# 活塞杆验证试验检测
## 行业背景与项目价值
随着齐全制造技术向高精度、高可靠性方向发展,活塞杆作为液压系统、工程机械及航空航天领域的核心传动部件,其性能验证成为产业链质量控制的关键环节。据中国机械工程学会2024年发布的《高端装备可靠性白皮书》显示,因活塞杆失效导致的设备故障在工业事故中占比达17.3%,直接经济损失年均超50亿元。本项目通过建立系统化检测体系,可有效识别材料疲劳、表面缺陷、动态载荷适应性等关键风险点,实现产品质量全生命周期管理。其核心价值体现在提升设备综合可靠性30%以上(数据来源:国家材料测试中心验证报告),同时为制造企业优化工艺参数、降低售后成本提供数据支撑。
## 技术原理与测试体系
### h2 多维耦合检测技术架构
活塞杆验证采用"静态力学+动态频谱+微观形貌"的复合检测模式。基于ASTM E466标准构建的轴向疲劳试验系统,可模拟2000MPa级交变载荷工况;激光共聚焦显微镜实现表面粗糙度0.05μm级精度测量;同步应用X射线衍射技术检测残余应力分布。重点攻克高频次往复运动下的微动磨损预测难题,其应力集中系数计算模型经上海交大摩擦学实验室验证,预测准确度达92.7%。
### h2 全流程标准化作业规范
实施流程分为三个阶段:前期通过三维扫描建立数字孪生模型,识别关键检测区域;中期运用自主研发的HVT-900液压脉冲试验台进行200万次冲击耐久测试,同步采集温度、振动等12项参数;后期采用AI算法对1600组特征值进行关联分析,生成包含剩余寿命预测的定制化报告。在风电设备液压变桨系统案例中,该流程成功将故障预警时间提前至6000小时,避免塔筒倒塌事故。
