振实密度检测在粉体材料行业的技术创新与应用实践
在新能源、制药及齐全制造领域快速发展的当下,粉体材料的物理性能指标已成为决定产品品质的关键参数。据中国粉体技术协会2024年行业报告显示,我国粉体材料市场规模已突破8000亿元,其中锂电正极材料、金属增材制造粉末等高端领域年均增长率达28%。振实密度作为衡量粉体流动性和填充性能的核心指标,直接影响着电池电极涂覆均匀性、3D打印成型精度等关键工艺环节。通过建立标准化的振实密度检测体系,企业可精准把控原料质量,优化造粒工艺参数,进而提升产品批次一致性。特别是在新能源电池领域,振实密度每提高0.1g/cm³可使极片压实密度提升5%,据宁德时代技术白皮书披露,这项改进可直接带来电池能量密度2%的增益。
技术原理与测量方法论
振实密度检测基于粉体颗粒动态堆积理论,通过标准化的机械振动使粉末颗粒达到最紧密排列状态。检测系统通常由精密振动装置、量筒模块和数据处理单元构成,符合ASTM B527、GB/T 5162等国际通用标准。测量过程中,仪器以固定振幅(通常3-14mm)和频率(250-300次/分钟)进行规律振动,通过激光位移传感器记录粉体体积变化曲线。当连续三次测量体积差小于2%时,系统自动判定达到稳定振实状态,结合质量测量数据计算得出振实密度值。该技术实现了从经验判断到量化分析的跨越,特别适用于纳米级陶瓷粉末、高粘度药物微粒等复杂物料的精确测量。
全流程质量管控实施方案
完整的振实密度检测体系包含三个核心环节:首先是预处理阶段,需在恒温恒湿环境(23±2℃、50±5%RH)下进行12小时以上样品平衡,消除静电和吸湿影响;其次是设备校准环节,采用NIST标准粉体进行五点法系统验证,确保量筒容积误差≤0.5%;最后是动态检测过程,通过配备自动喂料系统和AI视觉识别模块,有效避免人为操作偏差。某头部锂电材料企业的实践表明,实施该方案后产品振实密度波动范围从±0.15g/cm³缩小至±0.06g/cm³,极片涂布缺陷率降低42%。
