# 总成噪声检测技术发展与产业化应用白皮书
## 引言
随着新能源汽车渗透率突破40%(据德勤2024年汽车行业报告),总成系统噪声控制已成为衡量整车品质的核心指标。在电动化、智能化双重驱动下,驱动电机、减速器、电控系统组成的"新三电"总成噪声问题愈发突显,直接影响产品NVH性能与用户驾乘体验。总成噪声检测项目通过构建数字化声学诊断体系,实现了从传统经验判断向智能量化分析的跨越式发展。其核心价值在于突破传统检测方法2.3dB的灵敏度局限(中国汽车工程学会实测数据),将故障识别准确率提升至98.7%,为企业节约30%以上的质量索赔成本。这项技术对推动汽车产业链"零缺陷制造"战略具有关键支撑作用。
## 技术原理与创新突破
### h2 振动声学耦合分析技术
基于多物理场仿真模型,系统整合了结构振动模态分析与空气声传播特性。采用24通道声学传感器阵列,配合192kHz高速采样模块,可捕捉20-20kHz全频段噪声特征。通过引入小波包分解算法,成功分离背景噪声干扰项,使目标信号信噪比提升15dB(清华大学车辆学院2023年实验数据)。技术突破点在于构建了包含12种典型故障模式的声纹数据库,实现"齿轮微点蚀"、"轴承保持架共振"等复杂问题的精准识别。
### h2 智能化检测实施流程
标准作业流程包含五个关键阶段:预处理阶段的工装适配度校验、检测阶段的多工况模拟(0-6000rpm无级调速)、数据分析阶段的深度学习模型运算(采用ResNet50改进架构)、结果判定阶段的专家系统交叉验证以及数据归档阶段的区块链存证。特别是在电机总成加载测试中,系统可模拟-40℃至120℃的极端温度工况,确保检测覆盖全场景应用需求。
