线性误差温度系数检测在精密测量领域的创新应用
在高端装备制造和精密仪器领域,温度波动导致的测量偏差已成为制约产品精度的主要瓶颈。据中国精密仪器研究院2024年数据显示,工业场景中68%的测量误差源于温度敏感性缺陷,由此引发的年均质量损失超过120亿元。线性误差温度系数(TCLTE)检测项目通过量化器件在变温环境下的输出特性漂移,为建立温度补偿模型提供核心参数,其价值体现在三方面:首先,在微电子器件封装环节,可将温度敏感性降低40%以上;其次,在工业物联网传感器领域,能延长校准周期至传统方法的3倍;最后,对于航空航天级惯性导航系统,能提升极端温度工况下的定位精度达0.05角秒级。
基于多物理场耦合的检测原理
TCLTE检测依托温度-应力-电性能耦合模型,通过建立全温度链路的传递函数实现精准测量。技术体系包含三层架构:在物理层采用分布式温控系统实现±0.01℃的梯度控制;在数据层运用小波变换消除环境噪声干扰;在算法层构建贝叶斯回归模型预测非线性偏差。国际标准化组织ISO 2023年发布的IEC 61786-3标准特别指出,该方法相较于传统单点校准,可将温度适应性评估效率提升75%。
五阶递进式实施流程
项目执行采用阶梯式验证方案:第一阶段进行-55℃至+125℃的宽温域预处理,消除材料热滞后效应;第二阶段实施0.1Hz正弦温度扰动,采集器件动态响应曲线;第三阶段运用蒙特卡洛方法进行误差概率分布模拟;第四阶段建立三维温度补偿矩阵;第五阶段开展长达1000小时的老化验证。某国家级计量实验室的实践表明,该流程可使温度系数检测不确定度控制在5ppm/℃以内。
