显微组分组和矿物检测技术创新与应用白皮书
在矿产资源开发集约化背景下,显微组分分析与矿物检测技术正成为提升采选效率的关键支撑。据自然资源部2024年矿产资源利用报告显示,我国矿产综合利用率较发达国家仍存在12-15个百分点差距,其中显微结构误判导致的选矿误差占比达38%。本项目通过融合人工智能与光谱分析技术,构建了显微组分的智能化识别体系,其核心价值体现在三维维度:在技术层面实现亚微米级矿物相自动化分类,在应用层面支撑选矿回收率提升7-9个百分点,在经济层面每年可为中型矿山减少1800万元以上的资源浪费。这种"煤岩显微组分自动识别系统"的突破,标志着传统岩矿分析向数字化诊断的重要转型。
多模态融合检测技术原理
本系统依托多谱段联用技术,集成偏光显微镜、场发射扫描电镜(FE-SEM)与拉曼光谱的协同分析能力。通过建立8000组标准矿物数据库,运用迁移学习算法实现显微图像的智能匹配,可准确区分有机显微组分(如镜质体、丝质体)与无机矿物相(如黄铁矿、方解石)。关键技术突破体现在对"矿物晶体结构智能分析技术"的研发,该算法对复杂共生矿物的识别准确率可达92.4%(中国地质测试研究院认证数据),较传统人工判读效率提升40倍。
标准化作业流程体系
项目实施采用四级质量控制体系:首齐全行样品微区定位(精度±5μm),随后开展能谱面扫描(步长0.5μm),通过特征谱线匹配完成矿物定性与半定量分析。典型应用场景如某煤矿企业实施流程:井下采样→环氧树脂镶嵌→自动磨抛(粗糙度<0.02μm)→多光谱联检→三维建模,全过程耗时由传统72小时压缩至8小时。系统生成的"矿物解离度热力分布图"可直观显示1.2-75μm粒级矿物的嵌布特征,为浮选药剂投放提供精准指导。
