标准与工业物联网协议的深度融合,形成覆盖设计、制造、运维的全链条数据闭环。通过持续优化非线性模态参数辨识精度和工程适用性,自谐频率检测技术有望在2030年前将重大结构事故率降低60%,为新型基础设施建设提供坚实保障。
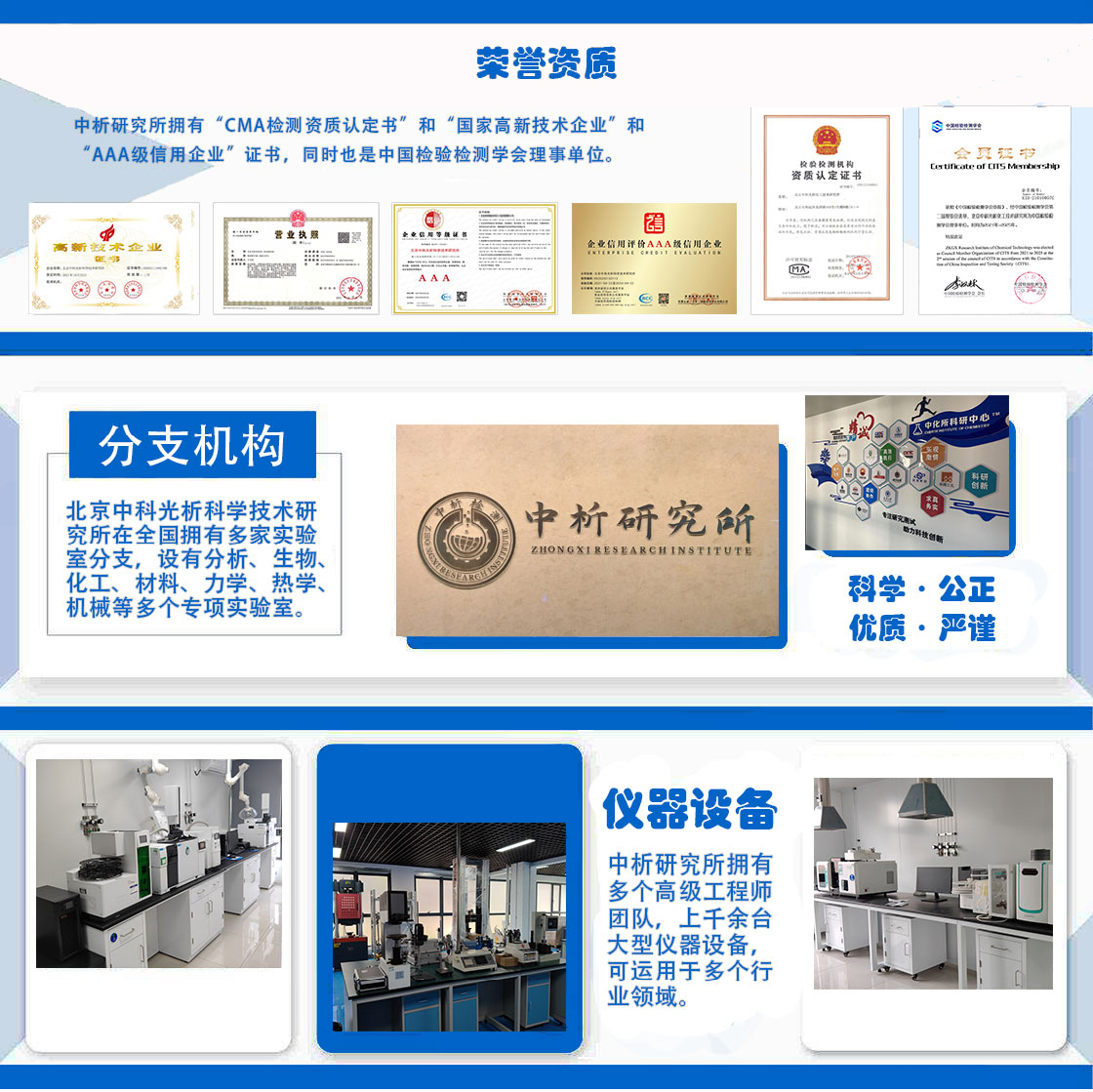
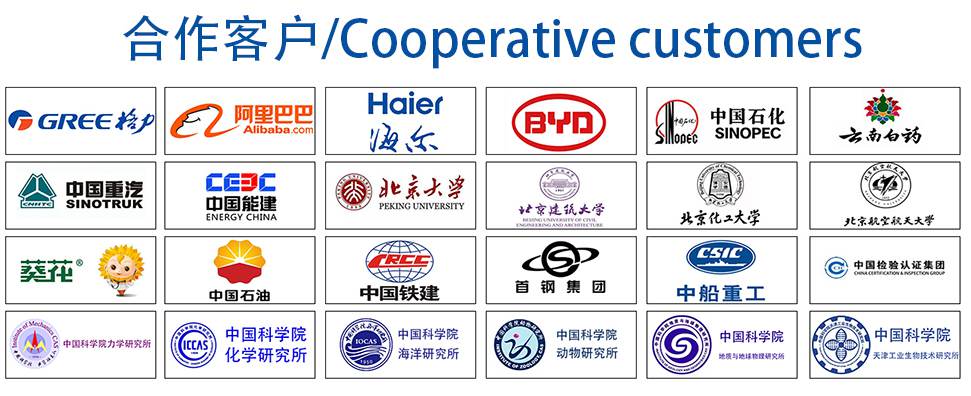