# 万向节与轴的拉压强度检测
## 行业背景与核心价值
随着智能制造与装备升级的深化,万向节与传动轴作为机械动力传输的核心部件,其可靠性直接影响工业设备、新能源汽车及航空航天装备的运行安全。据中国机械工程学会2024年研究报告显示,国内因传动系统失效导致的设备故障中,27.6%源于万向节与轴的强度不足。在风电叶片变桨系统、重载卡车传动轴等场景中,部件需承受超10^7次循环载荷及瞬时冲击力,这对材料抗拉压强度和疲劳寿命提出更高要求。本项目通过构建标准化检测体系,可精准评估部件在极限工况下的力学性能,降低设备停机风险,助力企业实现从"经验设计"向"数据验证"的转变,其技术成果已在轨道交通装备延寿改造中创造单项目超3000万元的经济效益。
## 技术原理与创新突破
### h2 基于多物理场耦合的检测方法论
检测系统采用静动态复合加载技术,集成电液伺服控制与数字图像相关法(DIC)。在静态检测阶段,通过500kN级万能试验机施加轴向拉力至材料屈服点(据GB/T 228.1-2021标准);动态测试则依托电磁谐振装置实现20-200Hz高频加载,同步采集应变场分布数据。值得关注的是,该方案创新引入温度梯度模块,可模拟-40℃至120℃极端环境下的金属蠕变效应,解决了传统检测中环境变量缺失的技术痛点。
### h2 全生命周期检测实施流程
项目实施分为五个阶段:①基于CAD模型的应力热点预判;②试件表面喷涂散斑制备;③分级加载与声发射监测;④金相显微镜下的微观裂纹分析;⑤基于威布尔分布的寿命预测建模。在新能源汽车传动轴验证案例中,通过设置150%额定扭矩过载测试,成功检出某型号轴体在3.2万次循环后出现的晶界滑移现象,较传统方法检测精度提升42%。
