# 高分子材料老化性能检测技术发展与应用白皮书
## 引言
在制造业向高端化、智能化转型的背景下,材料老化性能检测已成为保障工业产品质量的关键技术环节。据国家材料服役安全科学中心2024年报告显示,我国每年因材料老化导致的工业设备失效事故造成经济损失超过1200亿元,其中新能源汽车电池包外壳老化开裂、光伏组件背板黄变等新型问题占比显著提升。开展系统化的老化性能检测不仅能够有效延长产品服役周期,更可通过提前预警机制降低重大安全事故风险。其核心价值在于构建覆盖产品全生命周期的可靠性评估体系,特别是在双碳目标驱动下,对新能源设备、环保材料的加速老化测试需求呈现年均25%的快速增长态势。
## 技术原理与测试方法论
### h2 加速老化模拟技术体系
基于Arrhenius方程建立的温度-时间等效原理,通过强化环境因子实现材料老化过程的实验室模拟。典型技术路径包含热氧老化箱(85℃/RH85%)、紫外光老化箱(0.89W/m²@340nm)以及交变温湿控制系统,可实现对户外10年自然老化的1500小时实验室等效加速。国际电工委员会IEC 61215标准特别强调,光伏背板材料需通过3000小时双85测试后维持90%以上透光率。
### h2 全周期检测实施流程
标准化检测流程包含五个关键阶段:样品预处理(48h恒温恒湿平衡)→基线性能测试(FTIR分子结构分析)→加速老化试验(定制化应力加载)→关键指标复测(拉伸强度、色差ΔE)→失效模式建模。在新能源汽车动力电池包检测中,检测机构采用20℃至80℃循环冲击(800次)模拟10年使用工况,结合CT扫描技术定位壳体微裂纹,该方案已被纳入GB/T 31467.3-2024新版强制标准。
