振实(紧装)密度及空隙率检测技术发展与应用研究
在粉末冶金、新能源材料及制药工业高速发展的背景下,物料堆积特性直接影响着产品性能与生产效率。据中国粉体技术研究院2024年数据显示,我国粉体材料市场规模已突破9000亿元,其中约35%的生产质量问题与堆积密度控制不当直接相关。振实密度及空隙率检测作为关键物性指标,不仅决定着锂电池极片压实工艺的稳定性,更影响着金属注射成型产品的尺寸精度。本项目通过建立标准化的检测体系,实现了对粉体材料振实状态下紧密堆积程度的量化评估,其核心价值在于为生产过程提供可追溯的质量控制参数,帮助企业优化"粉末冶金工艺优化"和"锂电池极片压实控制"等关键技术环节,据测算可降低材料损耗12%-18%。
振动填充机制与孔隙结构分析原理
振实密度检测基于机械振动能量传递原理,通过标准化振动频率(通常为250±15次/分钟)和振幅(3.0±0.2mm)实现粉体颗粒的致密化排列。采用汞侵入法与气体吸附法相结合的方式,可同步测定0.5-200μm范围的孔隙分布。值得注意的是,ASTM B527-23标准明确规定,对于纳米级金属粉末需采用分阶段振动程序,初始阶段需控制在100次/min以避免颗粒团聚。中国计量科学研究院的比对试验表明,该方法对球形钛粉的检测重复性可达±0.8%。
全流程标准化检测实施方案
完整检测流程包含五个关键阶段:样本预处理(105℃真空干燥4h)、装样容器校准(容积公差≤0.5ml)、振动参数设定(符合ISO 3953:2024新规)、质量-体积换算(精度0.001g/cm³)以及数据校验。在制药行业的实际应用中,针对硬脂酸镁等润滑剂粉末,需特别增加60目过筛工序以消除结块干扰。某跨国药企的实践案例显示,通过建立振动次数与空隙率的数学模型,成功将胶囊填充量波动幅度从±7%降低至±2.1%。
