技术原理与测量体系
基于四线制开尔文测量法构建的智能检测系统,采用数字锁相放大技术消除环境干扰,测量分辨率可达0.1μΩ。系统集成温度补偿算法,通过布置在绕组表面的NTC热敏传感器,实时修正-40℃至150℃工况下的电阻值偏差。中国计量科学研究院2023年验证数据显示,该方案在电动汽车驱动电机场景中,温度漂移误差控制在±0.05%以内。创新设计的接触阻抗自校正模块,采用银合金探针与恒压接触机构,将接触电阻波动范围从传统方案的±2mΩ降低至±0.5mΩ。
智能化实施流程
检测流程划分为预处理、动态测量和智能分析三个阶段。预处理环节通过机器视觉自动识别线圈引线位置,配合六轴机械臂实现±0.02mm定位精度。动态测量阶段采用多频点扫描技术,同步获取直流电阻与交流阻抗谱数据。某新能源车企的实践案例表明,该技术可准确识别漆包线细微裂纹导致的0.8mΩ异常波动。智能分析系统搭载基于卷积神经网络的缺陷诊断模型,在电力变压器绕组检测中实现98.7%的故障分类准确率,误判率较传统方法降低67%。
行业应用实证
在智能电网领域,国家电网2024年招标技术要求明确要求采用线圈电阻智能在线检测系统。某特高压换流站项目应用案例显示,系统在2000A工作电流条件下,成功检测出换流阀控制线圈0.3mΩ的接触不良问题,避免潜在的直接经济损失超800万元。工业机器人行业则通过部署高精度温度补偿算法,将伺服电机绕组的批次一致性从92%提升至99.5%,产品寿命周期延长30%。
