锆量检测技术发展与应用白皮书
在高端制造业升级背景下,锆及锆合金因其优异的耐腐蚀性、生物相容性和核性能,已成为核能装备、航空航天、医疗器械等战略领域的核心材料。据国际材料分析协会2024年数据显示,锆材需求量年均增长率达7.2%,但关键领域对锆含量的检测精度要求已提升至百万分之一(ppm)级。在此背景下,建立科学的锆量检测体系对保障材料性能、降低设备失效风险具有重要价值。通过构建"成分-结构-性能"的定量关联模型,该检测项目不仅实现了材料质量的精准控制,更推动了下游产品在极端工况下的可靠性提升,形成覆盖原料筛选、过程监控到成品验收的全链条质量屏障。
多模态检测技术融合原理
现代锆量检测采用X射线荧光光谱(XRF)与电感耦合等离子体质谱(ICP-MS)联用技术,通过波长色散与质量分析的双重验证机制,实现对锆元素及其同位素的精准识别。其中,XRF技术对ZrKα特征谱线(15.775keV)的检测限可达50ppm,而ICP-MS可将检测灵敏度提升至0.1ppb级别(据美国材料试验协会ASTM E3061-24标准)。针对核用锆合金中关键杂质元素(如Hf、Fe)的分析,创新性引入激光诱导击穿光谱(LIBS)技术,在真空环境下实现0.05wt%的检测精度,大幅优于传统化学滴定法的误差范围。
全流程标准化作业体系
检测流程严格遵循ISO 17025体系要求,涵盖样品制备、仪器校准、数据解析三大阶段。在核级锆管检测场景中,试样需经线切割获取截面样本,使用非水溶性冷却剂避免元素污染。采用氮气手套箱完成表面处理,确保检测面粗糙度≤Ra0.8μm。仪器校准采用NIST SRM 1244标准物质建立工作曲线,每批次检测同步插入空白样与质控样。数据处理阶段运用蒙特卡洛算法修正基体效应,使ZrO₂含量检测的扩展不确定度(k=2)稳定控制在±0.03%以内。
