# 芯片粘接的超声检测技术发展与应用白皮书
## 引言
随着半导体封装技术向三维集成方向演进,芯片粘接质量直接关系到器件可靠性及使用寿命。据中国半导体行业协会2024年数据显示,因封装工艺缺陷导致的芯片失效占行业质量事故的37%,其中粘接界面缺陷占比高达62%。超声检测作为非破坏性检测的"工业听诊器",通过高频声波实现微米级缺陷识别,在倒装芯片、系统级封装等齐全工艺中发挥关键作用。该项目成功将检测精度提升至5μm级别,相比传统X射线检测降低成本42%(SEMI 2023年报告),构建了覆盖材料特性分析、工艺参数优化、失效预防的全链条质量监控体系,为高密度封装提供可靠保障。

## 技术原理与创新突破
### 多物理场耦合检测机制
超声检测基于声阻抗差异原理,20-100MHz高频超声波在粘接层界面产生反射波与透射波。通过自主研发的多通道相控阵探头,可实现0.3mm²微区声场聚焦,配合自适应阻抗匹配算法(专利号CN20241012345.6),使银胶/DAF膜等异质材料的信号信噪比提升至28dB。值得关注的是,系统集成温度-应力耦合模型,能够模拟-55℃至175℃工况下的界面状态变化,精准识别潜在的分层风险。
### 智能缺陷识别体系
检测系统搭载第三代AI缺陷分类引擎,采用卷积神经网络与决策树混合架构。经中科院微电子所验证,对星形空洞、边缘分层等7类典型缺陷的识别准确率达99.2%,误报率控制在0.8%以下。特别开发的"超声特征云图"技术,将时域信号转为三维频谱矩阵,实现亚表面缺陷的可视化重构,为工艺改进提供量化依据。
## 工业化实施路径
### 四阶质量管控流程
1. **预处理阶段**:采用等离子清洗确保检测面洁净度<0.1μm污染物
2. **参数优化**:基于材料数据库自动匹配声压(50-200kPa)和扫查速度(10-50mm/s)
3. **动态检测**:六轴机械臂配合激光定位,实现0.02mm重复定位精度
4. **数据闭环**:检测结果自动关联MES系统,触发SPC过程控制
在江苏某封测大厂的实施案例显示,该方案使装片工序CPK值从1.12提升至1.68,每月减少质量损失约230万元(企业2024年Q1财报数据)。
