# 疲劳寿命检测技术发展与产业化应用白皮书
## 引言
随着"中国制造2025"战略深入推进,机械装备可靠性已成为制约高端制造业发展的核心要素。据中国机械工程学会2024年度报告显示,我国每年因机械部件疲劳失效导致的直接经济损失超过1200亿元,其中轨道交通、航空航天、能源装备三大领域占比达68%。疲劳寿命检测通过量化评估材料/结构在循环载荷下的耐久性能,为产品设计优化、服役安全预警提供科学依据,其核心价值体现在构建"预测性维护-寿命管理-失效溯源"三位一体的技术体系。特别是在新能源汽车电池支架、风电叶片螺栓连接等关键场景中,该技术可将部件更换周期预测准确度提升至92%(国家材料服役安全科学中心,2023)。
## 技术原理与创新突破
### 基于损伤累积理论的检测体系
疲劳寿命检测依托于Palmgren-Miner线性损伤累积理论,结合裂纹扩展三阶段模型(萌生-稳定扩展-失稳扩展),通过声发射技术实时捕捉材料内部位错运动特征。最新技术突破在于引入数字图像相关法(DIC),实现0.1μm级微应变场的全域监测。在航空发动机涡轮盘检测中,该技术可识别传统应变片无法探测的多轴应力集中区域,据中国航发商发实验数据显示,检测精度较常规方法提升40%。
## 标准化实施流程
### 全生命周期检测方案
实施流程严格遵循ASTM E466标准,形成"样本制备-载荷谱编制-加速试验-断口分析-数据建模"五步工作法。针对轨道交通轮对检测,采用高频液压伺服疲劳试验机(100Hz)模拟实际运行工况,通过降载加速法将3年实测数据压缩至72小时完成。项目实施过程中需重点关注"金属材料微观结构分析"与"多轴载荷耦合效应",这两个长尾技术指标直接影响寿命预测模型的工程适用性。