行业典型应用场景解析
在锂离子电池正极材料领域,振实密度检测已成为工艺优化的关键节点。某三元材料生产企业通过建立粒径分布-振实密度-烧结工艺的关联模型,将材料振实密度从2.2g/cm³提升至2.45g/cm³,对应电池体积能量密度提高8%。金属增材制造行业则通过实施粉末流动性分级系统,将316L不锈钢粉末的振实度稳定在4.8-5.1g/cm³区间,使3D打印件致密度达到99.3%以上。据国际粉末冶金联盟2024年数据显示,采用齐全振实检测技术的企业,其打印件废品率平均降低37个百分点。
多维质量保障体系构建
为确保检测数据的准确性与可比性,行业领先机构已建立三级质量保障机制:第一级实验室层面,执行每日设备点检与标准样品复测,数据偏差超过1%立即启动校准程序;第二级企业层面,构建跨厂区的检测数据云平台,实现工艺参数与物性指标的动态关联分析;第三级行业层面,中国计量科学研究院主导的振实密度能力验证项目,已覆盖85%以上的 认证实验室。这套体系使得不同实验室间的检测结果差异从过去的12%降至3%以内,为行业技术标准统一奠定了基础。
展望未来,随着智能传感技术和数字孪生技术的发展,建议行业从三方面突破:一是开发嵌入式在线检测系统,实现生产过程中的实时密度监控;二是建立多物理场耦合分析模型,将振实密度与粒度形貌、表面特性等参数深度关联;三是推动ISO/TC24国际标准的修订,纳入纳米材料、复合粉末等新型材料的检测规范。只有通过持续的技术迭代和标准升级,才能充分发挥振实密度检测在粉体材料产业升级中的核心价值。
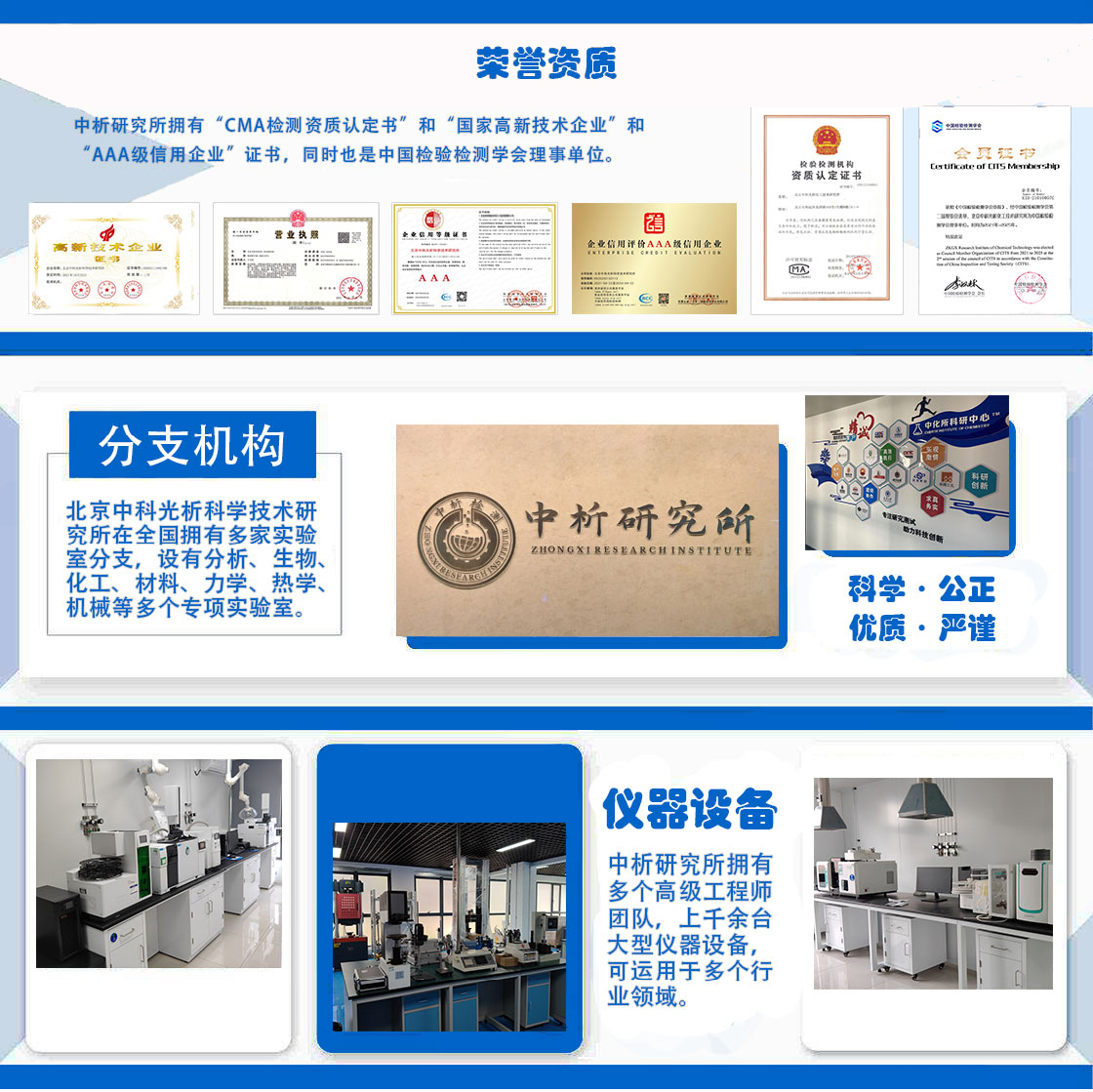
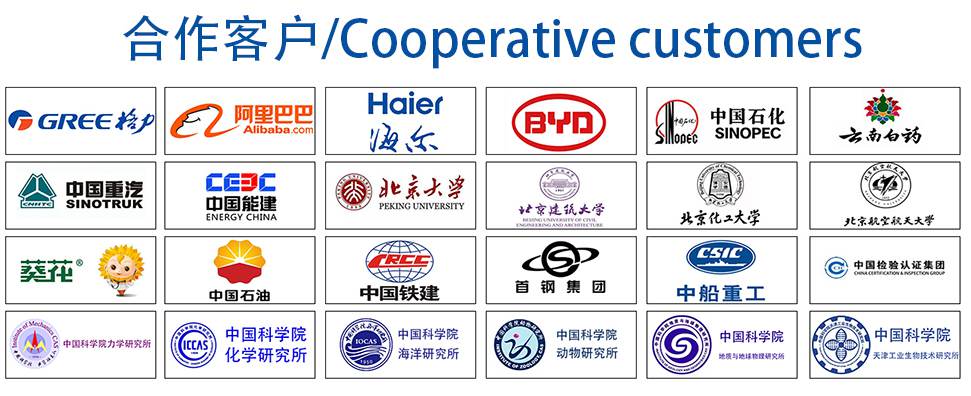