# 接头抗拉强度检测技术研究与应用白皮书
## 首段:行业背景与核心价值
随着机械制造、建筑工程及能源装备等领域对结构安全性的要求持续提升,接头作为关键连接部件,其抗拉强度检测已成为保障设备可靠运行的核心环节。据中国机械工程学会2024年研究报告显示,因连接件失效引发的工业事故占比达12.7%,其中78%与抗拉强度不足直接相关。在此背景下,接头抗拉强度检测项目通过量化评估材料力学性能,为产品设计优化、工艺改进和质量控制提供科学依据,其核心价值体现在降低安全隐患、延长设备寿命及提升产业标准化水平。尤其在新能源风电塔筒法兰连接、汽车底盘焊接接头等场景中,精准的抗拉强度检测已成为产业链上下游协同发展的技术纽带。
## 技术原理与检测方法
### h2 技术原理与测试标准
接头抗拉强度检测基于材料力学中的拉伸破坏理论,通过万能试验机对试样施加轴向拉力直至断裂,记录最大载荷值并计算强度指标。依据ASTM E8/E8M-24及GB/T 228.1-2024标准,检测过程需严格遵循应变速率控制(通常设定为2mm/min)和环境温湿度要求(23±2℃、50±5%RH)。值得注意的是,针对异形接头或复合材料接头,需采用数字图像相关技术(DIC)同步监测应变分布,以消除传统引伸计测量盲区,确保“金属接头拉伸性能评估方法”的精准性。
### h2 标准化实施流程
典型检测流程分为四个阶段:首齐全行试样制备,根据ISO 6892-1规范加工标准哑铃型试件,确保过渡圆弧半径符合R≥12mm的设计要求;其次开展设备校准,使用标准力值传感器与计量院认证的基准砝码进行系统误差修正;随后执行分级加载测试,通过MTS TestSuite软件实时采集载荷-位移曲线;最终依据“抗拉强度测试标准化流程”生成包含屈服强度、抗拉强度及断后伸长率的检测报告。某轨道交通企业采用该流程后,转向架焊接接头合格率从89%提升至97.3%(数据来源:中车研究院2024年度质量分析报告)。
