高分子材料检测技术原理
现代汽车塑料检测依托热重-红外联用(TG-FTIR)、动态机械分析(DMA)等核心技术,可精准解析材料分子链运动特性与失效机理。以电池包阻燃壳体检测为例,通过UL94垂直燃烧试验与极限氧指数(LOI)测试,配合扫描电镜(SEM)观察炭层结构,能够实现阻燃剂协同效应的定量评价。值得关注的是,ISO 6721-11:2023新引入的流变学测试方法,可模拟材料在-40℃至120℃交变工况下的蠕变行为,为寒冷地区电动车部件选型提供数据支撑。
全流程检测实施规范
标准化检测流程涵盖原材料入厂验证、成型工艺监控、成品性能评估三大阶段。某德系车企在华工厂的实践表明,实施ASTM D638拉伸试验与ISO 179缺口冲击试验联检后,仪表板聚丙烯材料的断裂伸长率偏差从±15%降至±5%。针对智能座舱触控面板,需额外进行EN 45545-2轨道交通材料防火等级测试,并通过10万次模拟触压的耐疲劳验证。检测机构现普遍采用区块链技术实现数据存证,确保从送样到报告签发的全过程可追溯。
行业典型应用案例
在新能源车领域,某头部电池企业通过实施GB/T 31467.3振动测试与SAE J2522耐化学试剂测试的组合方案,将电池外壳PC/ABS合金的应力开裂率降低82%。传统车企方面,广汽集团采用气相色谱-质谱联用(GC-MS)技术对64种内饰件VOCs释放量进行管控,使座舱空气质量的TVOC值稳定在0.4mg/m³以下(严于国标60%)。这些实践印证了"车用低VOCs高分子材料筛选"技术路线的可行性。