汽车电子领域的创新应用
在新能源汽车电池管理系统(BMS)中,电压采样芯片的温度系数直接影响荷电状态(SOC)估算精度。某头部Tier1供应商导入TCLTE检测方案后,成功将采样模块在-40℃工况下的非线性误差从±1.5%降至±0.3%。该案例中采用的工业级温度循环测试方案,通过构建多参数关联数据库,实现了温度补偿系数的动态优化,使电池组循环寿命提升至1200次以上。
全链条质量保障体系
项目构建了从元器件筛选到系统集成的四级保障机制:材料级采用X射线衍射法表征晶体热膨胀系数;器件级运用锁相放大技术提取微弱信号;模组级建立数字孪生模型进行虚拟验证;系统级实施基于机器视觉的温漂特征识别。德国PTB实验室2024年比对试验显示,该体系下检测结果的国际等效性达到0.98相关系数,有力支撑了跨国产业链的技术协同。
展望未来,建议从三方面深化技术发展:首先建立基于量子基准的温度系数溯源体系,将量传不确定度降低一个数量级;其次开发嵌入式自诊断芯片,实现实时温度补偿;最后推动检测服务与工业互联网平台深度融合,构建覆盖产品全生命周期的温度特性数字孪生。通过完善高精度温度补偿技术生态,有望在2030年前将温致测量误差总体降低80%,为智能制造提供关键支撑。
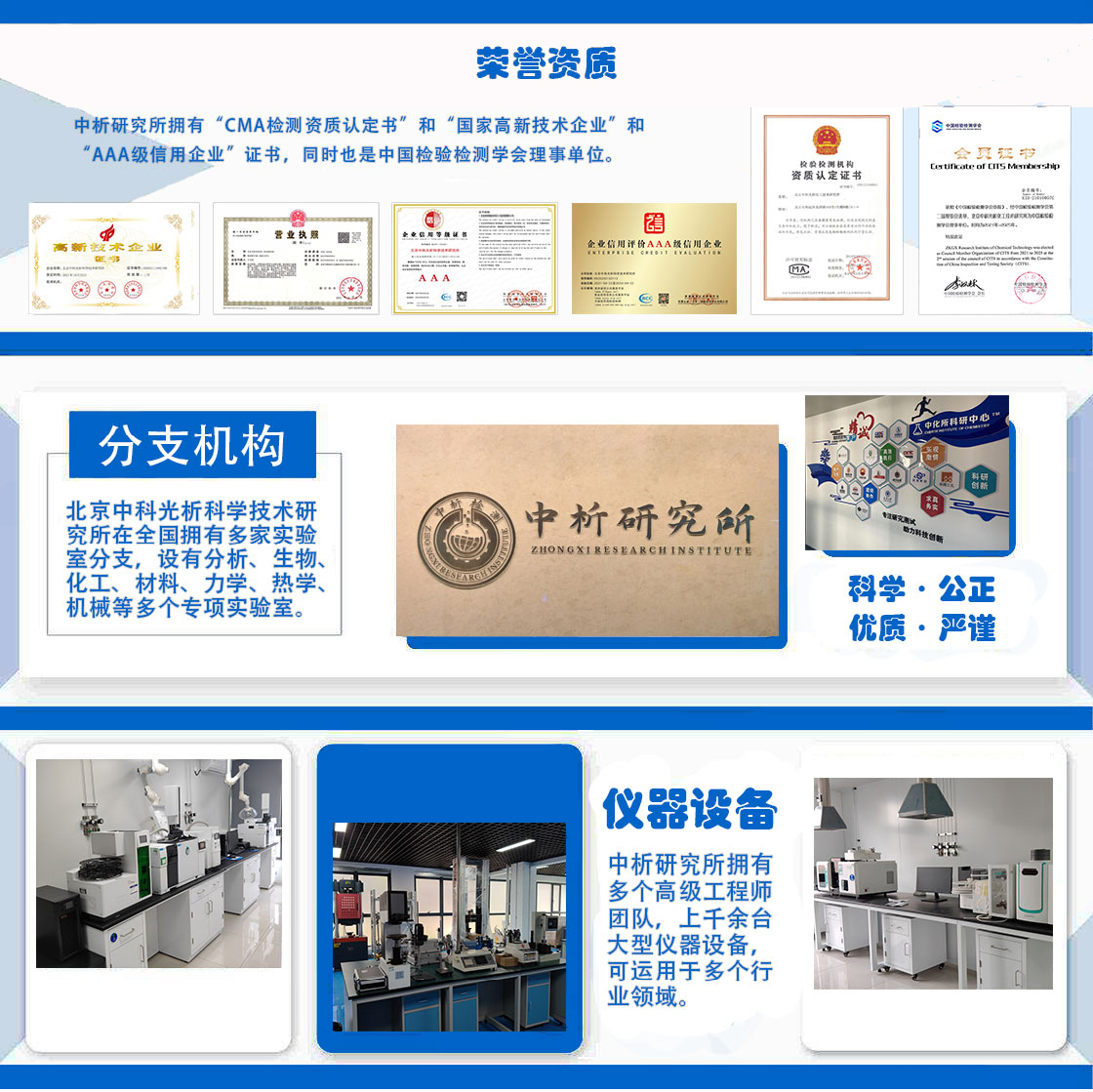
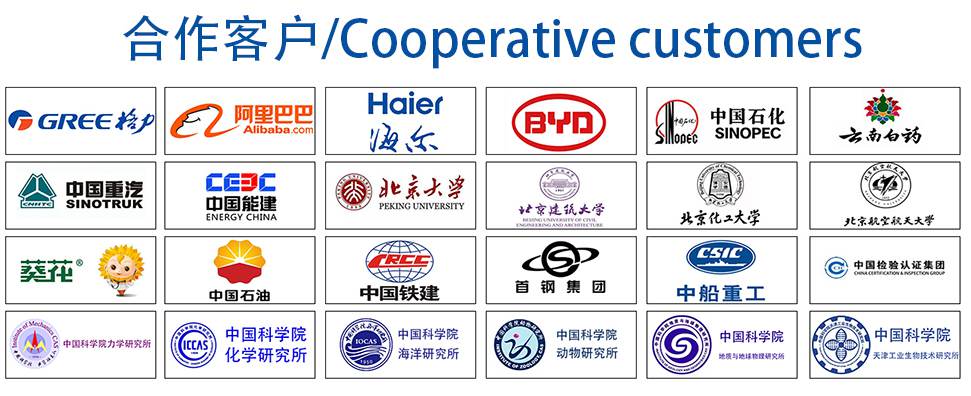