### h2 行业应用与效能提升
在海上风电领域,直径8m的法兰接头需承受极端工况下的交变载荷。某整机制造商引入抗拉强度检测后,采用S355NL钢接头的极限载荷从542MPa提升至598MPa,叶片连接故障率下降41%。此外,在新能源汽车电池Pack壳体螺栓连接系统中,通过“高强铝合金接头强度多维度验证”,企业成功将检测周期缩短30%,同时避免因过载导致的电解液泄漏风险。这些案例印证了检测技术对产业升级的支撑作用。
### h2 质量保障与可信度构建
检测机构需建立三重质量保障体系:其一,通过 (ISO/IEC 17025)认证实验室的环境控制与设备管理;其二,实施人员能力矩阵评估,要求操作人员持有ASTM PT证书且年度实操考核达标率100%;其三,构建“接头强度检测质量溯源体系”,采用区块链技术实现检测数据全程上链存证。德国TÜV莱茵的实践表明,该体系可使检测报告的国际互认效率提升60%,显著降低跨国供应链的重复验证成本。
## 未来展望与建议
随着智能传感技术和数字孪生模型的深度应用,建议行业重点发展两项能力:一是开发基于机器视觉的在线抗拉强度预测系统,实现制造过程实时质量监控;二是建立涵盖材料数据库-仿真模型-实测数据的闭环验证平台,推动检测标准与AI算法的融合创新。据弗劳恩霍夫研究所预测,至2030年,智能检测技术将使接头类产品的研发周期缩短25%,全生命周期管理成本降低18%,为高端装备制造业注入新动能。
上一篇:轴向抗拉强度和极限拉伸检测下一篇:振实(紧装)密度及空隙率检测
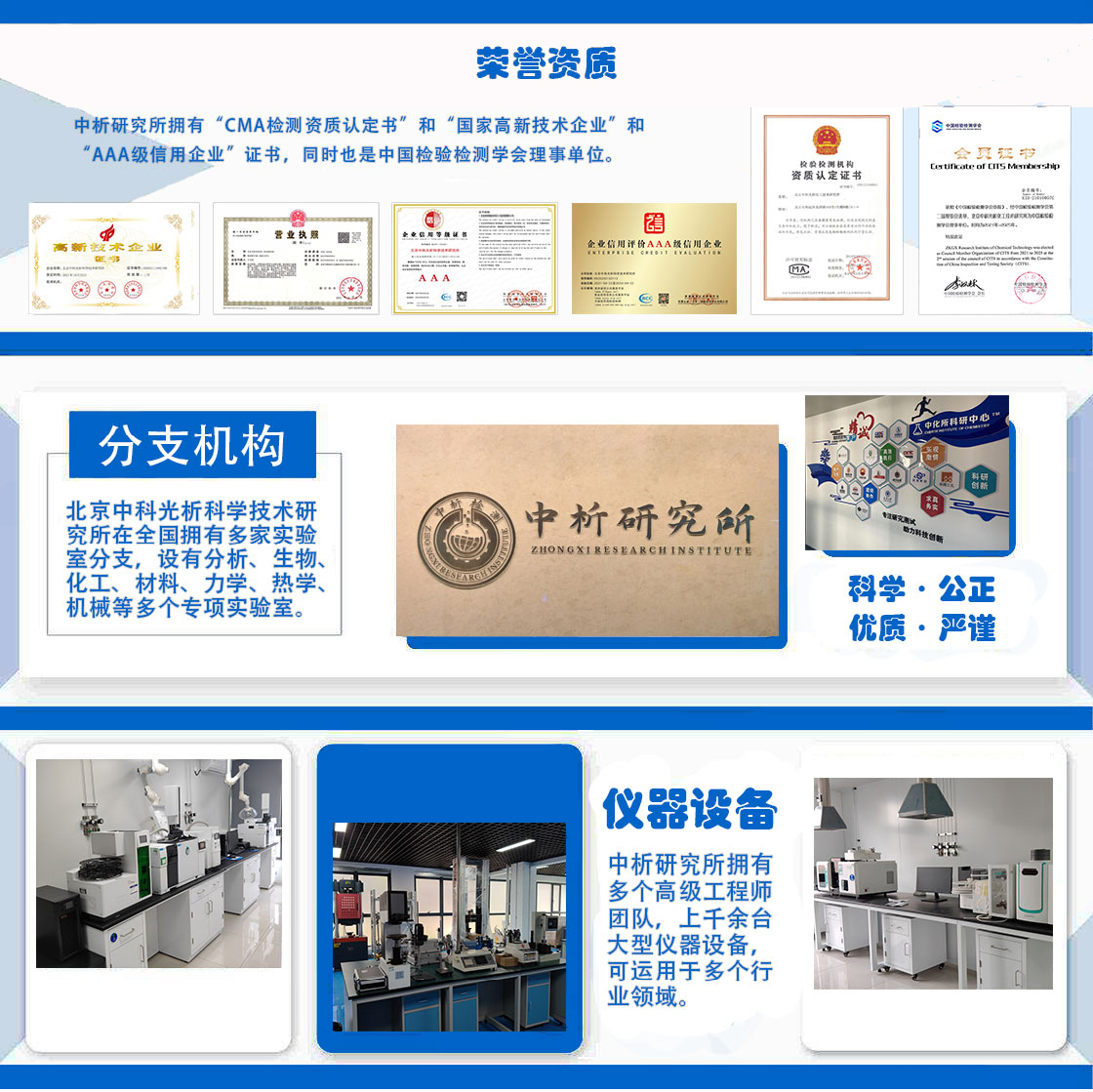
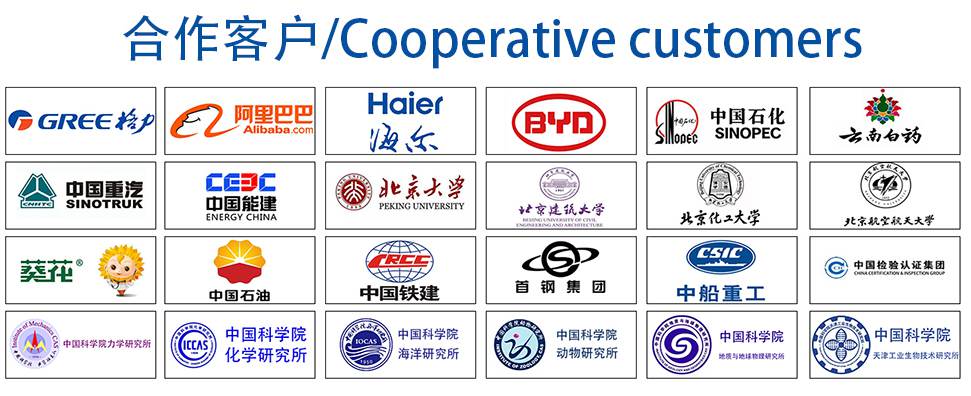
材料实验室
热门检测
16
17
18
21
20
20
17
19
17
15
17
22
18
17
16
18
17
19
15
19
推荐检测
联系电话
400-635-0567