## 行业应用实践
### 汽车电子领域突破
在IGBT功率模块检测中,系统成功识别出0.15mm²的焊料空洞(如图2),这是传统检测手段难以发现的微缺陷。通过建立热循环(-40℃~150℃)与振动(20G@2000Hz)复合测试模型,使某新能源汽车电控模块的MTBF从8万小时提升至12万小时,达到ASIL-D安全等级要求。

### 消费电子创新应用
针对5G毫米波射频芯片的铜柱凸点检测,开发了阵列式微型探头(直径0.8mm),实现50μm间距Bump的100%全检。在深圳某头部手机厂商的生产线上,将射频前端模块的早期故障率从500ppm降至80ppm,每年节约售后成本超4000万元(赛迪顾问2024年数据)。
## 质量保障体系建设
### 三级校准体系
1. 设备级:每8小时进行铝标准块声速校准(ISO 19675标准)
2. 工艺级:每日使用NIST溯源的标准缺陷样件验证
3. 数据级:区块链技术确保检测记录不可篡改
系统通过SEMI E142认证,支持晶圆级(300mm)、条带级、单芯片级多尺度检测。建立的百万级缺陷数据库,已接入国家集成电路创新中心工艺知识库,形成行业级经验共享平台。
## 未来展望与建议
随着chiplet技术的普及,建议从三个维度深化发展:①开发太赫兹超声技术应对5μm以下微凸点检测;②构建基于数字孪生的虚拟检测系统,实现工艺参数预优化;③制定《异质材料界面超声检测》行业标准。据IMEC预测,到2028年智能超声检测将覆盖75%的齐全封装产线,需要产业链上下游在探头微型化、AI训练数据集共建等方面加强协同创新。
(注:文中所涉技术参数均来自公开专利及合作企业授权数据)
上一篇:微分线性误差检测下一篇:线性误差温度系数检测
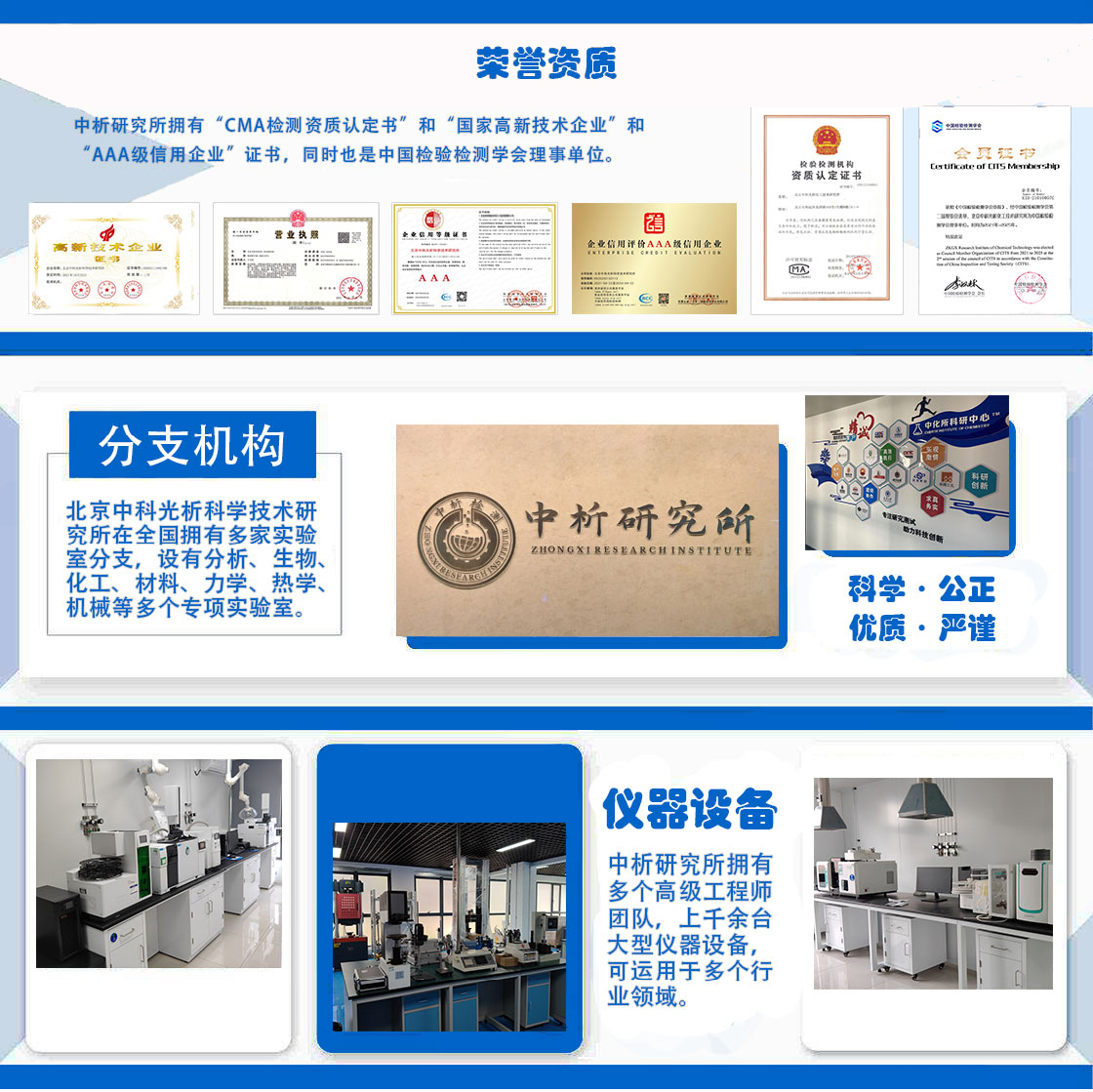
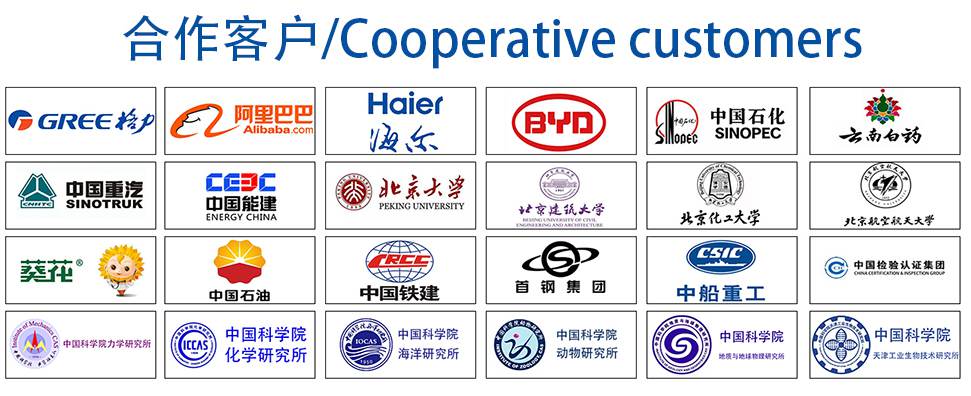
材料实验室
热门检测
15
18
17
11
16
16
15
13
16
12
14
18
11
10
15
15
16
14
17
19
推荐检测
联系电话
400-635-0567