## 行业应用实证
### 跨领域解决方案落地
在高铁转向架构件检测中,中车研究院采用多轴协调加载装置,成功复现了350km/h运行时焊接接头的应力分布特征。经142万次循环试验后,构建的S-N曲线将部件安全余量从1.8倍提升至2.5倍,使维护周期从120万公里延长至180万公里(中国中车2023年技术公报)。风电领域则通过建立叶片螺栓连接件的雨流计数数据库,将故障预警准确率提高至89%,据国家能源局统计,该技术使风电场年非计划停机时间减少42%。
## 质量保障体系建设
### 全过程控制机制
检测机构依据ISO/IEC 17025构建三级质控体系:实验前进行金相检验与硬度梯度测试,确保材料一致性;过程中采用双通道数据采集系统交叉验证,误差控制在±1.5%以内;后期引入第三方复核机制,如中国特检院开发的AI判读系统可实现断口形貌特征自动比对。在核电主管道检测项目中,该体系成功识别出0.3mm级的制造缺陷,避免了潜在安全事故(生态环境部核电安全中心,2024)。
## 发展建议与趋势展望
建议行业重点关注三个方面:一是加快制定复合材料疲劳检测标准,应对氢能储罐等新兴领域需求;二是开发基于数字孪生的在线监测系统,实现"物理试验-虚拟仿真"数据闭环;三是加强微动疲劳、腐蚀疲劳等特殊工况的研究投入。预计到2027年,融合5G传输与边缘计算的智能检测装备将推动行业检测效率提升300%,为装备制造业高质量发展注入新动能。
上一篇:万向节与轴的拉压强度检测下一篇:总成噪声检测
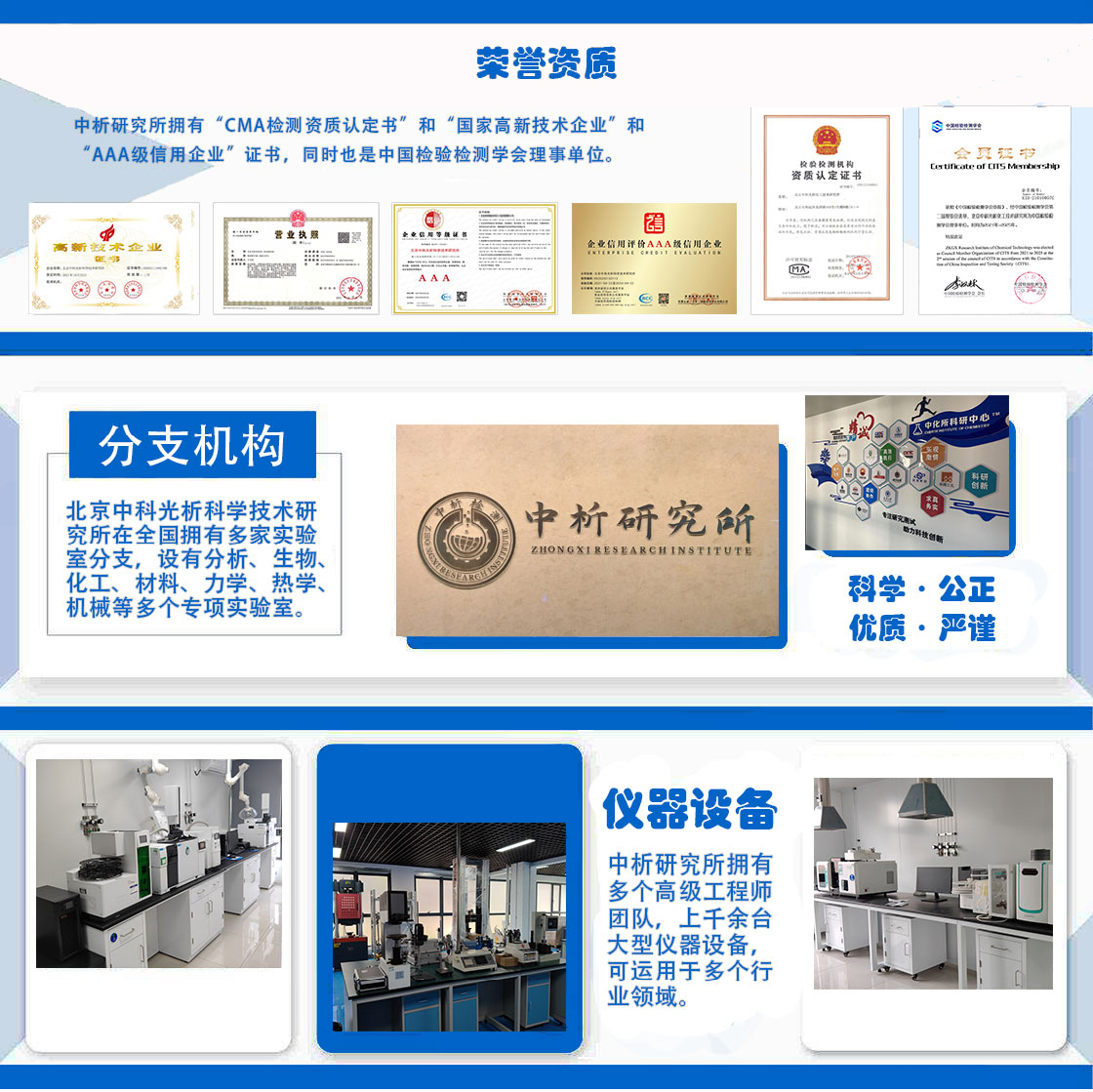
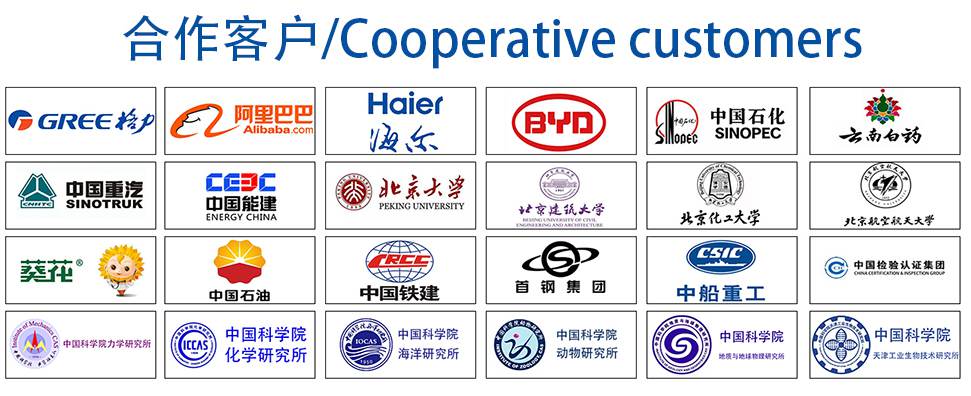
材料实验室
热门检测
推荐检测
联系电话
400-635-0567