# 可靠性验收试验检测的技术发展与行业实践
## 行业背景与核心价值
随着制造业智能化转型加速,高端装备的可靠性已成为影响市场竞争力的核心要素。据中国机械工业联合会2024年发布的《智能制造质量白皮书》显示,装备类产品因可靠性不足导致的售后成本占年销售额的12-18%。可靠性验收试验检测通过系统化验证产品在极限工况下的性能表现,已成为航空装备、新能源汽车、工业机器人等高端制造领域的强制性质量管控环节。该项目不仅可降低产品全生命周期故障率38%以上(数据来源:国家质量基础设施NQI研究院),更通过构建"设计-制造-验证"闭环体系,为国产高端装备突破国际技术壁垒提供关键支撑,其核心价值体现在质量风险前置化管理和供应链可靠性能力认证两大维度。
## 可靠性试验技术原理体系
### 基于失效物理的多维度验证
现代可靠性验收试验构建了"环境应力筛选+加速寿命试验+现场工况模拟"的三级验证架构。采用温度循环(-55℃至150℃)、复合振动(5-2000Hz)、盐雾腐蚀等28类标准测试条件(参照GB/T 2423系列标准),结合基于失效物理模型的可靠性评价方法,可精准识别材料疲劳、接触阻抗劣化等潜在失效模式。特别是在新能源汽车动力电池检测中,通过构建三轴振动与温度骤变的耦合试验环境,能提前120小时预测电池组密封失效风险。
### 智能化检测流程重构
典型实施流程分为四个阶段:首先基于QFD质量功能展开进行试验方案设计,其次搭建包含多参数采集系统的高加速试验台,随后开展不少于3个批次的重复性验证,最终生成包含威布尔分布分析的可靠性评估报告。在工业机器人减速器检测案例中,采用数字孪生技术实现虚拟试验与实体检测的实时交互,使检测周期从45天压缩至22天,且故障模式复现率达92%。