质量保障体系构建
行业领先的检测机构已建立 17025与IATF 16949双体系认证的质控网络。上海某第三方实验室的创新实践显示,运用机器视觉技术对试样断裂面进行智能分析,可使疲劳测试结果的复现性提升至98.7%。针对改性塑料行业特有的"批次稳定性"难题,开发基于近红外光谱(NIRS)的在线监测系统,实现每15秒一次的熔体流动速率(MFR)实时反馈,将生产异常响应时间缩短至传统人工检测的1/20。
## 技术展望与发展建议 随着智能网联汽车对功能集成度的要求提升,建议行业重点发展三项关键技术:一是开发多物理场耦合加速老化试验装置,实现光照、湿热、机械载荷的协同作用模拟;二是建立车规级再生塑料数据库,完善PCR材料在转向机构等安全件中的应用规范;三是推进数字孪生技术在检测领域的应用,通过材料基因组工程预测新型复合材料的服役表现。只有构建"检测-研发-量产"的闭环体系,才能支撑汽车产业在碳中和目标下的可持续发展。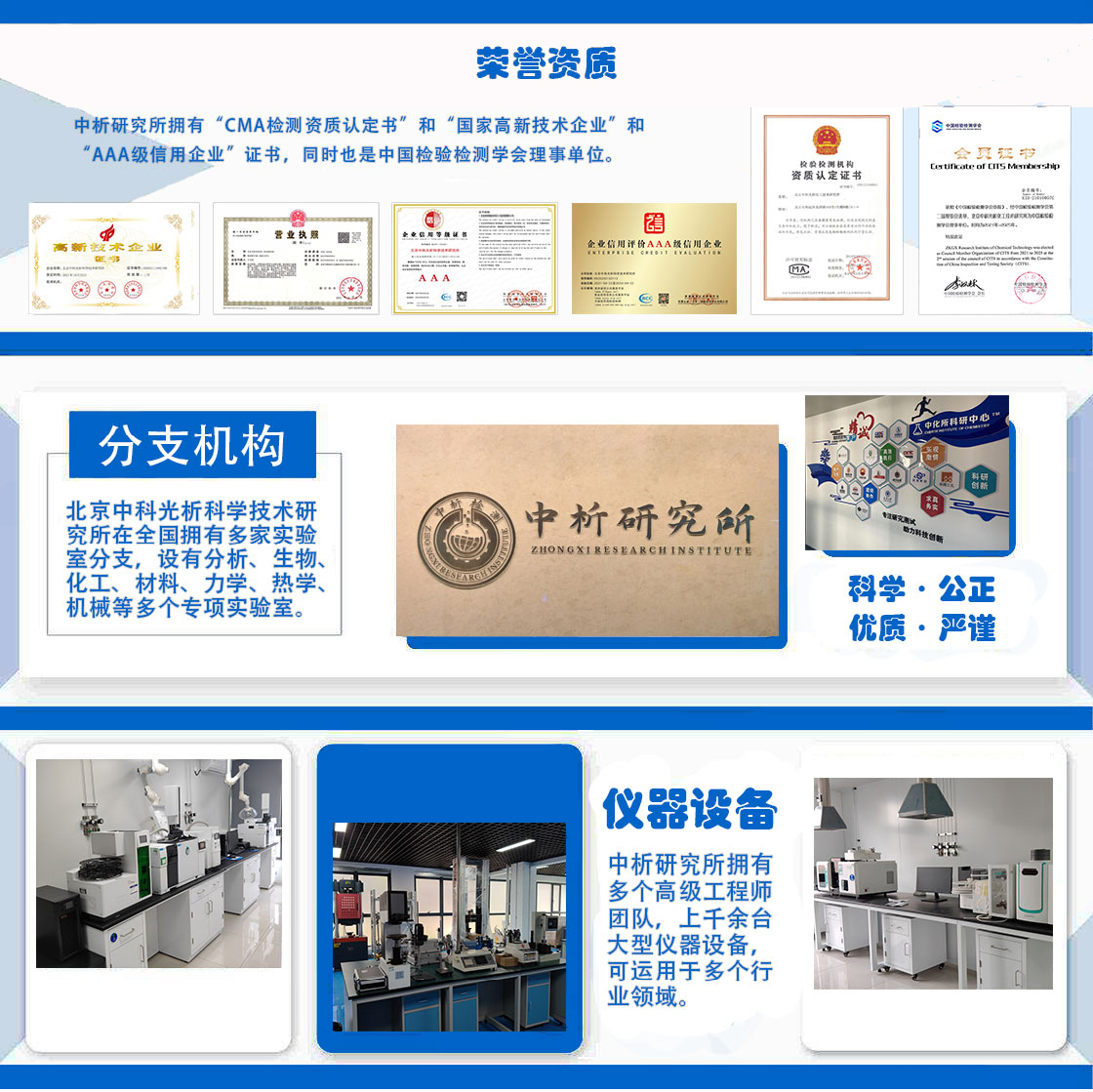
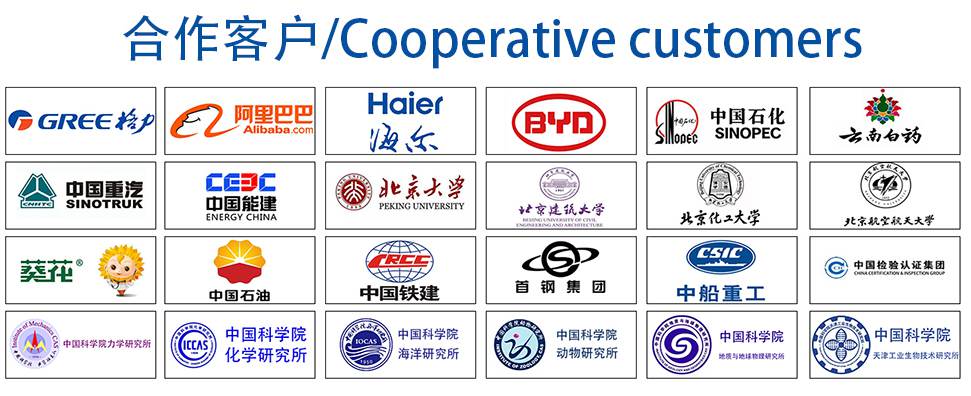