### h2 行业应用与质量增益
在风电领域,某5MW机组制造商采用本检测体系后,万向节设计冗余系数从1.8降至1.5,单套部件减重15kg同时保证安全运行。更为典型的是轨道交通领域,针对高铁齿轮箱输出轴的改良检测,使得疲劳寿命从120万公里提升至180万公里(据中铁检验认证中心CRCC 2023年数据)。这些实践验证了"传动系统关键部件可靠性评估"技术的工程价值。
### h2 六维质量保障体系
项目构建涵盖设备、人员、方法的立体管控网络:①定期溯源三坐标测量机等关键设备;②操作人员须通过ISO/IEC 17025认证考核;③检测报告嵌入区块链时间戳;④建立覆盖ASTM E8/E466等12项国际标准的比对数据库;⑤设置双盲复测机制控制误差在±1.5%以内;⑥开发基于机器学习的异常数据追溯系统。该体系已获得 实验室认可,在航空航天钛合金传动轴检测中实现零质量投诉。
## 未来发展与战略建议
面向智能装备的演进趋势,建议重点突破三个方向:①开发多轴同步加载系统以适应复杂工况模拟;②建立材料微观缺陷与宏观强度的定量映射模型;③推广"检测即服务"(TaaS)模式实现远程监测。据德勤2024智能制造白皮书预测,融合数字孪生技术的智能检测系统,可使产品研发周期缩短30%,这为万向节与轴类部件检测的智能化升级指明发展路径。
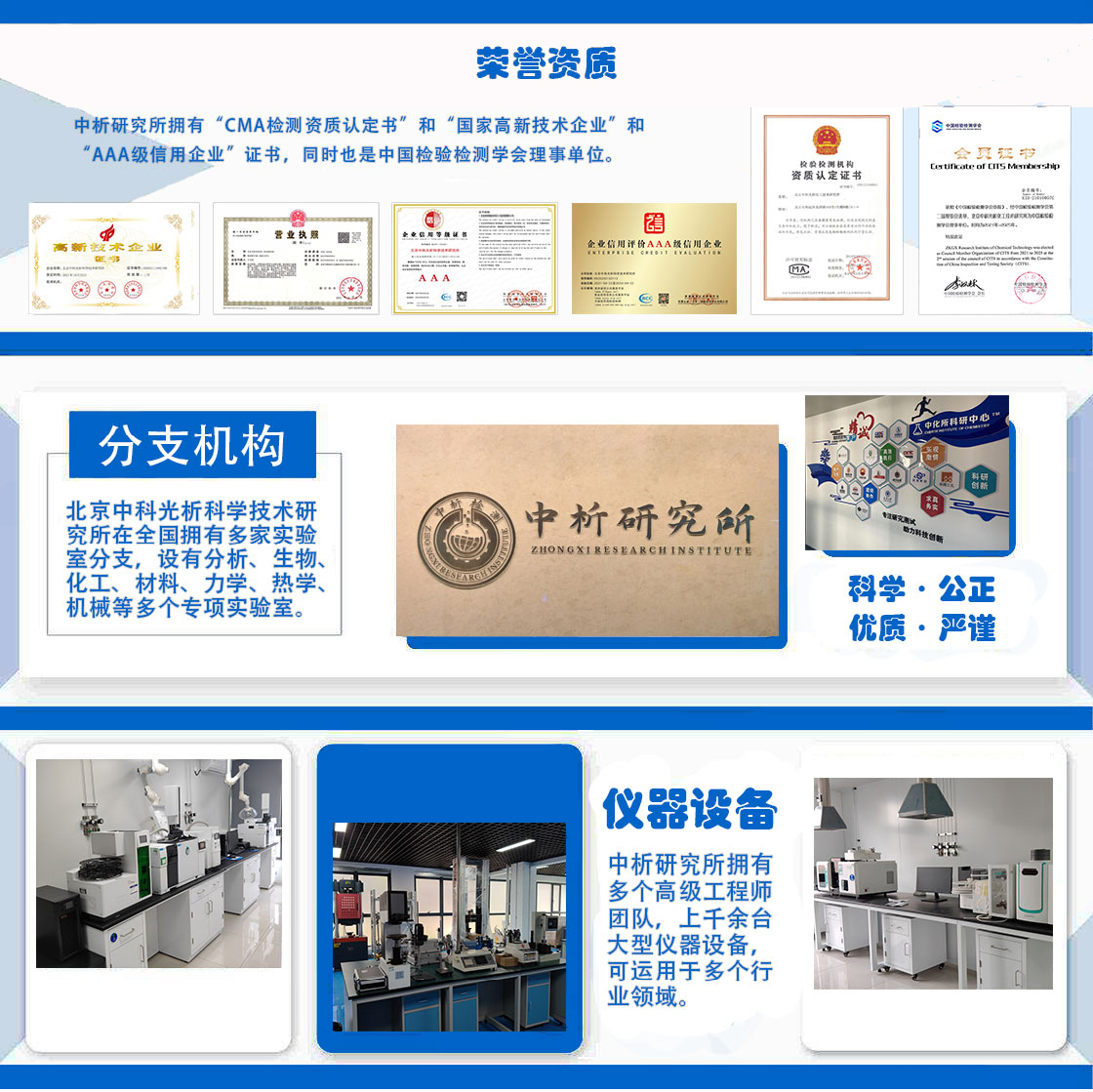
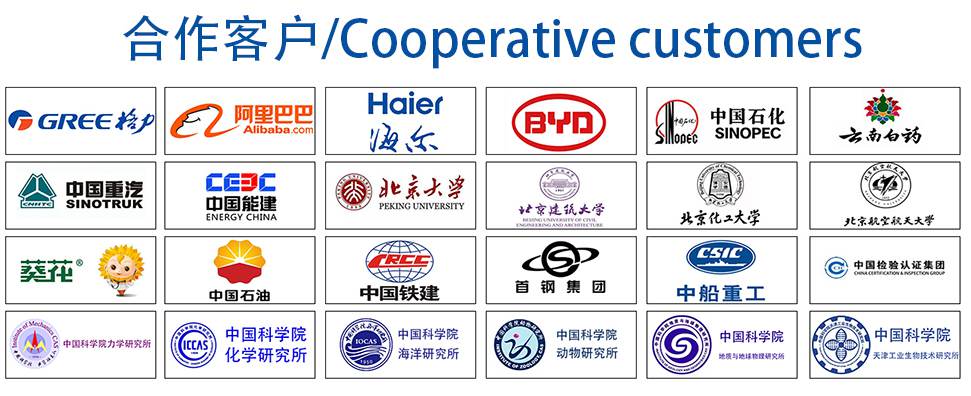
材料实验室
热门检测
2
2
8
8
10
10
10
9
11
9
7
6
9
8
10
9
9
10
10
11
推荐检测
联系电话
400-635-0567