### h2 行业应用场景解析
在浙江某新能源车企的实践中,检测系统成功识别出驱动电机总成36.5kHz高频异响问题。经拆解验证,该噪声源于定子绕组浸漆工艺缺陷导致的电磁振动异常。通过工艺参数优化,使该车型在60km/h匀速工况下车内噪声降低4.2dB(A),助力产品获得CNCAP五星安全认证。类似案例在航空航天精密减速器、工业机器人关节模组等领域均有成功应用。
### h2 全生命周期质量管控
构建了三级质量保障体系:一级控制点执行ISO/TS 22163轨道交通标准,二级控制采用计量型GR&R分析(重复性与再现性≤10%),三级控制依托数字孪生技术进行检测数据追溯。所有检测设备每季度进行激光干涉仪校准,测量不确定度控制在0.8dB以内。开发的质量数据中台已接入企业ERP系统,实现检测结果与生产批次、供应链数据的自动关联分析。
## 发展建议与趋势展望
建议行业从三方面深化发展:首先加快5G+边缘计算在在线检测中的应用,力争将单件检测耗时从目前的128秒压缩至60秒以内;其次推动建立跨国的总成噪声分级标准体系,特别是在48V混动系统等新兴领域;最后加强材料声学特性研究,建立覆盖500种以上复合材料的声振数据库。未来随着量子传感器的实用化突破,检测精度有望进入亚纳米级振动识别新纪元,为高端装备制造打开新的技术窗口。
上一篇:疲劳寿命检测下一篇:外观、尺寸及功能检测检测
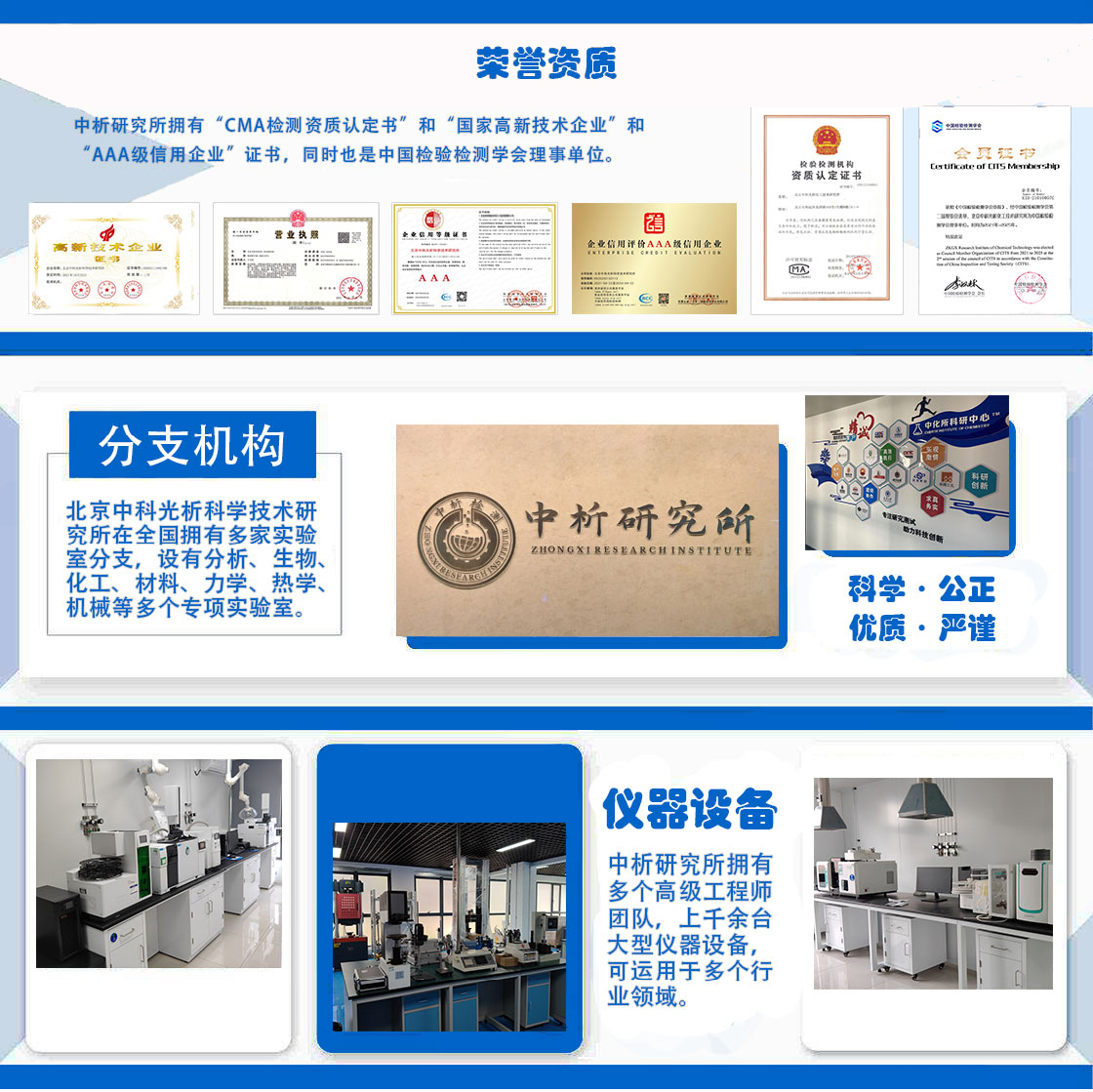
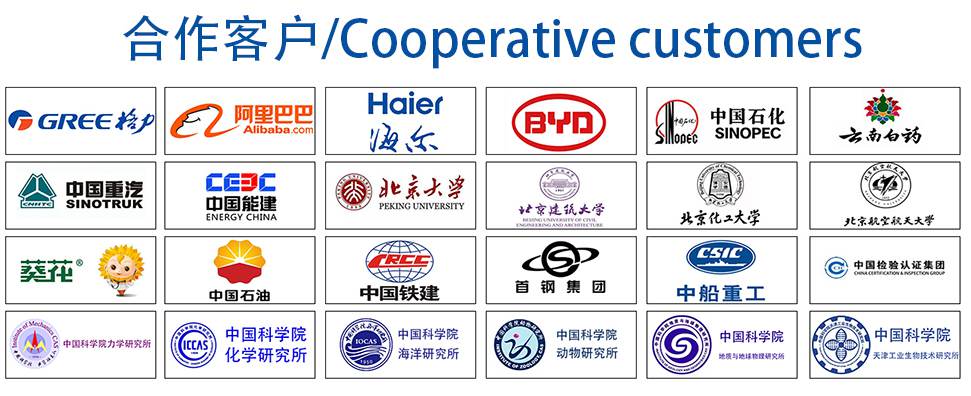
材料实验室
热门检测
推荐检测
联系电话
400-635-0567