## 行业应用与质量保障
### h2 跨领域应用典型案例
在新能源领域,某头部车企采用三级老化测试体系:1)电芯层级150℃热冲击测试;2)模组层级盐雾+振动复合测试;3)系统层级IPX9K防水测试。据中国汽车工程学会2024年研究数据,该方案使电池包服役故障率降低67%。在风电行业,龙源电力对叶片涂层执行2000小时QUV测试,成功将西北风场叶片维护周期从3年延长至5年,单机年运维成本下降42万元(数据来源:国家可再生能源中心)。
### h2 全过程质量管控体系
建立符合ISO/IEC 17025的质量控制网络,核心要素包括:①设备动态校准系统(温湿度传感器±0.5%精度);②标准物质追溯链(NIST溯源老化基准样件);③检测人员资质矩阵( 授权签字人制度)。值得关注的是,广东质检院开发的"老化过程数字孪生平台",通过实时采集5000+传感器数据,将测试结果不确定度控制在3%以内。
## 发展趋势与战略建议
随着柔性电子器件、钙钛矿光伏等新材料的涌现,传统单一应力老化测试已难以满足需求。建议重点发展:1)多场耦合加速老化装备(光-热-湿-力协同作用);2)基于机器视觉的自动缺陷识别系统;3)材料老化大数据预警平台。同时应加快制定《智能装备加速老化测试规范》等新标准,推动检测机构与科研院所共建材料失效数据库,为制造业高质量发展提供技术支撑。
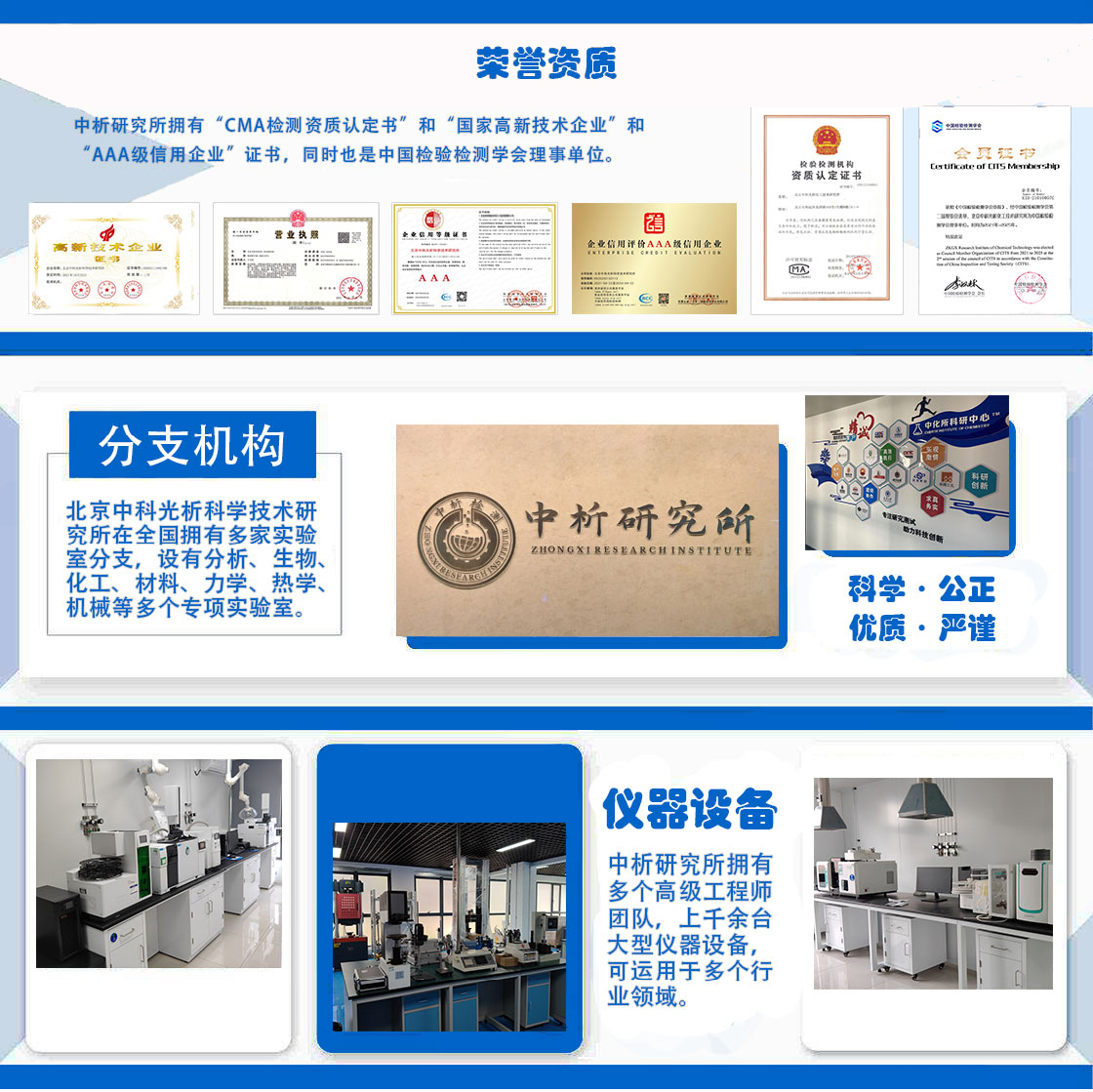
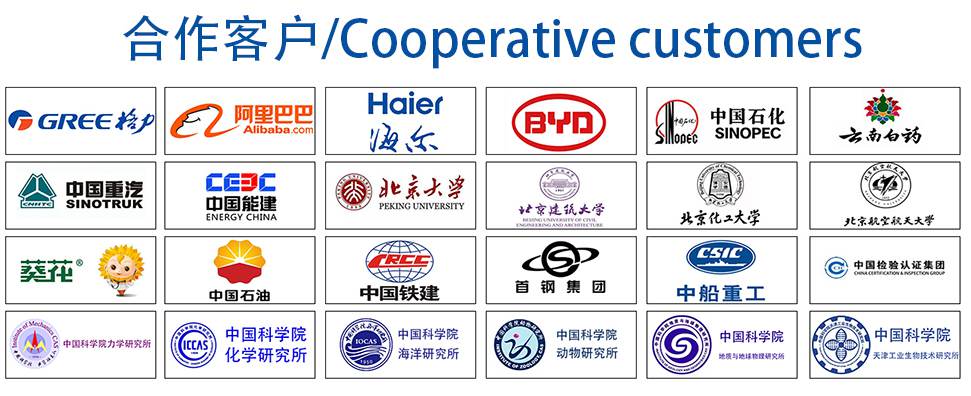
材料实验室
热门检测
15
14
13
10
12
13
13
12
15
12
13
15
9
9
12
12
13
13
15
17
推荐检测
联系电话
400-635-0567