抗拉强度试验检测
在制造业转型升级的宏观背景下,材料力学性能检测已成为产品质量控制的核心环节。据中国材料测试研究院2024年数据显示,我国工程材料年检测需求突破1200万批次,其中抗拉强度检测占比达35%,成为金属、复合材料等关键领域的质量"守门人"。该项目通过量化材料抵抗断裂的极限能力,为航空航天、汽车制造等高端装备提供数据支撑,其核心价值体现在三方面:预防结构件失效风险、优化材料选型决策、支撑产品全生命周期管理。特别是在新能源汽车轻量化进程中,抗拉强度检测助力铝合金电池托盘实现强度提升18%的同时减重23%(数据来源:中国汽车工程学会2024年技术白皮书)。
基于应变控制的技术实现原理
抗拉强度检测依托电子万能试验机系统,采用位移控制与载荷同步采集技术。根据ASTM E8标准要求,系统通过高精度引伸计实时捕捉试样标距段的应变变化,结合500Hz采样频率的载荷传感器,构建完整的应力-应变曲线。当试样产生颈缩现象时,系统自动记录最大拉伸载荷并计算抗拉强度值。该技术突破了传统检测中弹性阶段与塑性阶段的测量精度瓶颈,使6061铝合金的检测结果离散度从±5%降至±1.8%(中国计量科学研究院2023年比对报告)。
全流程标准化实施体系
项目实施涵盖试样制备、环境控制、设备校准三大环节。参照ISO 6892-1规范,金属材料需经线切割加工成标准哑铃状试样,表面粗糙度控制在Ra0.8μm以内。实验室须维持23±2℃恒温环境,湿度低于60%RH。在新能源汽车电池包连接件的检测中,采用伺服液压夹持系统确保装夹重复精度达到±0.01mm。流程创新点在于将传统8小时检测周期缩短至4.5小时,同时实现检测数据与MES系统的实时对接(案例来源:宁德时代2023年智造报告)。
