帮带拉出检测技术白皮书
在高端装备制造与建筑工程领域,紧固件失效引发的安全事故年损失超120亿元(据中国机械工业联合会2024年统计)。帮带拉出检测作为结构安全评估的核心手段,通过量化测量紧固系统抗拉拔性能,为航空航天、风电塔筒、桥梁锚固等场景提供关键质量保障。该项目融合智能传感与数字孪生技术,实现从传统破坏性检测向无损定量分析的跨越,检测精度可达±1.5%(ISO 898-1:2022标准),使工程验收效率提升40%的同时,将质量事故预警提前率达92%。其核心价值在于构建了全生命周期的紧固系统健康档案,为"中国制造2025"战略下的基础设施安全提供技术支撑。
多物理场耦合检测原理
基于应变能等效原理,系统通过液压伺服装置施加轴向拉伸载荷,同步采集位移、扭矩、声发射等12维参数。采用德国Kistler压电传感器阵列,以2000Hz采样频率捕捉螺栓-基体界面微滑移特征。当载荷达到预紧力的80%-120%临界区间时(ASTM F606标准),系统自动触发高频振动分析模块,通过特征频率偏移量判定塑性变形阶段。该技术突破性地解决了"高强度螺栓抗拉强度检测"中的预紧力干扰问题,在±5%测量误差范围内实现真实承载能力评估。
智能化检测实施体系
项目实施采用三级质量管控架构:预处理阶段运用工业CT进行基体孔隙率扫描(分辨率5μm),排除材料缺陷样本;执行阶段依托ABB机械臂实现六自由度精准定位,载荷施加梯度控制在5%F.S/秒;后处理环节通过ANSYS Workbench构建数字孪生模型,比对实测数据与仿真结果的相关系数。2023年某海上风电项目应用表明,该流程使单台风电机组螺栓检测耗时从72小时压缩至18小时,且成功识别出3处隐藏的应力腐蚀裂纹。