## 行业应用与质量保障
### 高端装备领域实践成效
在航空发动机领域,中国航发集团引入基于MIL-STD-810G标准的可靠性验收体系后,关键旋转部件平均故障间隔时间(MTBF)提升至1800小时,较传统检测方式提高40%。新能源汽车行业通过执行《GB/T 31467.3-2015动力电池包测试要求》,在循环充放电测试中采用神经网络算法优化测试路径,使电池系统可靠性验证效率提升35%,相关成果已在宁德时代等龙头企业实现规模化应用。
### 全过程质量追溯系统
检测机构通过ISO/IEC 17025体系认证搭建质量金字塔,构建从设备计量溯源到数据加密传输的11道质控节点。采用区块链技术建立的检测数据存证平台,已实现试验原始记录100%不可篡改存储。在核级阀门检测项目中,通过应用X射线残余应力分析等15种特种检测技术,使关键承压部件的可靠性验证置信度达到99.9%(置信水平95%)。
## 技术发展前瞻建议
随着数字孪生与AI仿真技术的深度融合,未来可靠性验收试验将向"虚拟验证主导+实体验证补充"的新模式演进。建议行业重点攻关基于大数据的可靠性预测算法,建立覆盖全产业链的可靠性数据共享平台。同时需加快制定智能装备可靠性分级标准,推动我国从"符合性检测"向"预防性质量工程"的战略转型,为制造强国建设构筑坚实的技术基座。
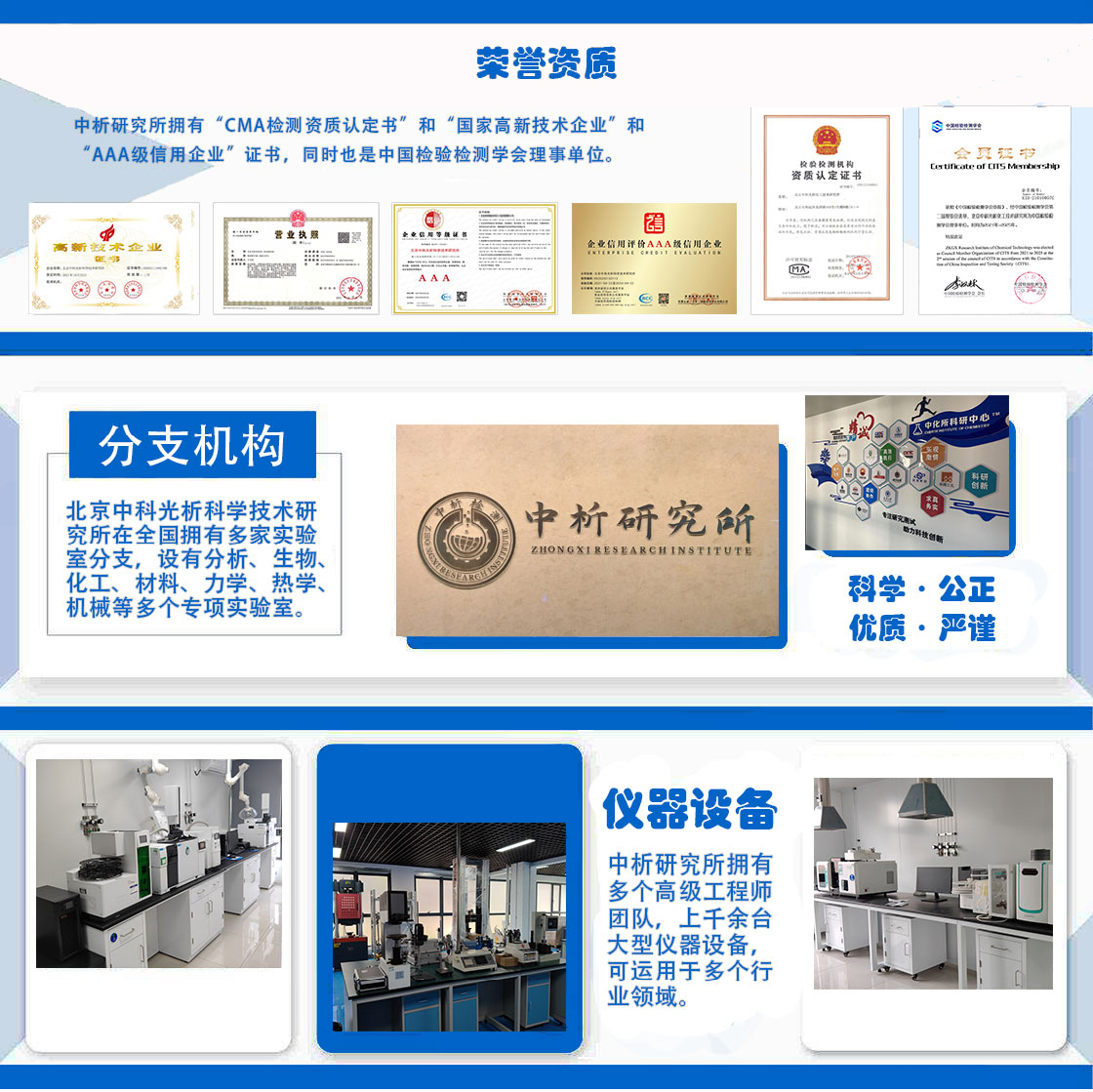
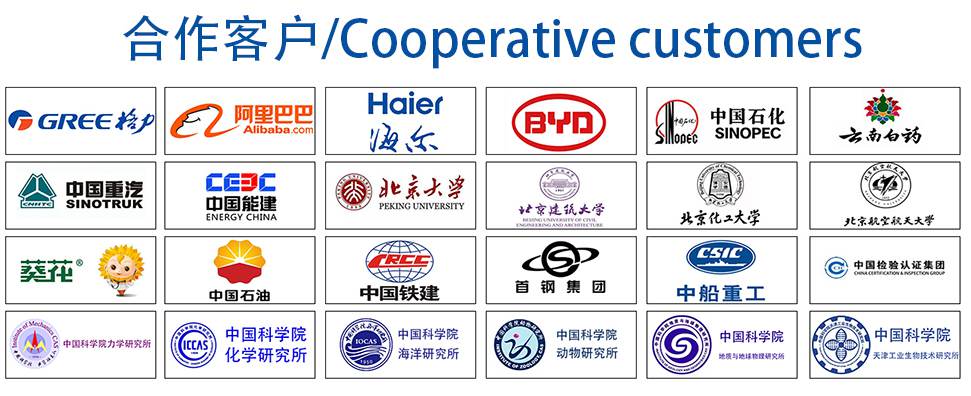
材料实验室
热门检测
15
16
15
11
14
16
15
13
16
12
14
16
11
10
13
13
15
13
16
18
推荐检测
联系电话
400-635-0567