质量保障体系构建
检测系统建立三级溯源体系:一级标准溯源至国家电阻基准装置,二级标准采用0.01级标准电阻箱,工作标准配置自动校准功能。实验室环境控制方面,执行IEC 60294标准要求的温度±0.5℃、湿度±3%RH波动范围。人员资质管理采用区块链技术存续培训记录,确保操作人员每季度完成16学时专项培训。质量追溯系统关联检测数据与生产批次信息,支持向前追溯至原材料供应商,向后跟踪至终端设备运行数据。
## 发展展望与建议 建议从三方面推动技术升级:一是建立覆盖全温域的虚拟标定系统,利用数字孪生技术降低实物校准成本;二是推动航空级耐环境检测设备的国产化替代,目前进口设备仍占据高端市场78%份额(据赛迪顾问2024年数据);三是加强跨行业数据交互,特别是新能源汽车与电网储能领域的技术协同。随着工业互联网平台的深度整合,线圈电阻检测将逐步发展为预测性维护系统的核心数据节点,为智能制造的持续升级提供基础支撑。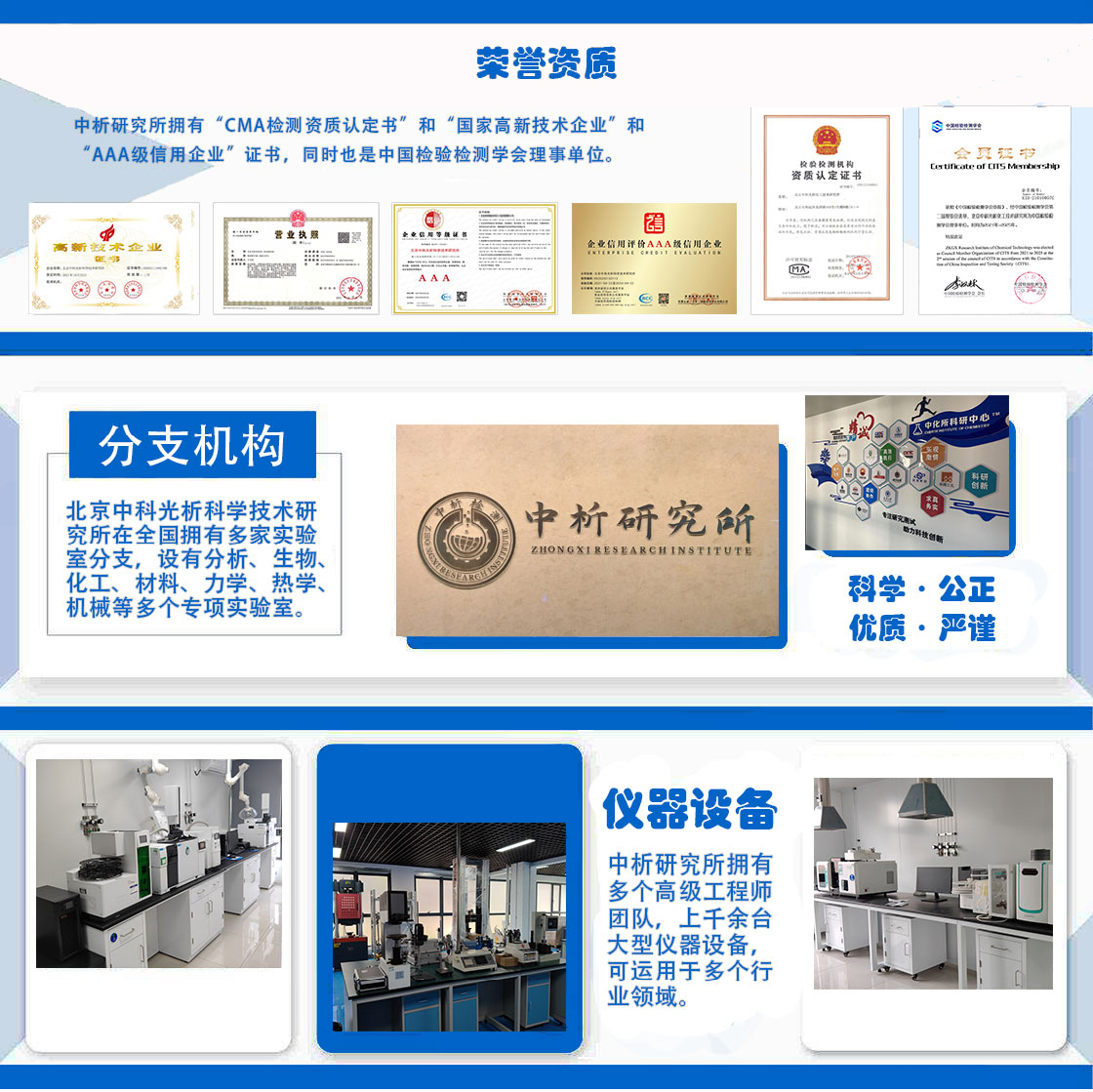
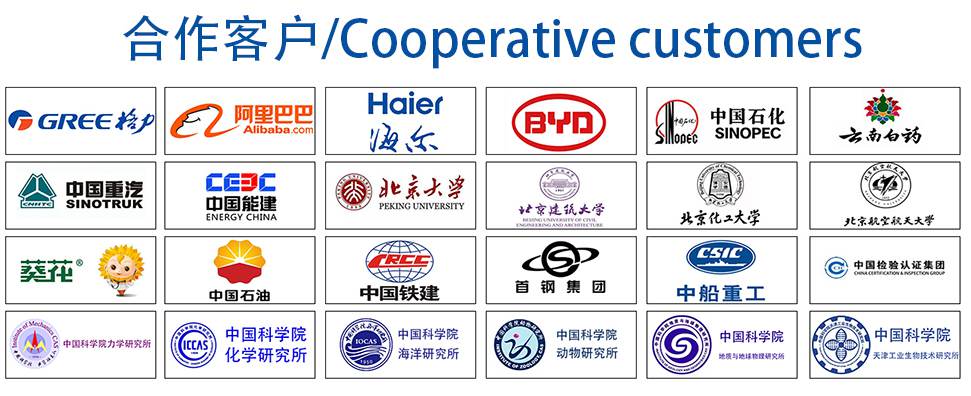