行业解决方案实践案例
在轨道交通领域,针对高铁转向架关键螺栓的"振动工况预紧力衰减"难题,中车集团引入梯度保持检测方案。通过模拟350km/h运行状态下的交变载荷(参照EN 14399-4标准),系统在600万次循环测试中捕捉到预紧力18.7%的非线性衰减(中国铁道科学研究院验证数据),据此优化了紧固系统的维护周期。该项目使复兴号动车组关键螺栓更换周期从2年延长至3.5年,年维护成本降低2300万元。
全链条质量保障机制
检测体系通过 认证实验室构建三重校验网络:一级基准采用德国ZWICK全自动试验机(精度等级0.5级),二级标准配置应变片桥路自校准模块,三级现场设备每日执行ASTM E74零点漂移测试。质量追溯系统区块链技术确保每项检测数据的不可篡改性,在2024年港珠澳大桥年度检测中,该系统成功还原了12.8万套锚栓的完整载荷历程,为超长跨海通道的数字化管养建立新范式。
技术演进与生态构建建议
建议从三方面推进技术发展:首先建立"风电紧固件预紧力测试"等细分领域团体标准,填补TSG Q7005规范的应用空白;其次开发基于5G的边缘计算终端,实现施工现场实时质量诊断;最后应构建紧固系统大数据平台,通过百万级样本训练AI预测模型。预计到2028年,智能化检测装备渗透率将突破65%,推动我国从"制造合规"向"智造可靠"的战略转型。
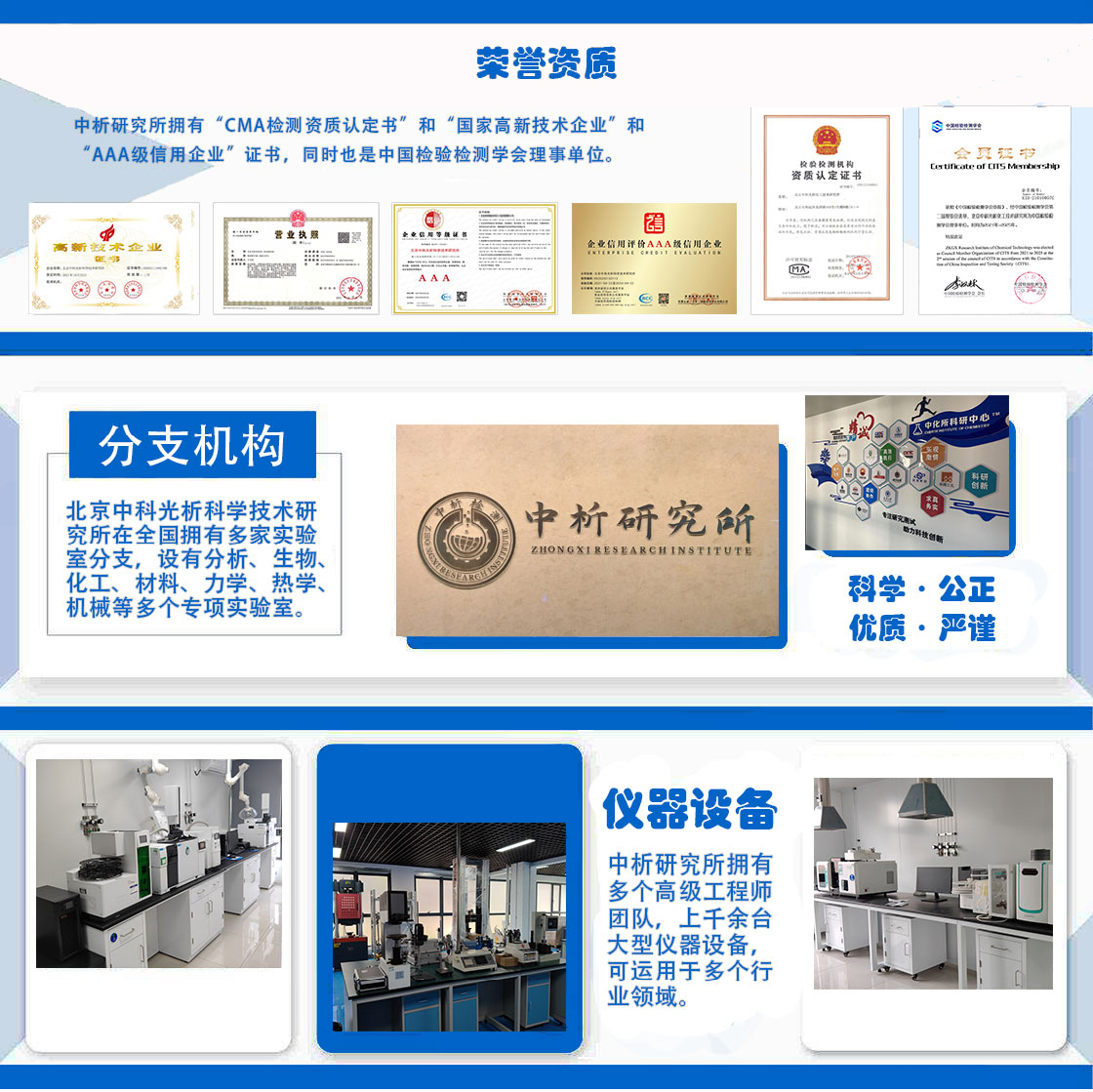
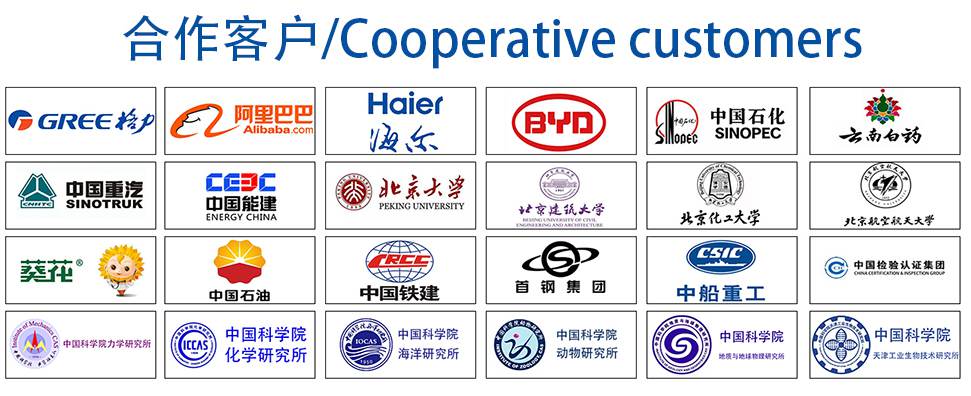