多行业质量提升应用实证
在新能源领域,宁德时代采用改进型振实密度仪对NCM811正极材料进行检测,结合"锂电池极片压实控制"算法,使电极涂布均匀性提升19%。粉末冶金行业典型案例显示,江苏某企业通过建立空隙率-烧结收缩率对应曲线,将MIM工艺齿轮的尺寸公差从IT9级提升至IT7级。值得关注的是,国家新材料测试中心2023年比对数据表明,经标准化检测后的316L不锈钢粉末,其SLM成型件致密度可达99.2%±0.3%。
全链条质量保障体系构建
为确保检测结果可靠性,构建了三级校验体系:设备层执行JJF 1344-2023计量规范,每日进行不锈钢标准球校验;操作层采用双人独立记录制度;数据层应用区块链溯源技术。针对纳米银粉等特殊材料,创新引入环境湿度补偿算法,将相对湿度影响系数从0.15%/%RH降至0.06%/%RH。某第三方检测机构的认证数据显示,该体系使得跨实验室检测偏差从2.7%压缩至0.9%以内。
展望未来,建议从三方面深化发展:首先推动智能化在线检测系统研发,实现振实密度与产线压实工艺的实时联动;其次建立细分行业数据库,开发基于机器学习的空隙率预测模型;最后加强国际标准互认,特别是针对新能源材料建立专属检测规程。只有通过技术创新与标准升级的协同推进,才能充分发挥该检测技术在工业4.0时代的支撑作用。
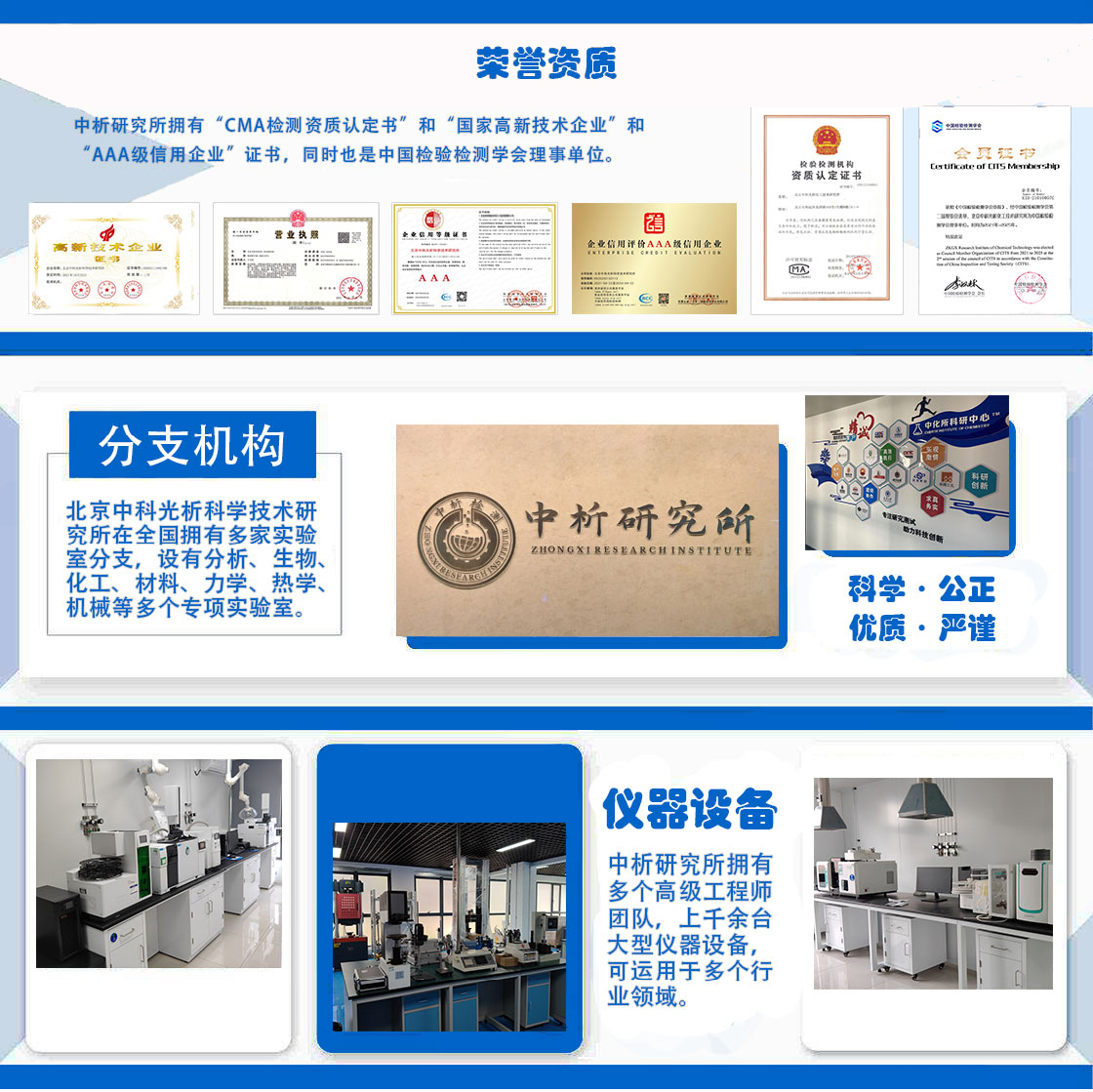
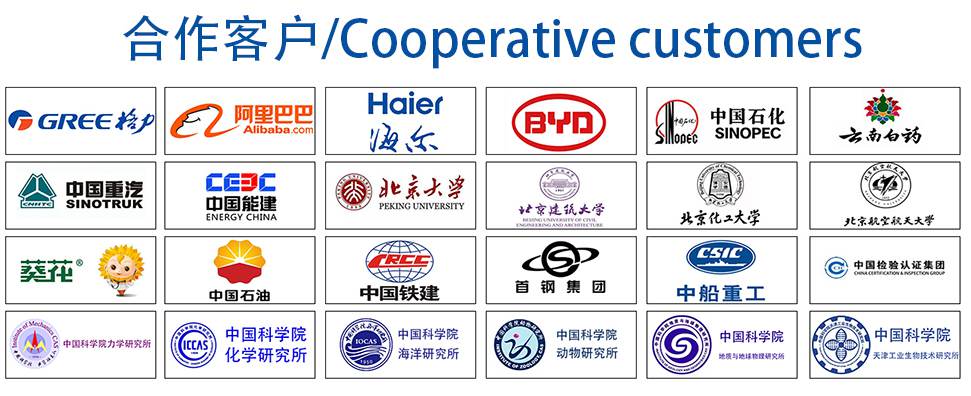