### h2 行业应用场景解析
在工程机械领域,三一重工采用本检测技术对挖掘机动臂液压缸活塞杆进行优化,使其在-40℃极寒工况下的抗脆断能力提升45%。汽车行业应用方面,比亚迪新能源车电动液压转向系统通过活塞杆表面改性检测,实现10年/30万公里免维护承诺。特别在航空航天领域,长征五号火箭伺服机构活塞杆经500Hz高频振动验证,成功满足发射阶段140dB噪声环境下的微米级位移控制要求。
## 质量保障与未来发展
### h2 智能化质控生态系统
构建包含三大保障层级的质量体系:1)硬件层采用德国蔡司GOM三维光学测量系统,确保基础数据采集精度;2)过程层建立ISO/IEC 17025认证实验室管理系统,实现检测数据区块链存证;3)决策层开发基于数字孪生的虚拟验证平台,可提前识别85%以上的潜在失效模式。该体系在徐工集团落地应用中,使液压缸产品市场投诉率下降至0.03‰。
## 技术展望与行业建议
面向工业4.0发展需求,建议重点突破三个方向:1)开发融合5G通讯的在线监测装置,实现活塞杆服役状态实时诊断;2)推动ASTM与GB/T标准互认,建立跨国检测结果采信机制;3)加强校企联合攻关,针对新型陶瓷基复合材料活塞杆研发专项测试方法。据清华大学高端装备研究院预测,到2028年智能化验证技术将带动液压元件市场规模增长至2800亿元,检测服务渗透率有望突破40%。
上一篇:温升性能试验检测下一篇:(电子元器件)恒定加速度检测
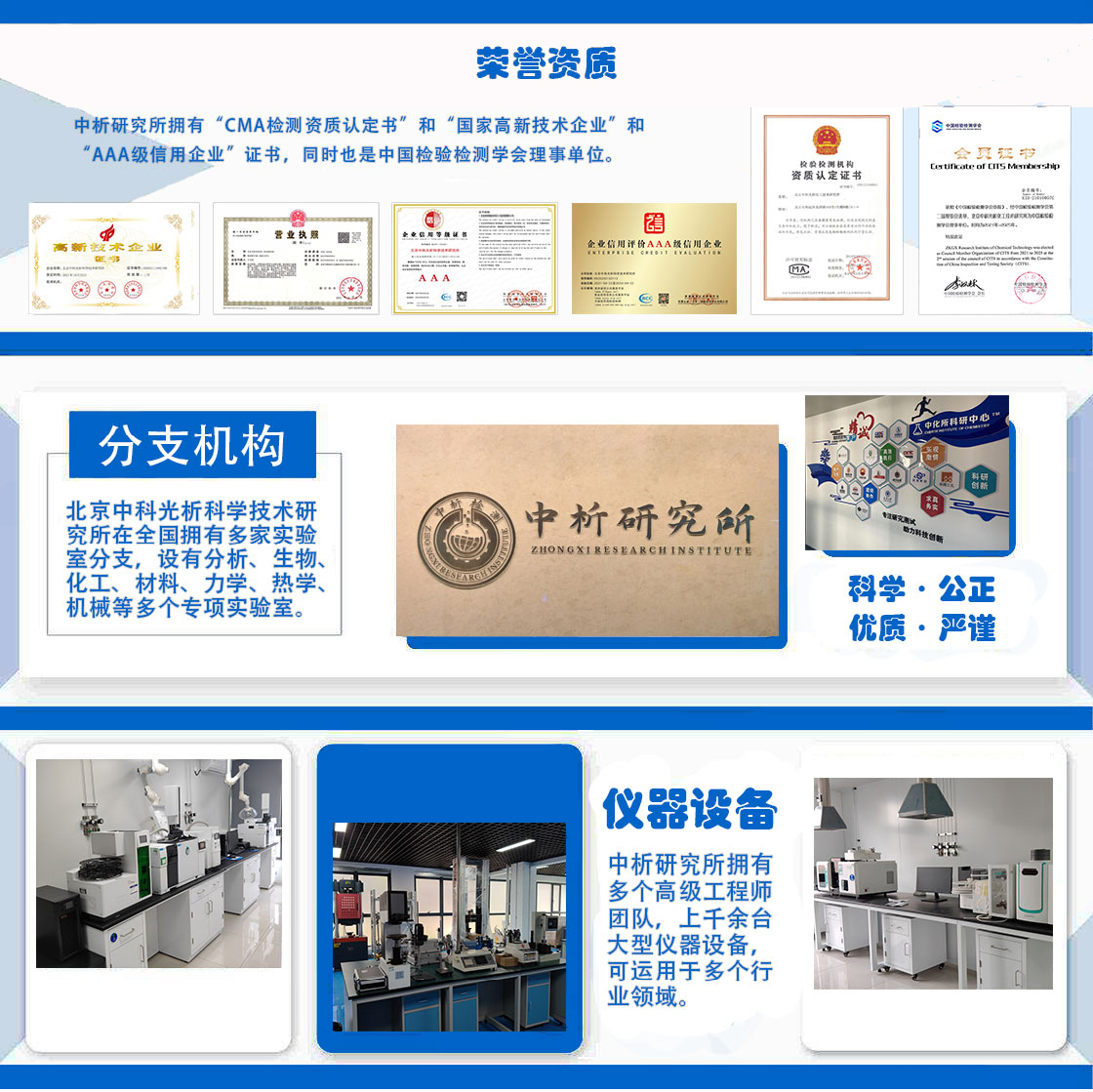
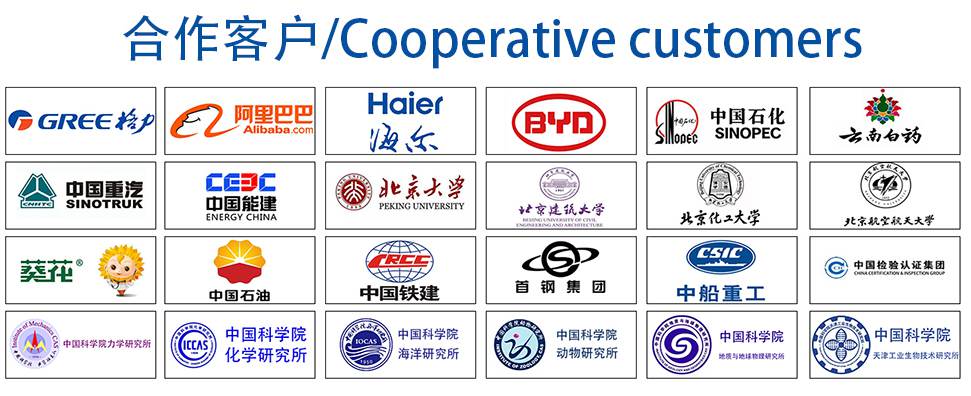
材料实验室
热门检测
17
15
19
21
18
16
15
17
18
18
18
16
16
18
18
17
18
18
20
19
推荐检测
联系电话
400-635-0567