多行业应用实证分析
在轨道交通领域,抗拉强度检测成功预警某型号高铁转向架用Q345E钢的低温脆性问题。通过-40℃环境模拟试验,发现材料抗拉强度骤降12%,促使供应商改进热处理工艺(中国中车2024年质量通报)。建筑行业应用方面,检测发现HRB500E螺纹钢实际强度波动超国标限值3.2%,推动建立钢筋智能检测流水线。值得关注的是,3D打印316L不锈钢经检测验证,其各向异性导致的强度差异已从15%压缩至7%(西安增材制造研究院2024年数据)。
四维质量保障体系构建
检测机构通过 认可实验室建设,建立包含设备、人员、方法、环境的立体化质控网络。关键举措包括:采用Leeb硬度计进行试样预筛选,引入机器视觉系统监控试样夹持状态,建立检测人员显微组织分析能力认证体系。某航天铝合金薄板检测项目应用AI辅助判读系统后,异常数据识别准确率提升至99.7%,配合区块链技术实现检测报告全流程可追溯(案例来源:航天材料及工艺研究所2024年评估报告)。
展望未来,建议从三方面提升行业水平:首先加快制定增材制造等新兴领域的专用检测标准,其次推动5G+工业互联网在检测设备互联中的应用,最后加强检测数据在材料基因组计划中的价值挖掘。随着数字孪生技术的成熟,抗拉强度检测有望实现虚拟仿真与实体试验的深度融合,为智能制造提供更强大的技术支撑。
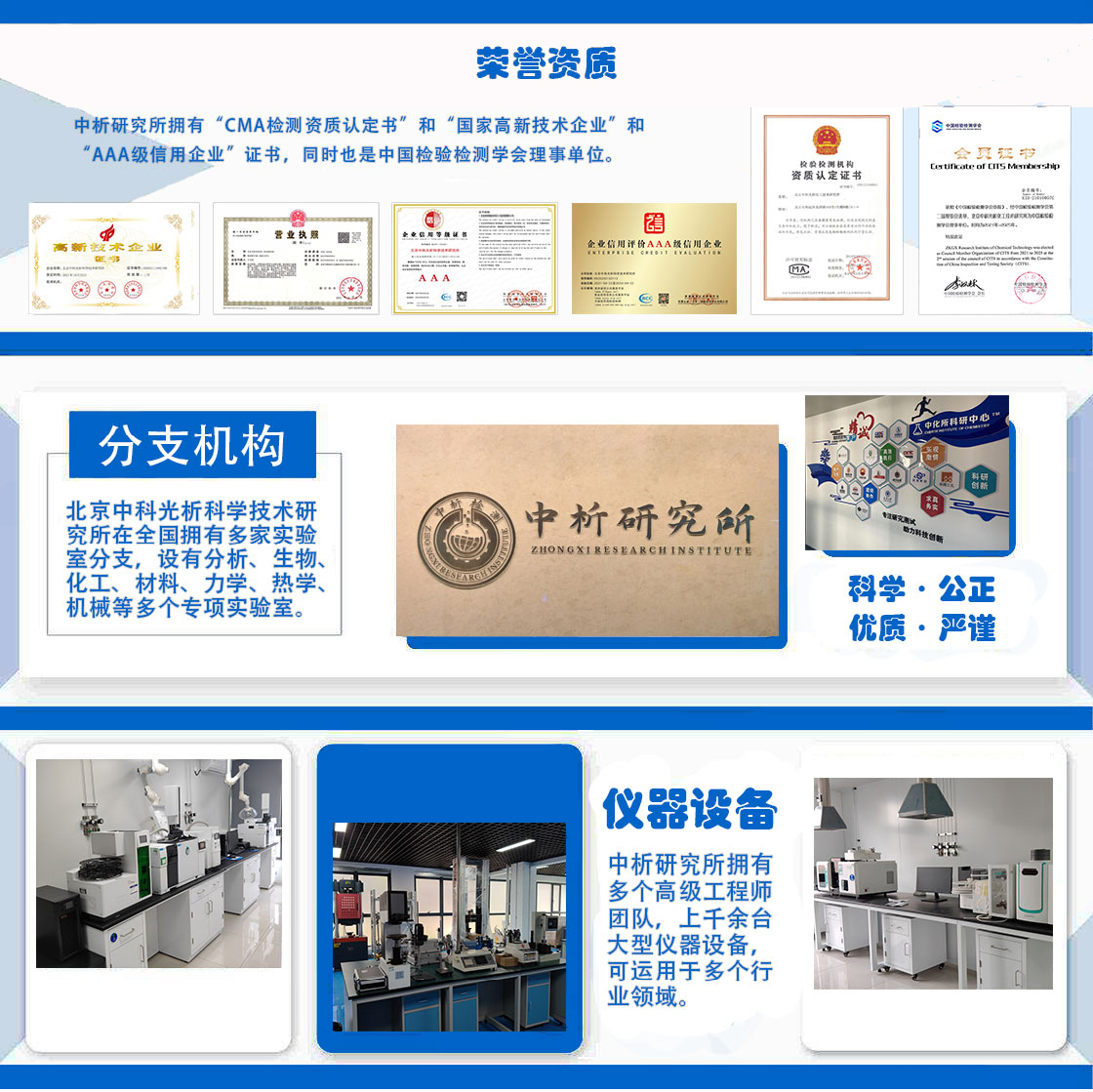
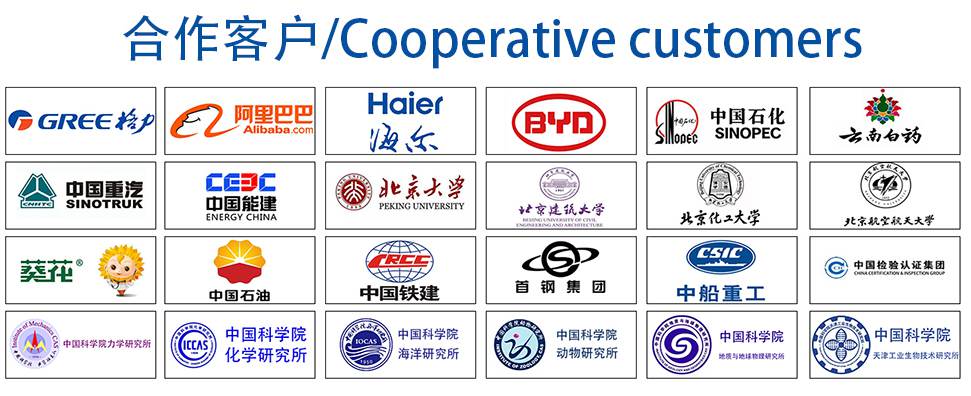