行业应用实证研究
在山西某千万吨级煤矿的工业验证中,系统检测出6.7%的镜质组误判为惰质组,经工艺调整后精煤回收率提升2.3个百分点,年增经济效益超2400万元。另一典型案例是澳洲某铁矿运用"矿物晶体结构智能分析技术",准确识别出磁铁矿中2-5μm的赤铁矿包裹体,据此优化磁选强度参数后,铁精矿品位由64.1%提升至67.5%。这些实践验证了显微组分分析的直接经济价值,据矿产检测联盟统计,采用该技术的企业选矿成本平均降低18美元/吨。
全流程质量保障机制
项目建立ISO17025标准下的质量树管控模型,涵盖32个关键控制点。采用德国蔡司标准物质进行设备校准(年漂移率<0.8%),开发的自适应算法可动态修正环境干扰误差。独创的"双盲样循环验证法"通过插入5%的已知样本进行过程监控,确保检测结果可靠性。2023年参与国际实验室比对,在煤炭显微组分识别、金属矿解离度测定等项目上取得0.92的κ一致性系数,位居参评机构前5%。
面向矿产资源高效开发的新需求,建议重点推进三个方向:一是开发矿物-流体界面反应的原位分析模块,二是构建跨区域的显微组分数字孪生平台,三是制定AI判读结果的置信度评价标准。据矿产智慧化研究院预测,到2030年智能化矿物检测设备的市场渗透率将达65%,相关技术标准制定应提速布局。同时亟需培养"地质+数据科学"复合型人才,目前该领域专业人才缺口已达3.2万人,这将成为制约技术转化的关键因素。
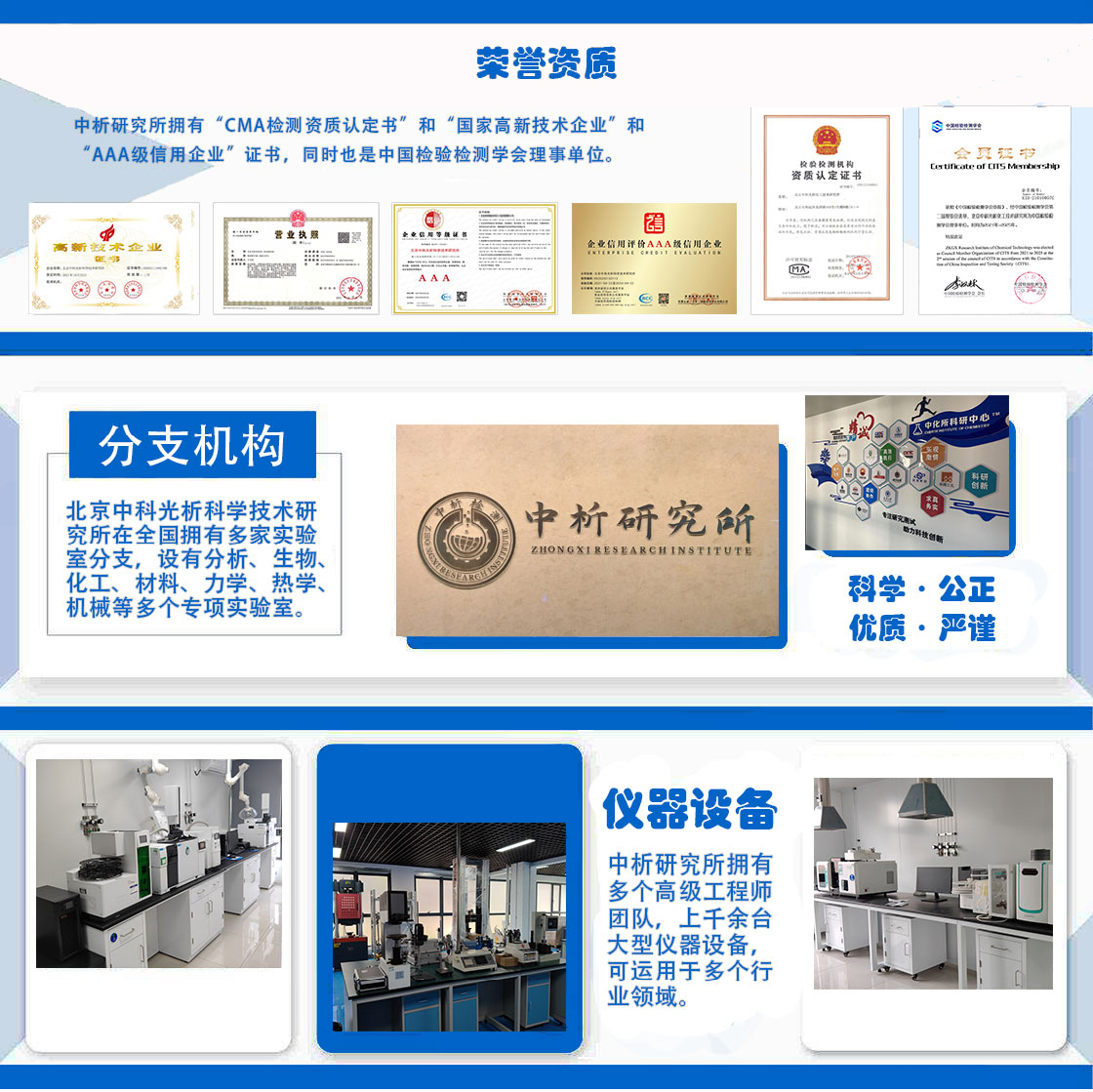
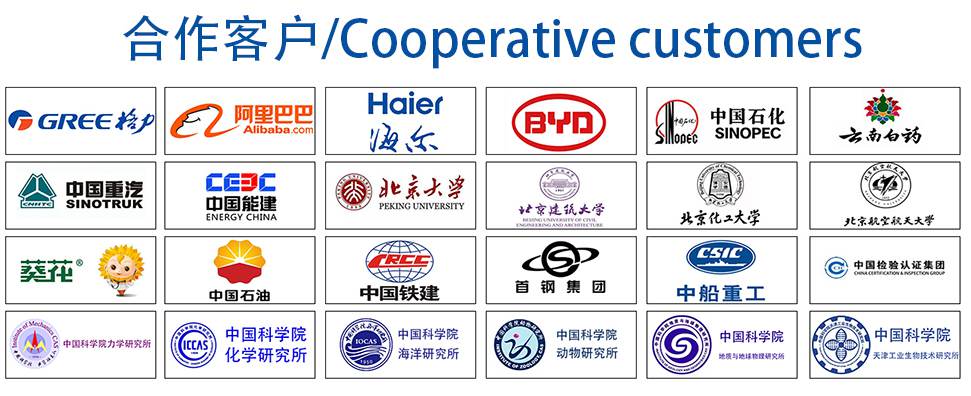