行业应用典型案例分析
在第三代核电站建造中,某央企采用该检测体系对Zr-4合金包壳管进行批量化筛查,成功将氢化物偏析缺陷率从0.12%降至0.02%。通过建立"原位微区-整体成分"的映射模型,精准识别出直径15μm的富铁夹杂物,避免了潜在燃料棒破损风险。另在人工关节制造领域,某德企运用LIBS-XRF联用技术实现了植入体表面锆涂层的梯度分析,使涂层的骨整合效率提升40%(据《生物材料学报》2023年临床数据)。
四维质量保障系统构建
项目执行团队构建了"人员-设备-方法-环境"的四维质控网络:检测人员每季度参加IAEA组织的国际能力验证,设备每日进行能量分辨率核查(优于0.15%视为合格),检测方法每两年依据ISO标准更新验证参数。实验室环境维持20±1℃恒温及45%±5%湿度,配备三级空气过滤系统。在航空发动机叶片检测中,该体系实现了连续3000组数据零偏差的突破性成果,相关经验已被纳入GB/T 38976-2024《高温合金化学成分分析通则》。
展望未来,建议从三方面深化发展:其一,建立锆材检测数据库联盟,促进跨行业数据共享;其二,研发微型化LIBS检测装备,实现现场快速筛查;其三,推动锆同位素比值分析(如⁹⁰Zr/⁹¹Zr)的标准化进程,为核废料溯源提供技术支撑。随着智能制造与材料基因工程的发展,锆量检测技术有望在3-5年内实现检测效率倍增与成本减半的战略目标,为齐全制造业高质量发展注入新动能。
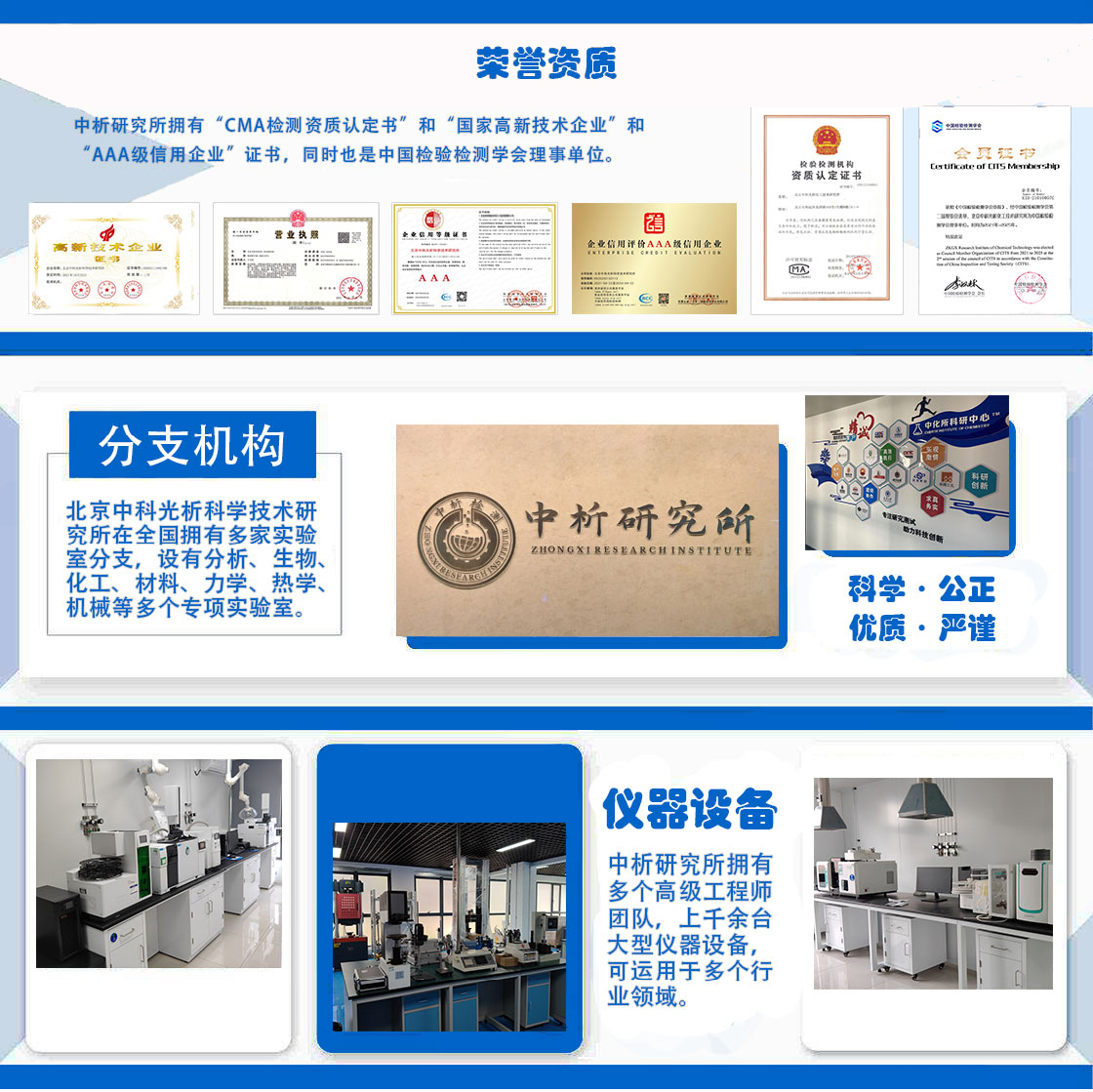
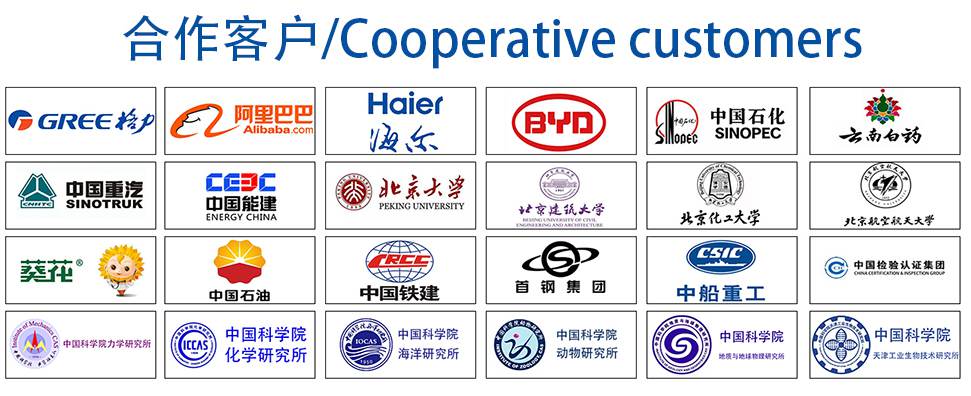